Technology Category
- Sensors - Temperature Sensors
- Wearables - Exoskeletons
Applicable Industries
- Buildings
- Construction & Infrastructure
Applicable Functions
- Procurement
- Product Research & Development
Use Cases
- Building Automation & Control
- Structural Health Monitoring
About The Customer
The customer in this case study is the Laboratory for Visionary Architecture (LAVA). LAVA incorporates patterns of nature organization with future technologies to evolve structures and achieve more efficient architectures with less material. LAVA strives to explore and create new forms of design that enhances reality and reflects the environment in every architectural project. LAVA has completed various projects ranging from installations to urban centers, and furniture to airports. The Bionic Tower is a symbol of LAVA’s visions of tomorrow’s architecture. The design unifies nature’s organization system with advanced computing technology, to achieve an architectural expression of ultimate lightness, efficiency, and sophistication.
The Challenge
The Bionic Tower, a high-rise tower proposal in Abu Dhabi designed by the Laboratory for Visionary Architecture (LAVA), is a symbol of LAVA’s visions of tomorrow’s architecture. The design unifies nature’s organization system with advanced computing technology, to achieve an architectural expression of ultimate lightness, efficiency, and sophistication. The structural expression of this architecture is a proposed organic exoskeleton which acts to structurally stabilize the building. The major challenge was to generate a unique structural form that is lightweight and organic in appearance in order to achieve the free-form exoskeleton structure.
The Solution
James Kingman, a graduate of the School of Civil Engineering Master Degree program at the University of Leeds, took the geometry of the CAD model provided by LAVA and created his own finite element model using Altair HyperWorks. Loading and boundary conditions were applied to the model representing gravity and environmental loading along with idealized foundation support. He conceptualized the building structure as a central core braced by the external exoskeleton. He undertook a series of studies using Optistruct, Altair's structural analysis and optimization solver, to investigate how topology optimization could be used to develop the design of the exoskeleton structure. The entire building envelope was defined as a designable domain in the topology optimization. A sensitivity study was undertaken and it was found that finite elements with a nominal size of approximately one meter produced satisfactory results. The automatic mesh generation process created a mesh composed of approximately 100,000 finite elements.
Operational Impact
Quantitative Benefit
Case Study missing?
Start adding your own!
Register with your work email and create a new case study profile for your business.
Related Case Studies.
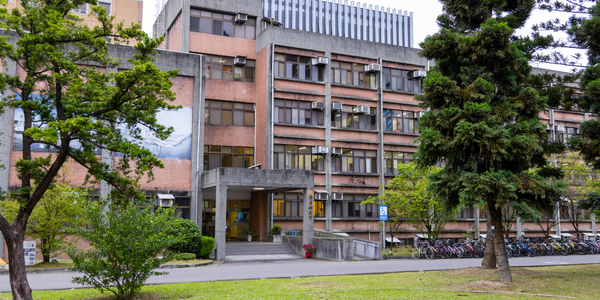
Case Study
Energy Saving & Power Monitoring System
Recently a university in Taiwan was experiencing dramatic power usage increases due to its growing number of campus buildings and students. Aiming to analyze their power consumption and increase their power efficiency across 52 buildings, the university wanted to build a power management system utilizing web-based hardware and software. With these goals in mind, they contacted Advantech to help them develop their system and provide them with the means to save energy in the years to come.
