Customer Company Size
Mid-size Company
Region
- America
Country
- United States
Product
- Chempax
Tech Stack
- Database Management
Implementation Scale
- Enterprise-wide Deployment
Impact Metrics
- Productivity Improvements
- Customer Satisfaction
Technology Category
- Application Infrastructure & Middleware - Data Exchange & Integration
Applicable Industries
- Chemicals
- Automotive
- Pharmaceuticals
Applicable Functions
- Discrete Manufacturing
Use Cases
- Inventory Management
- Supply Chain Visibility
Services
- System Integration
- Training
About The Customer
Superior Oil Company is a leading provider of chemical products in the Midwest. As an independent chemical distributor, Superior provides industrial solvents and chemicals, water-based cleaners, heat exchange fluids and fiberglass composites to a diverse range of industries. The company was established in 1932 and has 11 locations in North America, with its headquarters in Indianapolis, IN. The industries served by Superior include Adhesives, Automotive, Chemicals, Fiberglass Reinforced Plastics, Foundry, I & I Compounders, Metal Fabricating, Painting & Coatings, Pharmaceutical, and Printing.
The Challenge
Superior Oil Company, a distributor, manufacturer and waste recycler, was facing challenges with its inventory and customer data management across its multiple locations. The company was unable to view inventory or customer data from other locations, leading to constant calls to gather this information. Additionally, the company was using 9 different databases for each of its locations, leading to inefficiencies and inconsistencies in data management. The company was also facing issues with its financial reporting, taking up to 3 weeks to get financials with their previous system. They were also doing manual double entries for all of their accounting.
The Solution
Superior Oil Company chose to implement Chempax, a software solution built specifically for the chemical industry. The software's customer service module, with its connection into manufacturing, purchasing and inventory control, was particularly impressive. With Chempax, Superior was able to consolidate its 9 databases into one standardized database for all locations. This change significantly improved the company's customer service, inventory and manufacturing capabilities. The accounting function in Chempax allowed the company to get financial information within days at the end of each month, as opposed to the 3 weeks it took with their previous system. The software also eliminated the need for manual double entries for accounting, increasing productivity and efficiency. The reporting functionality of Chempax, including product usage reports, improved the company's operations.
Operational Impact
Quantitative Benefit
Case Study missing?
Start adding your own!
Register with your work email and create a new case study profile for your business.
Related Case Studies.
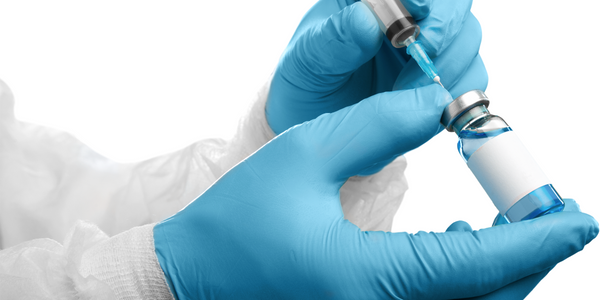
Case Study
Case Study: Pfizer
Pfizer’s high-performance computing software and systems for worldwide research and development support large-scale data analysis, research projects, clinical analytics, and modeling. Pfizer’s computing services are used across the spectrum of research and development efforts, from the deep biological understanding of disease to the design of safe, efficacious therapeutic agents.
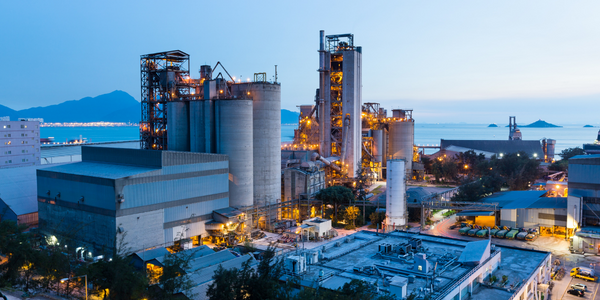
Case Study
Honeywell - Tata Chemicals Improves Data Accessibility with OneWireless
Tata was facing data accessibility challenges in the cement plant control room tapping signals from remote process control areas and other distant locations, including the gas scrubber. Tata needed a wireless solution to extend its control network securely to remote locations that would also provide seamless communication with existing control applications.
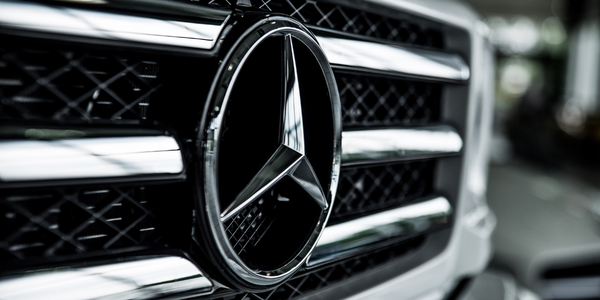
Case Study
Integral Plant Maintenance
Mercedes-Benz and his partner GAZ chose Siemens to be its maintenance partner at a new engine plant in Yaroslavl, Russia. The new plant offers a capacity to manufacture diesel engines for the Russian market, for locally produced Sprinter Classic. In addition to engines for the local market, the Yaroslavl plant will also produce spare parts. Mercedes-Benz Russia and his partner needed a service partner in order to ensure the operation of these lines in a maintenance partnership arrangement. The challenges included coordinating the entire maintenance management operation, in particular inspections, corrective and predictive maintenance activities, and the optimizing spare parts management. Siemens developed a customized maintenance solution that includes all electronic and mechanical maintenance activities (Integral Plant Maintenance).