Technology Category
- Sensors - Acoustic Sensors
- Sensors - Haptic Sensors
Applicable Industries
- Automotive
- Packaging
Applicable Functions
- Product Research & Development
- Quality Assurance
Use Cases
- Predictive Maintenance
- Time Sensitive Networking
Services
- Testing & Certification
About The Customer
Trèves Products Services & Innovation is a France-based company with a turnover of €580 million in 2021. As one of the leading Tier-1 suppliers of noise, vibration, and harshness (NVH) reduction parts, Trèves provides full sound packages for the trunk, body, interior, and powertrain. The company employs 4,900 people, including 300 R&D engineers located across 9 technical centers, with 26 plants in 17 countries. They work to meet the requirements of their 15+ OEM customers. Trèves has numerous specialists in the characterization and modeling of poro-elastic sound packages and has been successfully using AlphaCell for over 5 years.
The Challenge
Trèves Products Services & Innovation, a leading Tier-1 supplier of noise, vibration, and harshness (NVH) reduction parts, was facing a challenge in reducing part design and lead time. The traditional approach required expensive and time-consuming physical testing with real parts to account for their multi-layer arrangement and varying thickness. The input parameters for these models also needed to be readily available. Furthermore, the models had to be comprehensive in scope and easy to implement. With the upcoming reduction in pass-by noise emission limits from 70 to 68 dB, expected in 2024, the ability to accurately predict noise levels became essential. The challenge was to replace physical testing with numerical modeling to meet customer expectations and regulatory requirements.
The Solution
Trèves turned to AlphaCell from Matelys-Research Lab, available via the Altair Partner Alliance (APA), to address their challenge. AlphaCell offered several features that met Trèves’ needs, including the ability to predict within seconds the response of multi-layer configurations in diffuse sound field conditions, such as those encountered in an alpha-cabin test. The effect of varying thicknesses was accounted for in a fast, user-friendly manner with any compressed part predicted from the initial material properties. The model’s acoustic input parameters were determined via a dedicated characterization process mastered at Trèves using the Matelys software suite and equipment. Simulation results were easily compared with measured data using the model’s intuitive drag and drop interface. In this project, data for flat samples produced in several thicknesses were compared with real engine hood parts.
Operational Impact
Quantitative Benefit
Case Study missing?
Start adding your own!
Register with your work email and create a new case study profile for your business.
Related Case Studies.
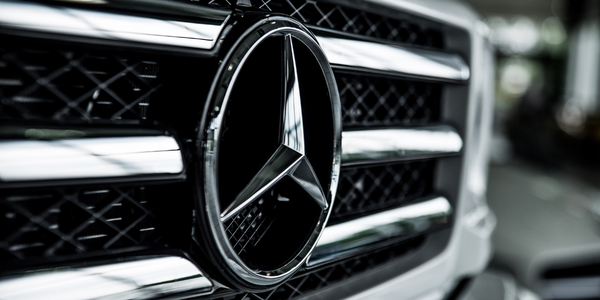
Case Study
Integral Plant Maintenance
Mercedes-Benz and his partner GAZ chose Siemens to be its maintenance partner at a new engine plant in Yaroslavl, Russia. The new plant offers a capacity to manufacture diesel engines for the Russian market, for locally produced Sprinter Classic. In addition to engines for the local market, the Yaroslavl plant will also produce spare parts. Mercedes-Benz Russia and his partner needed a service partner in order to ensure the operation of these lines in a maintenance partnership arrangement. The challenges included coordinating the entire maintenance management operation, in particular inspections, corrective and predictive maintenance activities, and the optimizing spare parts management. Siemens developed a customized maintenance solution that includes all electronic and mechanical maintenance activities (Integral Plant Maintenance).

Case Study
IoT Data Analytics Case Study - Packaging Films Manufacturer
The company manufactures packaging films on made to order or configure to order basis. Every order has a different set of requirements from the product characteristics perspective and hence requires machine’s settings to be adjusted accordingly. If the film quality does not meet the required standards, the degraded quality impacts customer delivery causes customer dissatisfaction and results in lower margins. The biggest challenge was to identify the real root cause and devise a remedy for that.

Case Study
Monitoring of Pressure Pumps in Automotive Industry
A large German/American producer of auto parts uses high-pressure pumps to deburr machined parts as a part of its production and quality check process. They decided to monitor these pumps to make sure they work properly and that they can see any indications leading to a potential failure before it affects their process.