Customer Company Size
Large Corporate
Region
- Europe
- America
Country
- France
- Canada
- United Kingdom
Product
- 3DEXPERIENCE platform
- CATIA
- ENOVIA V6
- SIMULIA
- DELMIA V6
- 3DVIA
Tech Stack
- Design software
- Data management software
- Simulation and analysis software
- Manufacturing and documentation software
Implementation Scale
- Enterprise-wide Deployment
Impact Metrics
- Productivity Improvements
- Innovation Output
Technology Category
- Platform as a Service (PaaS) - Application Development Platforms
- Platform as a Service (PaaS) - Data Management Platforms
- Analytics & Modeling - Digital Twin / Simulation
- Functional Applications - Product Lifecycle Management Systems (PLM)
Applicable Industries
- Aerospace
- National Security & Defense
Applicable Functions
- Discrete Manufacturing
- Product Research & Development
Use Cases
- Manufacturing System Automation
- Digital Twin
- Virtual Prototyping & Product Testing
Services
- Software Design & Engineering Services
- System Integration
About The Customer
Messier-Bugatti-Dowty (Safran) is the world leader in aircraft landing and braking systems. The company is structured into five operating divisions and its products and technologies enable it to provide global expertise. About 25,000 Messier-Bugatti-Dowty-equipped aircraft make over 40,000 landings every day, all over the world. Its carbon brakes are 50% lighter than older generation steel counterparts. Airlines save on fuel through new composite materials, including titanium, used for machining equipment and landing gear, thus reducing their weight, environmental impact and operating costs. The company is located in 20 sites worldwide and has over 7,000 employees. Its headquarters is in Vélizy-Villacoublay, France.
The Challenge
Messier-Bugatti-Dowty, a global leader in aircraft landing and braking systems, faced the challenge of finding customized solutions for each client as rapidly as possible, often across continents. The company operates in a cross-cultural, multi-site environment with technicians and engineers working in different countries who do not necessarily speak the same language and who, in the past, were using different methods and tools. Each of their sites in Gloucester (UK), Montreal and Toronto (Canada), and Bidos (France) had their own industrialization processes and tools, making data exchange difficult and collaboration practically non-existent. The company launched a Manufacturing and Engineering Data System (MEDS) project to streamline development processes by rationalizing information systems at landing gear production sites.
The Solution
Messier-Bugatti-Dowty adopted Dassault Systèmes’ 3DEXPERIENCE platform for design, data management, simulation and analysis, manufacturing and documentation as provided through the industry solution “Ready for Rate.” The 3DEXPERIENCE platform provides engineering and manufacturing planning stakeholders with cross-site digital continuity and real-time access to accurate product and product build information. The platform is industry-oriented and flexible because it provides the ‘out-of-the-box’ industry specific tools needed to manage the entire production chain. The company uses many 3DEXPERIENCE platform applications including CATIA for design, ENOVIA V6 for multi-site collaboration and digital product management, SIMULIA for digital simulation and analysis, DELMIA V6 to manage assembly plans and machining sequences, and 3DVIA to exchange information throughout its ecosystem and to generate client documentation.
Operational Impact
Quantitative Benefit
Case Study missing?
Start adding your own!
Register with your work email and create a new case study profile for your business.
Related Case Studies.
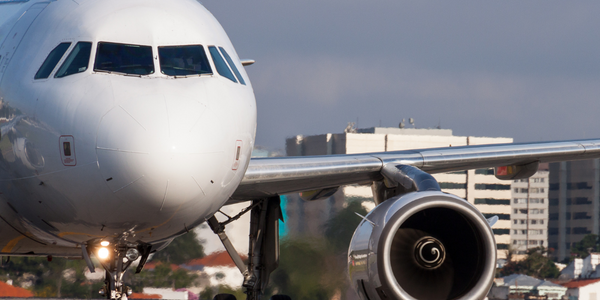
Case Study
Airbus Soars with Wearable Technology
Building an Airbus aircraft involves complex manufacturing processes consisting of thousands of moving parts. Speed and accuracy are critical to business and competitive advantage. Improvements in both would have high impact on Airbus’ bottom line. Airbus wanted to help operators reduce the complexity of assembling cabin seats and decrease the time required to complete this task.
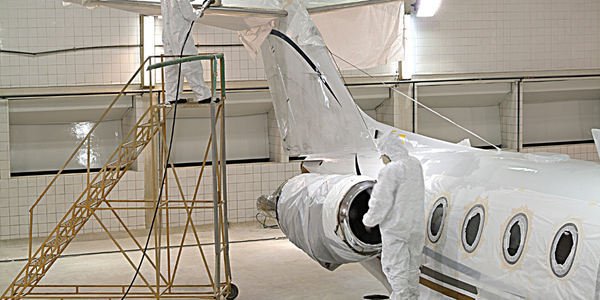
Case Study
Aircraft Predictive Maintenance and Workflow Optimization
First, aircraft manufacturer have trouble monitoring the health of aircraft systems with health prognostics and deliver predictive maintenance insights. Second, aircraft manufacturer wants a solution that can provide an in-context advisory and align job assignments to match technician experience and expertise.
