Technology Category
- Analytics & Modeling - Digital Twin / Simulation
- Processors & Edge Intelligence - Microcontrollers & Printed Circuit Boards
Applicable Industries
- Consumer Goods
- Electronics
Applicable Functions
- Product Research & Development
- Quality Assurance
Use Cases
- Time Sensitive Networking
- Virtual Prototyping & Product Testing
Services
- System Integration
- Testing & Certification
About The Customer
LG Electronics Inc. is a global leader and technology innovator in consumer electronics, mobile communications, and home appliances. With annual worldwide sales of $45.22 billion in 2012, LG is one of the industry’s leading producers of flat panel TVs, mobile devices, air conditioners, washing machines, and refrigerators. The company is constantly developing new versions of smartphones, making it one of the fastest-selling, most rapidly evolving, and most competitive products in the electronics industry. The company's profitability, positioning, and reputation among consumers are significantly impacted by the time to market for new models.
The Challenge
The smartphone industry is one of the fastest evolving and most competitive sectors in the electronics industry. New models are developed every few months, and any reduction in time to market can significantly impact a manufacturer's profitability, positioning, and reputation. However, certain aspects of the development process, such as drop-test simulation, have remained time-consuming and resistant to acceleration. Drop-test simulation is a crucial element in ensuring the quality and robustness of a smartphone. Despite using computer simulation for virtual drop testing, LG Electronics (LGE) faced challenges in shortening the simulation time due to the large number of parts and assemblies in smartphones, the time-consuming geometry cleanup, simplification, and meshing, and the multitude of contact definitions that required many manual steps. Thorough testing involves a variety of drop and bending conditions, where analysis setup is time-intensive. Post-processing and generating reports also contributed to the overall time to achieve results. On average, drop-test simulation took one to two weeks to set up, conduct, and analyze, with modeling and post-processing representing 60 to 80 percent of the time invested.
The Solution
In collaboration with Altair, LGE aimed to create a seamlessly integrated drop-test simulation automation system that would enable LGE engineers to conduct virtual smartphone drop tests within just 24 hours. This methodology, incorporating modeling and drop and bending analysis, was expected to significantly speed up the development process and provide a substantial competitive advantage for LGE. The Altair-LGE team developed a way to automatically simplify geometry, create solder joints, generate high-quality meshes, and create contacts between parts using Altair’s HyperWorks computer-aided engineering suite. This suite includes HyperMesh for pre-processing, the RADIOSS solver, HyperView for post-processing, and its embedded automation framework. The automated system developed by the Altair-LGE team requires only a few hours and is a fully integrated, end-to-end, and user-friendly system that can simulate drop and bending test scenarios. The system also promotes standardization, reliability, and repeatability of the drop and bending analyses.
Operational Impact
Quantitative Benefit
Case Study missing?
Start adding your own!
Register with your work email and create a new case study profile for your business.
Related Case Studies.
.png)
Case Study
Improving Vending Machine Profitability with the Internet of Things (IoT)
The vending industry is undergoing a sea change, taking advantage of new technologies to go beyond just delivering snacks to creating a new retail location. Intelligent vending machines can be found in many public locations as well as company facilities, selling different types of goods and services, including even computer accessories, gold bars, tickets, and office supplies. With increasing sophistication, they may also provide time- and location-based data pertaining to sales, inventory, and customer preferences. But at the end of the day, vending machine operators know greater profitability is driven by higher sales and lower operating costs.
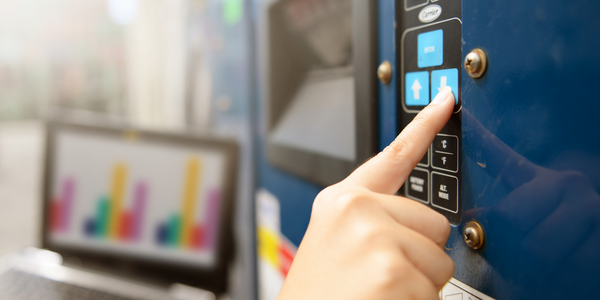
Case Study
Remote Temperature Monitoring of Perishable Goods Saves Money
RMONI was facing temperature monitoring challenges in a cold chain business. A cold chain must be established and maintained to ensure goods have been properly refrigerated during every step of the process, making temperature monitoring a critical business function. Manual registration practice can be very costly, labor intensive and prone to mistakes.
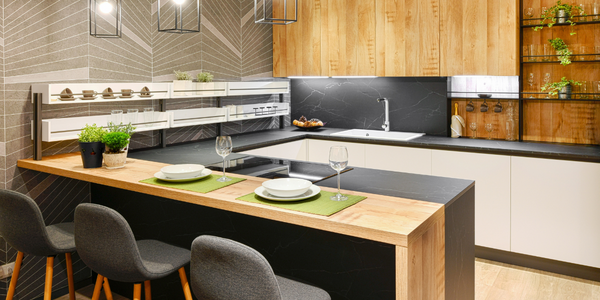
Case Study
Series Production with Lot-size-1 Flexibility
Nobilia manufactures customized fitted kitchens with a lot size of 1. They require maximum transparency of tracking design data and individual processing steps so that they can locate a particular piece of kitchen furniture in the sequence of processes.