Altair HyperWorks and Product Design Consultation at Force Protection: Analysis Support for a New Class of Military Vehicles
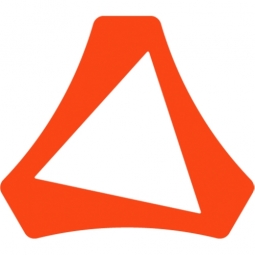
Technology Category
- Robots - Autonomous Guided Vehicles (AGV)
- Sensors - Haptic Sensors
Applicable Industries
- Automotive
- National Security & Defense
Applicable Functions
- Human Resources
- Product Research & Development
Use Cases
- Personnel Tracking & Monitoring
- Vehicle Performance Monitoring
Services
- Hardware Design & Engineering Services
About The Customer
Force Protection, Inc. (FPI) is a rapidly-growing company based in South Carolina that specializes in the creation of military vehicles. Their pioneering design, the Buffalo, is a large and intimidating vehicle built on a Mack truck chassis, designed for the purpose of clearing out land mines and Improvised Explosive Devices (IEDs). This design became the basis of a new U.S. military vehicle design standard known as MRAP (Mine Resistant, Ambush Protected). FPI continues to innovate and develop new products under the MRAP standard, including the Cougar, a smaller, more versatile version of the Buffalo.
The Challenge
Force Protection, Inc. (FPI), a South Carolina-based company, had developed a new class of military vehicle, the Buffalo, designed for clearing out land mines and Improvised Explosive Devices (IEDs). The Buffalo's pioneering design, with a monocoque hull designed to deflect blast away from personnel inside, became the basis of a new U.S. military vehicle design standard known as MRAP (Mine Resistant, Ambush Protected). However, as U.S. military involvement in the Middle East increased, the need for personnel transports that could withstand the kind of anti-insurgency war U.S. soldiers were fighting became apparent. The Army requested FPI to produce a smaller, more versatile version of the Buffalo, which was named the Cougar. This new vehicle had to meet a series of military, SAE, and NTSA standards, requiring documentable analyses to ensure compliance. FPI, however, lacked a formal in-house analysis capability.
The Solution
To meet the Army's requirements, FPI hired Harley Wattrick, a retired Ford employee with extensive FEA experience, to set up an analysis group. Wattrick and fellow analyst Lorraine Pizzirani, both experienced design engineers and CAE specialists, integrated analysis into the engineering process at FPI. They used Altair HyperWorks tools and assistance from Altair Product Design consulting services to develop a series of products under the MRAP standard. The HyperWorks tool allowed for clean import of FPI’s SolidWorks CAD geometry, eliminating the need for manual cleanup of CAD geometry after importing CAD files. This improved FPI's ability to respond quickly to requests for analysis. As FPI continued to grow and develop new vehicles, the workload on the two-person analysis shop increased. To manage this, FPI outsourced analysis expertise to Altair Product Design consulting operations.
Operational Impact
Quantitative Benefit
Case Study missing?
Start adding your own!
Register with your work email and create a new case study profile for your business.
Related Case Studies.
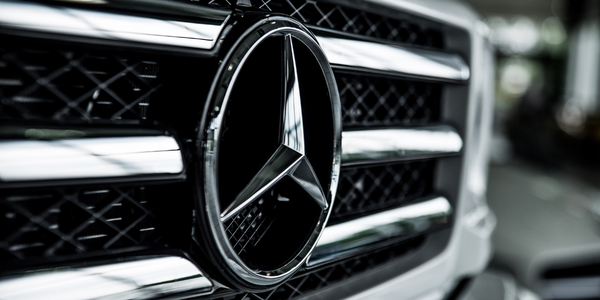
Case Study
Integral Plant Maintenance
Mercedes-Benz and his partner GAZ chose Siemens to be its maintenance partner at a new engine plant in Yaroslavl, Russia. The new plant offers a capacity to manufacture diesel engines for the Russian market, for locally produced Sprinter Classic. In addition to engines for the local market, the Yaroslavl plant will also produce spare parts. Mercedes-Benz Russia and his partner needed a service partner in order to ensure the operation of these lines in a maintenance partnership arrangement. The challenges included coordinating the entire maintenance management operation, in particular inspections, corrective and predictive maintenance activities, and the optimizing spare parts management. Siemens developed a customized maintenance solution that includes all electronic and mechanical maintenance activities (Integral Plant Maintenance).

Case Study
Monitoring of Pressure Pumps in Automotive Industry
A large German/American producer of auto parts uses high-pressure pumps to deburr machined parts as a part of its production and quality check process. They decided to monitor these pumps to make sure they work properly and that they can see any indications leading to a potential failure before it affects their process.