Product
- FORCAM FORCE
- REPORTING & VISUALIZATION module
Tech Stack
- Service-Oriented Architecture (SOA)
- Manufacturing Execution System (MES)
Implementation Scale
- Enterprise-wide Deployment
Impact Metrics
- Productivity Improvements
- Cost Savings
Technology Category
- Application Infrastructure & Middleware - Data Exchange & Integration
Applicable Functions
- Discrete Manufacturing
- Quality Assurance
Use Cases
- Manufacturing System Automation
- Predictive Maintenance
Services
- System Integration
- Software Design & Engineering Services
About The Customer
The customer in this case study is a market-leading machinery firm. The production manager of the firm was convinced that production could become even more efficient to save costs and resources despite the complexity of the manufacturing process. Once a year, a prominent ITConsulting firm offered advice on how to optimize the value chain and subsequently, the productivity by more than 20%. Such high gains in productivity were achieved through the reduction of waiting and downtimes, leading to increased machine availability. Results however were affected by frequent new product introductions and shorter product life cycles.
The Challenge
The manufacturing industry is facing an abundance of complexity, which becomes more apparent with frequent product innovation and shorter product life cycles. Digitization and the ability to access information from anywhere and at any time are changing the rules in almost all sectors. Manufacturers must accelerate production cycles and distributors must shorten delivery times. In response to changing dynamics involving savvy consumer expectations, time to market, and intense global competition coupled with the Internet of Things and mobile technologies, the entire supply chain ecosystem is undergoing a vast transformation. With the many meanings of digital transformation at innovative companies, to remain competitive means to uncover potential for increased productivity and to unleash the hidden factory. Hard facts from machine data must be accessed, understood, and evaluated for effective intervention.
The Solution
The solution to the challenge was the implementation of the FORCAM FORCE solution, specifically the “REPORTING & VISUALIZATION” module. This tool offers critical information on the production process in real-time alongside key performance indicators (KPI) delivered to all devices in use by the shop floor and management personnel today. The firm deployed a Quality Management System (QMS) alongside a powerful SAP ERP system. The production manager and IT-department were in agreement that just a monolithic IT-system was NOT sufficient to integrate all generated data from planning - design - assembly - to production across the company. The overall design of the system should ensure that interoperability with other systems is adhered to at all times and that it corresponds with the conventional automation pyramid in use.
Operational Impact
Quantitative Benefit
Case Study missing?
Start adding your own!
Register with your work email and create a new case study profile for your business.
Related Case Studies.
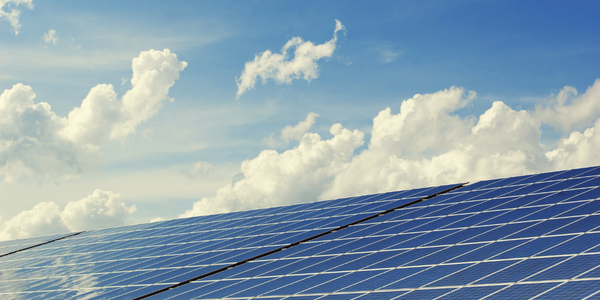
Case Study
Remote Monitoring & Predictive Maintenance App for a Solar Energy System
The maintenance & tracking of various modules was an overhead for the customer due to the huge labor costs involved. Being an advanced solar solutions provider, they wanted to ensure early detection of issues and provide the best-in-class customer experience. Hence they wanted to automate the whole process.
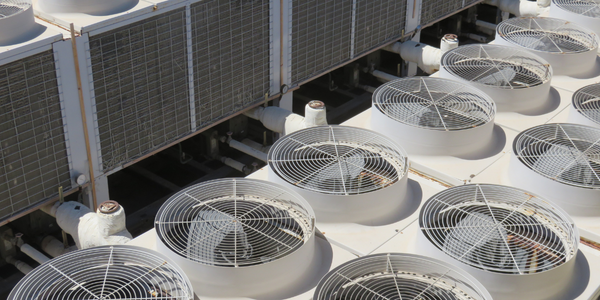
Case Study
Predictive Maintenance for Industrial Chillers
For global leaders in the industrial chiller manufacturing, reliability of the entire production process is of the utmost importance. Chillers are refrigeration systems that produce ice water to provide cooling for a process or industrial application. One of those leaders sought a way to respond to asset performance issues, even before they occur. The intelligence to guarantee maximum reliability of cooling devices is embedded (pre-alarming). A pre-alarming phase means that the cooling device still works, but symptoms may appear, telling manufacturers that a failure is likely to occur in the near future. Chillers who are not internet connected at that moment, provide little insight in this pre-alarming phase.
