Amigo Mobility’s Order-to-Cash Automation via Celigo Delivers 10x ROI, Greater Efficiency, and Customer Satisfaction
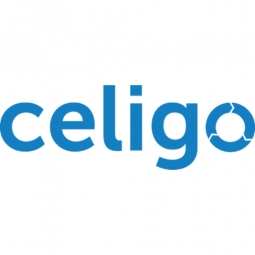
Technology Category
- Application Infrastructure & Middleware - Data Exchange & Integration
- Application Infrastructure & Middleware - Middleware, SDKs & Libraries
Applicable Industries
- Automotive
- Retail
Applicable Functions
- Maintenance
- Procurement
Use Cases
- Autonomous Transport Systems
- Transportation Simulation
Services
- System Integration
About The Customer
Amigo Mobility International, Inc. is a manufacturer and direct seller of motorized shopping carts, material handling equipment, and parts and accessories for mobility vehicles. Founded by Al Thieme in 1968, Amigo Mobility is an intricate company with over a 100 employees, supplying mobility solutions all over the world, in a variety of sectors, including healthcare, grocery, retail, material handling, and hospitals. The company is headquartered in Saginaw, Michigan, USA and uses products like integrator.io, Cash Application Manager for NetSuite, EDI, SAP Business Network, ServiceChannel, DocParser, and MailParser.
The Challenge
Amigo Mobility faced significant challenges with their order entry process from many of their largest customers. Customers like Kroger, Target and Walmart used SAP Ariba to issue purchase orders and accept invoices, but the lack of an intuitive and reliable way to sync Amigo’s internal system with SAP Ariba meant that Amigo had to enter and handle a large volume of orders manually. This led to data alignment issues and missed orders. Additionally, the company also needed to streamline service repair orders, custom pricing management, and cash application. After trying unsuccessfully for more than one year to build an integration between their EDI system and Ariba with internal resources, they needed to find a solution that would fit as many of their order process requirements as possible, while simultaneously saving on costs.
The Solution
Amigo Mobility adopted Celigo after learning about it at SuiteWorld. The Ariba-NetSuite integration offered by Celigo allowed them to automate their processes around Ariba, improving order accuracy by 100 percent and freeing up employees for other tasks. Encouraged by the success of the Ariba integration, they then turned to the Cash Application Manager (CAM) to improve the cash application process. They also integrated ServiceChannel and NetSuite with Celigo to handle their approximately 3,500 work orders per month, eliminating the need for two full-time employees to manually handle repair service orders. They also used Celigo to streamline document and email order flows with DocParser and MailParser integrations, and for pricing management, allowing them to update all sub-customers at once when changing the price on the parent customer.
Operational Impact
Quantitative Benefit
Case Study missing?
Start adding your own!
Register with your work email and create a new case study profile for your business.
Related Case Studies.
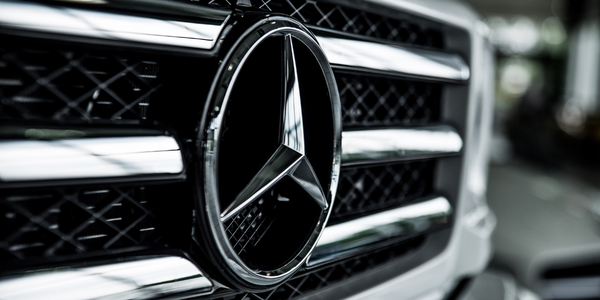
Case Study
Integral Plant Maintenance
Mercedes-Benz and his partner GAZ chose Siemens to be its maintenance partner at a new engine plant in Yaroslavl, Russia. The new plant offers a capacity to manufacture diesel engines for the Russian market, for locally produced Sprinter Classic. In addition to engines for the local market, the Yaroslavl plant will also produce spare parts. Mercedes-Benz Russia and his partner needed a service partner in order to ensure the operation of these lines in a maintenance partnership arrangement. The challenges included coordinating the entire maintenance management operation, in particular inspections, corrective and predictive maintenance activities, and the optimizing spare parts management. Siemens developed a customized maintenance solution that includes all electronic and mechanical maintenance activities (Integral Plant Maintenance).
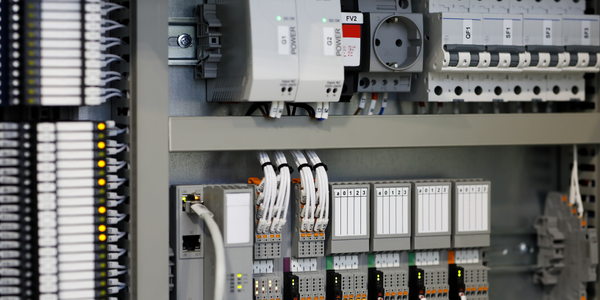
Case Study
Improving Production Line Efficiency with Ethernet Micro RTU Controller
Moxa was asked to provide a connectivity solution for one of the world's leading cosmetics companies. This multinational corporation, with retail presence in 130 countries, 23 global braches, and over 66,000 employees, sought to improve the efficiency of their production process by migrating from manual monitoring to an automatic productivity monitoring system. The production line was being monitored by ABB Real-TPI, a factory information system that offers data collection and analysis to improve plant efficiency. Due to software limitations, the customer needed an OPC server and a corresponding I/O solution to collect data from additional sensor devices for the Real-TPI system. The goal is to enable the factory information system to more thoroughly collect data from every corner of the production line. This will improve its ability to measure Overall Equipment Effectiveness (OEE) and translate into increased production efficiencies. System Requirements • Instant status updates while still consuming minimal bandwidth to relieve strain on limited factory networks • Interoperable with ABB Real-TPI • Small form factor appropriate for deployment where space is scarce • Remote software management and configuration to simplify operations