Technology Category
- Functional Applications - Manufacturing Execution Systems (MES)
Applicable Industries
- Aerospace
- Automotive
Applicable Functions
- Product Research & Development
Use Cases
- Additive Manufacturing
- Virtual Prototyping & Product Testing
About The Customer
3D Systems, based in Rock Hill, South Carolina, is a leading innovator in 3D printing technology. The company has a rich history of accomplishments, including the invention of 3D printing with Stereolithography (SLA) and its commercialization in 1989, as well as the invention and commercialization of Selective Laser Sintering (SLS) in 1992. Today, 3D Systems’ wide range of 3D printers are used for production-grade manufacturing in various industries including aerospace, automotive, patient-specific medical devices, and a variety of consumer, electronic, and fashion accessories.
The Challenge
3D Systems, a pioneer in 3D printing technology, was approached by the Cooper Hewitt – Smithsonian Design Museum in New York to participate in an exhibit highlighting innovative software and new manufacturing methods. The challenge was to design and 3D print a structurally sound, lightweight skateboard, a product that has remained largely unchanged for many years. The team at 3D Systems aimed to revolutionize the way a skateboard is designed and produced, with the goal of creating a skateboard lighter than others on the market.
The Solution
To meet this challenge, 3D Systems utilized solidThinking Inspire to optimize the deck and trucks of a traditional skateboard design. The software was used to generate 20-30 different concepts, each of which was analyzed to identify any weak points in the design. The winning concept was then refined into the final design to be 3D printed. The deck of the board was manufactured with PA-12 Nylon using 3D Systems’ Selective Laser Sintering technology, while the trucks were printed in titanium using Direct Metal Printing. Future plans include using Inspire to redesign and print the wheels of the skateboard, and a second version of the skateboard printed using glass filled nylon for increased stiffness.
Operational Impact
Quantitative Benefit
Case Study missing?
Start adding your own!
Register with your work email and create a new case study profile for your business.
Related Case Studies.
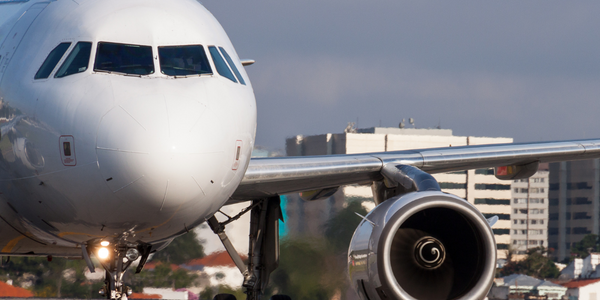
Case Study
Airbus Soars with Wearable Technology
Building an Airbus aircraft involves complex manufacturing processes consisting of thousands of moving parts. Speed and accuracy are critical to business and competitive advantage. Improvements in both would have high impact on Airbus’ bottom line. Airbus wanted to help operators reduce the complexity of assembling cabin seats and decrease the time required to complete this task.
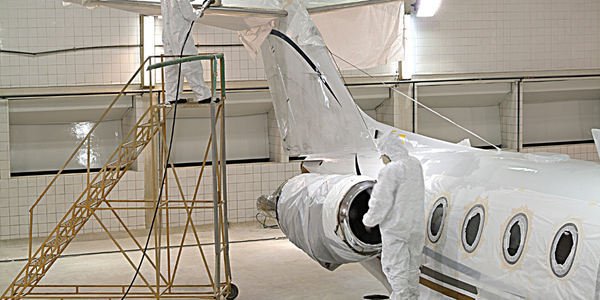
Case Study
Aircraft Predictive Maintenance and Workflow Optimization
First, aircraft manufacturer have trouble monitoring the health of aircraft systems with health prognostics and deliver predictive maintenance insights. Second, aircraft manufacturer wants a solution that can provide an in-context advisory and align job assignments to match technician experience and expertise.
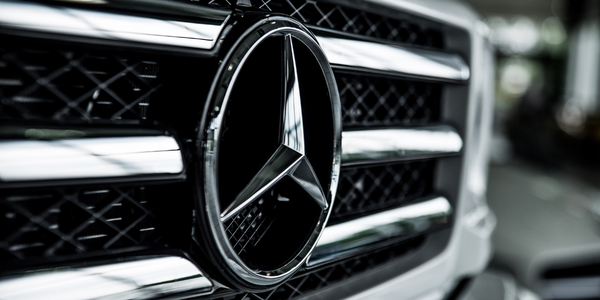
Case Study
Integral Plant Maintenance
Mercedes-Benz and his partner GAZ chose Siemens to be its maintenance partner at a new engine plant in Yaroslavl, Russia. The new plant offers a capacity to manufacture diesel engines for the Russian market, for locally produced Sprinter Classic. In addition to engines for the local market, the Yaroslavl plant will also produce spare parts. Mercedes-Benz Russia and his partner needed a service partner in order to ensure the operation of these lines in a maintenance partnership arrangement. The challenges included coordinating the entire maintenance management operation, in particular inspections, corrective and predictive maintenance activities, and the optimizing spare parts management. Siemens developed a customized maintenance solution that includes all electronic and mechanical maintenance activities (Integral Plant Maintenance).
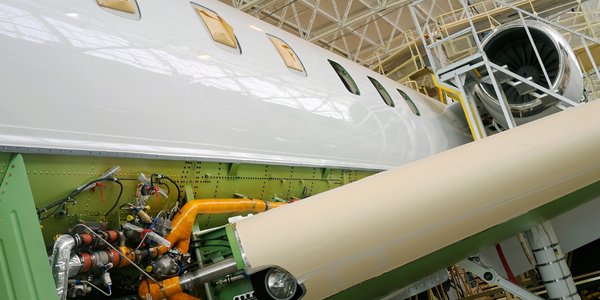
Case Study
Aerospace & Defense Case Study Airbus
For the development of its new wide-body aircraft, Airbus needed to ensure quality and consistency across all internal and external stakeholders. Airbus had many challenges including a very aggressive development schedule and the need to ramp up production quickly to satisfy their delivery commitments. The lack of communication extended design time and introduced errors that drove up costs.