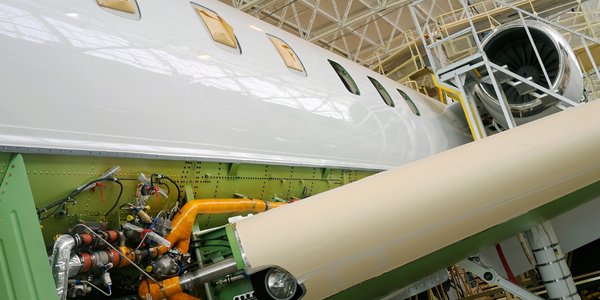
Case Study
Aerospace & Defense Case Study Airbus
For the development of its new wide-body aircraft, Airbus needed to ensure quality and consistency across all internal and external stakeholders. Airbus had many challenges including a very aggressive development schedule and the need to ramp up production quickly to satisfy their delivery commitments. The lack of communication extended design time and introduced errors that drove up costs.
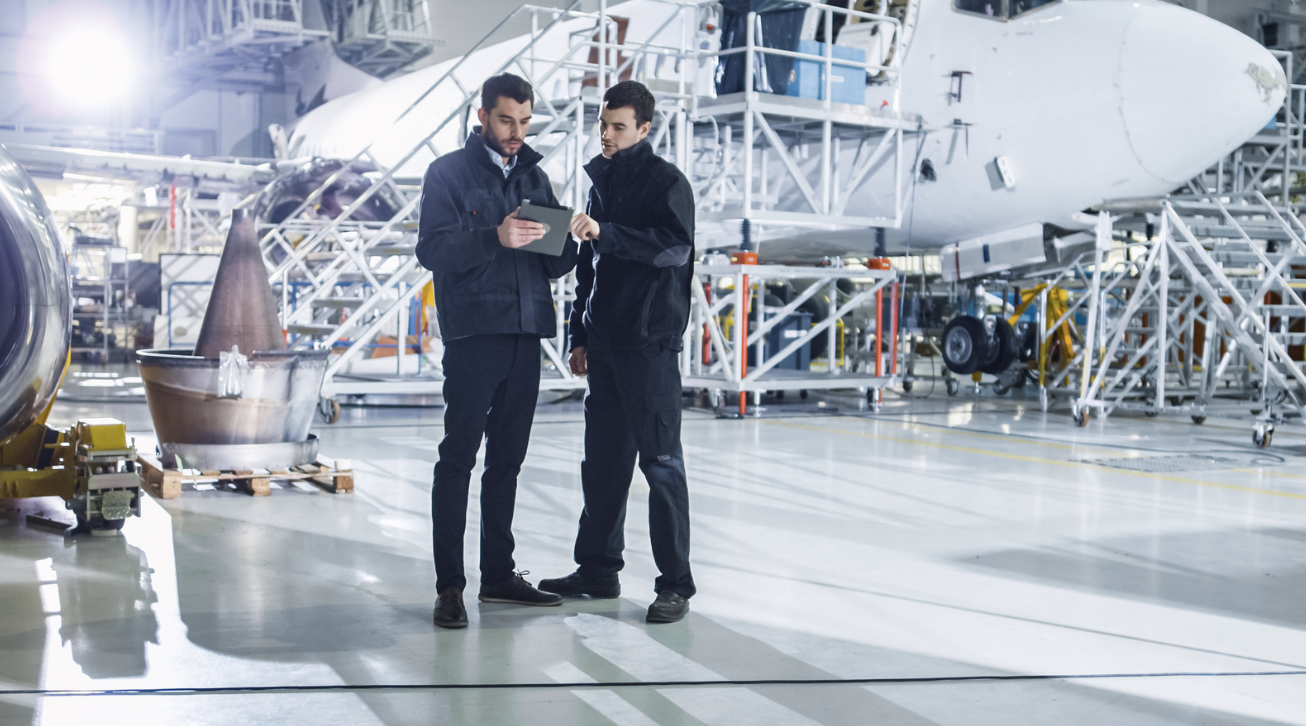
Case Study
Developing Smart Tools for the Airbus Factory
Manufacturing and assembly of aircraft, which involves tens of thousands of steps that must be followed by the operators, and a single mistake in the process could cost hundreds of thousands of dollars to fix, makes the room for error very small.
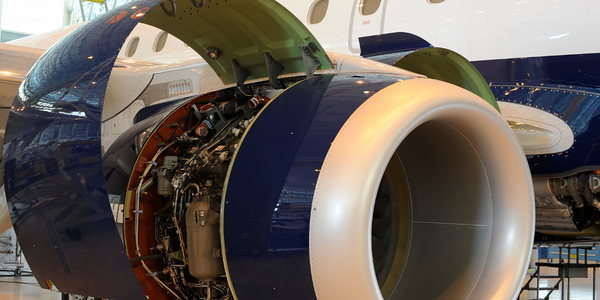
Case Study
Accelerate Production for Spirit AeroSystems
The manufacture and assembly of massive fuselage assemblies and other large structures generates a river of data. In fact, the bill of materials for a single fuselage alone can be millions of rows of data. In-house production processes and testing, as well as other manufacturers and customers created data flows that overwhelmed previous processes and information systems. Spirit’s customer base had grown substantially since their 2005 divestiture from Boeing, resulting in a $41 billion backlog of orders to fill. To address this backlog, meet increased customer demands and minimize additional capital investment, the company needed a way to improve throughput in the existing operational footprint. Spirit had a requirement from customers to increase fuselage production by 30%. To accomplish this goal, Spirit needed real-time information on its value chain and workflow. However, the two terabytes of data being pulled from their SAP ECC was unmanageable and overloaded their business warehouse. It had become time-consuming and difficult to pull aggregate data, disaggregate it for the needed information and then reassemble to create a report. During the 6-8 hours it took to build a report, another work shift (they run three per day) would have already taken place, thus the report content was out-of-date before it was ever delivered. As a result, supervisors often had to rely on manual efforts to provide charts, reports and analysis.