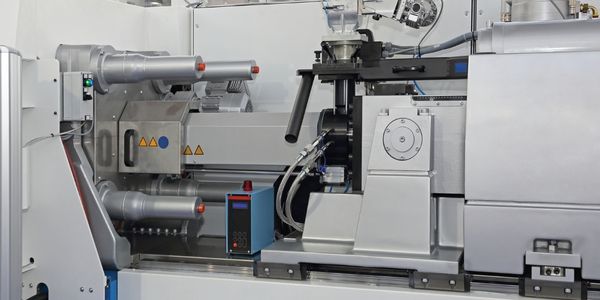
Case Study
Plastic Spoons Case study: Injection Moulding
In order to meet customer expectations by supplying a wide variety of packaging units, from 36 to 1000 spoons per package, a new production and packaging line needed to be built. DeSter wanted to achieve higher production capacity, lower cycle time and a high degree of operator friendliness with this new production line.
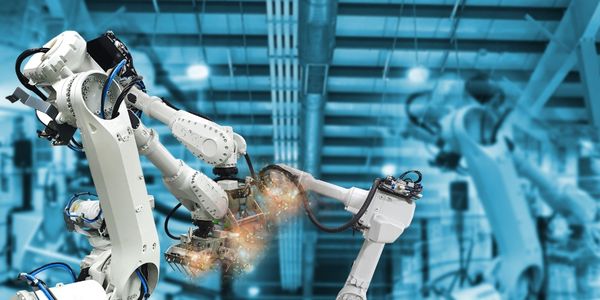
Case Study
Robot Saves Money and Time for US Custom Molding Company
Injection Technology (Itech) is a custom molder for a variety of clients that require precision plastic parts for such products as electric meter covers, dental appliance cases and spools. With 95 employees operating 23 molding machines in a 30,000 square foot plant, Itech wanted to reduce man hours and increase efficiency.
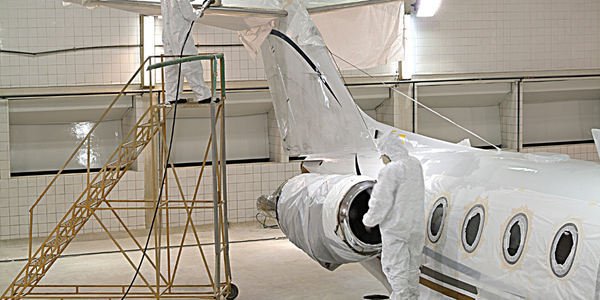
Case Study
Aircraft Predictive Maintenance and Workflow Optimization
First, aircraft manufacturer have trouble monitoring the health of aircraft systems with health prognostics and deliver predictive maintenance insights. Second, aircraft manufacturer wants a solution that can provide an in-context advisory and align job assignments to match technician experience and expertise.
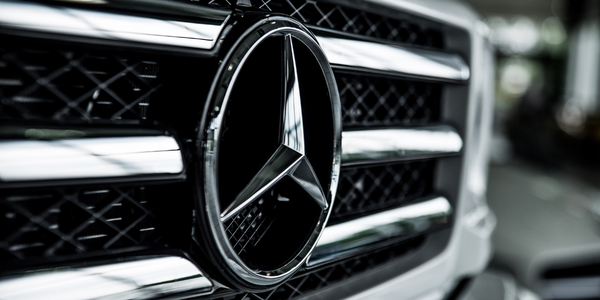
Case Study
Integral Plant Maintenance
Mercedes-Benz and his partner GAZ chose Siemens to be its maintenance partner at a new engine plant in Yaroslavl, Russia. The new plant offers a capacity to manufacture diesel engines for the Russian market, for locally produced Sprinter Classic. In addition to engines for the local market, the Yaroslavl plant will also produce spare parts. Mercedes-Benz Russia and his partner needed a service partner in order to ensure the operation of these lines in a maintenance partnership arrangement. The challenges included coordinating the entire maintenance management operation, in particular inspections, corrective and predictive maintenance activities, and the optimizing spare parts management. Siemens developed a customized maintenance solution that includes all electronic and mechanical maintenance activities (Integral Plant Maintenance).