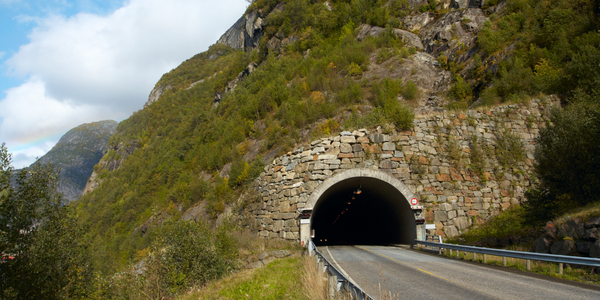
Case Study
IoT System for Tunnel Construction
The Zenitaka Corporation ('Zenitaka') has two major business areas: its architectural business focuses on structures such as government buildings, office buildings, and commercial facilities, while its civil engineering business is targeted at structures such as tunnels, bridges and dams. Within these areas, there presented two issues that have always persisted in regard to the construction of mountain tunnels. These issues are 'improving safety" and "reducing energy consumption". Mountain tunnels construction requires a massive amount of electricity. This is because there are many kinds of electrical equipment being used day and night, including construction machinery, construction lighting, and ventilating fan. Despite this, the amount of power consumption is generally not tightly managed. In many cases, the exact amount of power consumption is only ascertained when the bill from the power company becomes available. Sometimes, corporations install demand-monitoring equipment to help curb the maximum power demanded. However, even in these cases, the devices only allow the total volume of power consumption to be ascertained, or they may issue warnings to prevent the contracted volume of power from being exceeded. In order to tackle the issue of reducing power consumption, it was first necessary to obtain an accurate breakdown of how much power was being used in each particular area. In other words, we needed to be able to visualize the amount of power being consumed. Safety, was also not being managed very rigorously. Even now, tunnel construction sites often use a 'name label' system for managing entry into the work site. Specifically, red labels with white reverse sides that bear the workers' names on both sides are displayed at the tunnel work site entrance. The workers themselves then flip the name label to the appropriate side when entering or exiting from the work site to indicate whether or not they are working inside the tunnel at any given time. If a worker forgets to flip his or her name label when entering or exiting from the tunnel, management cannot be performed effectively. In order to tackle the challenges mentioned above, Zenitaka decided to build a system that could improve the safety of tunnel construction as well as reduce the amount of power consumed. In other words, this new system would facilitate a clear picture of which workers were working in each location at the mountain tunnel construction site, as well as which processes were being carried out at those respective locations at any given time. The system would maintain the safety of all workers while also carefully controlling the electrical equipment to reduce unnecessary power consumption. Having decided on the concept, our next concern was whether there existed any kind of robust hardware that would not break down at the construction work site, that could move freely in response to changes in the working environment, and that could accurately detect workers and vehicles using radio frequency identification (RFID). Given that this system would involve many components that were new to Zenitaka, we decided to enlist the cooperation of E.I.Sol Co., Ltd. ('E.I.Sol') as our joint development partner, as they had provided us with a highly practical proposal.
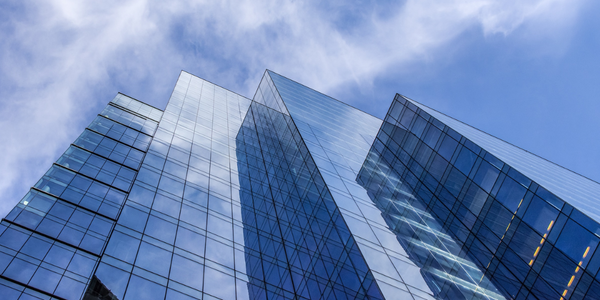
Case Study
Intelligent Building Automation System and Energy Saving Solution
One of the most difficult problems facing the world is conserving energy in buildings. However, it is not easy to have a cost-effective solution to reduce energy usage in a building. One solution for saving energy is to implement an intelligent building automation system (BAS) which can be controlled according to its schedule. In Indonesia a large university with a five floor building and 22 classrooms wanted to save the amount of energy being used.
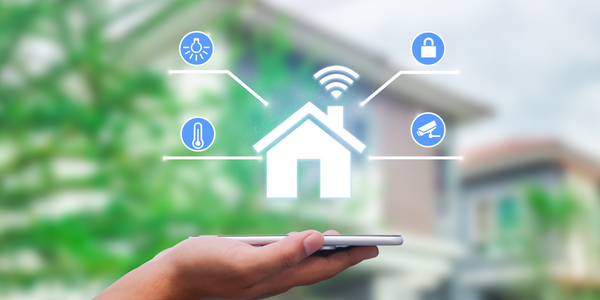
Case Study
Powering Smart Home Automation solutions with IoT for Energy conservation
Many industry leaders that offer Smart Energy Management products & solutions face challenges including:How to build a scalable platform that can automatically scale-up to on-board ‘n’ number of Smart home devicesData security, solution availability, and reliability are the other critical factors to deal withHow to create a robust common IoT platform that handles any kind of smart devicesHow to enable data management capabilities that would help in intelligent decision-making
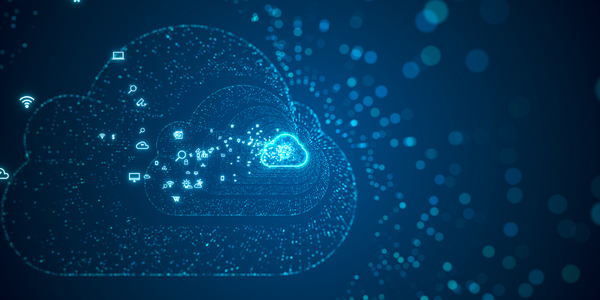
Case Study
Splunk Partnership Ties Together Big Data & IoT Services
Splunk was faced with the need to meet emerging customer demands for interfacing IoT projects to its suite of services. The company required an IoT partner that would be able to easily and quickly integrate with its Splunk Enterprise platform, rather than allocating development resources and time to building out an IoT interface and application platform.