Customer Company Size
Large Corporate
Region
- Asia
- Europe
Country
- Italy
Product
- IBM ILOG CPLEX CP Optimizer
- MBM Italia S.r.l — GPS 64b (Global Planning System)
Tech Stack
- Mathematical Optimization
- Simulation
Implementation Scale
- Enterprise-wide Deployment
Impact Metrics
- Productivity Improvements
- Cost Savings
Technology Category
- Analytics & Modeling - Predictive Analytics
- Analytics & Modeling - Process Analytics
Applicable Industries
- Metals
Applicable Functions
- Discrete Manufacturing
Use Cases
- Advanced Production Planning and Scheduling
- Flexible Manufacturing
Services
- System Integration
About The Customer
Danieli & C. Officine Meccaniche S.p.A. is a large company based in Europe that designs, constructs, and sells plants and equipment for the metallurgical industry, such as steel and iron. The company has factories in five countries across Europe and Asia. The company's operations involve the complex process of building steel mills and the related equipment, which requires the orchestration of thousands of components, workers, and machines.
The Challenge
Building steel mills and the related equipment is a highly complex process that requires orchestrating thousands of components, workers and machines. Lacking modern planning software, Italy-based Danieli & C. Officine Meccaniche S.p.A., a steel plant builder with factories in five countries in Europe and Asia, struggled to coordinate materials and resources, compromising efficiency and jeopardizing timelines.
The Solution
Danieli chose a mathematical optimization solution that takes into account all production constraints of every single plant, enabling the builder to develop optimal production schedules that align with order requirements, delivery dates and manufacturing goals. If changes in production plans occur, what-if scenarios show their effect on workloads while the solution runs multiple simulations and results are delivered in a few seconds, helping Danieli schedule its flexible manufacturing system (FMS) machine operations.
Operational Impact
Quantitative Benefit
Case Study missing?
Start adding your own!
Register with your work email and create a new case study profile for your business.
Related Case Studies.
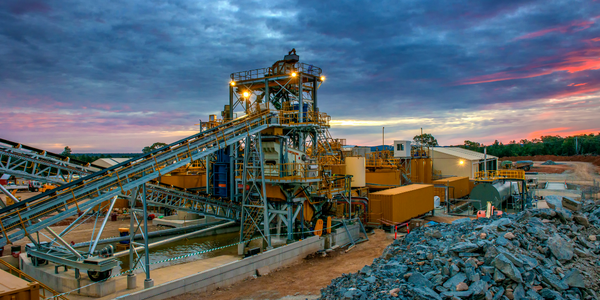
Case Study
Goldcorp: Internet of Things Enables the Mine of the Future
Goldcorp is committed to responsible mining practices and maintaining maximum safety for its workers. At the same time, the firm is constantly exploring ways to improve the efficiency of its operations, extend the life of its assets, and control costs. Goldcorp needed technology that can maximize production efficiency by tracking all mining operations, keep employees safe with remote operations and monitoring of hazardous work areas and control production costs through better asset and site management.

Case Study
KSP Steel Decentralized Control Room
While on-site in Pavlodar, Kazakhstan, the DAQRI team of Business Development and Solutions Architecture personnel worked closely with KSP Steel’s production leadership to understand the steel production process, operational challenges, and worker pain points.
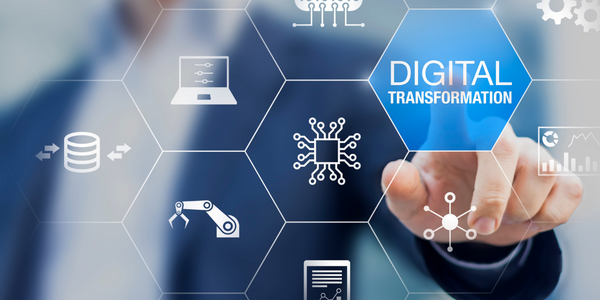
Case Study
Bluescope Steel on Path to Digitally Transform Operations and IT
Increasing competition and fluctuations in the construction market prompted BlueScope Steel to look toward digital transformation of its four businesses, including modern core applications and IT infrastructure. BlueScope needed to modernize its infrastructure and adopt new technologies to improve operations and supply chain efficiency while maintaining and updating an aging application portfolio.
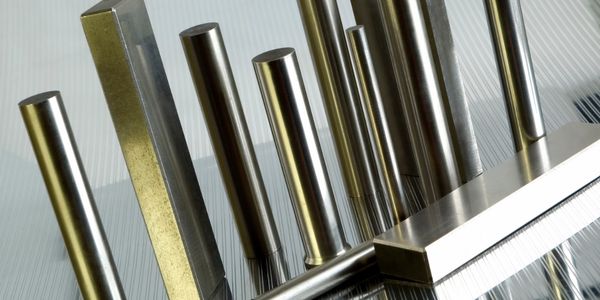
Case Study
RobotStudio Case Study: Benteler Automobiltechnik
Benteler has a small pipe business area for which they produce fuel lines and coolant lines made of aluminum for Porsche and other car manufacturers. One of the problems in production was that when Benteler added new products, production had too much downtime.
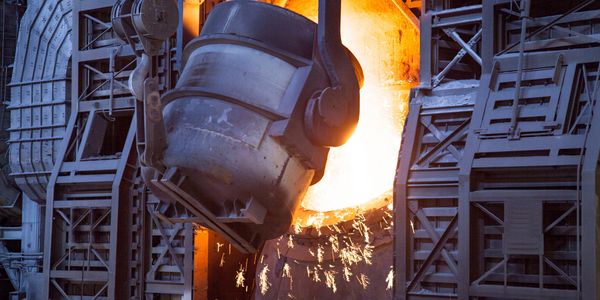
Case Study
Continuous Casting Machines in a Steel Factory
With a very broad range of applications, steel is an important material and has been developed into the most extensive alloy in the engineering world. Since delivering high quality is absolutely crucial for steel plants, ensuring maximum productivity and the best quality production are the keys to competitiveness in the steel industry. Additionally, working conditions in steel factories are not suitable for workers to stay in for long periods of time, so manufactures usually adopt various machines to complete the steel production processes. However, the precision of these machines is often overestimated and the lack of flexibility also makes supervisors unable to adjust operating procedures. A renowned steel factory in Asia planned to improve its Distributed Control System (DCS) of furnaces as well as addressing the problem of insufficient accuracy. However, most well-known international equipment suppliers can not provide a satisfactory solution and local maintenance because the project needed new technologies to more accurately control equipment operations. By implementing Advantech’s automated monitoring and control solution, steel factories can not only improve the manufacturing processes but can also allow users to add additional functions to the existing system so as to make sure the operation runs at high efficiency.
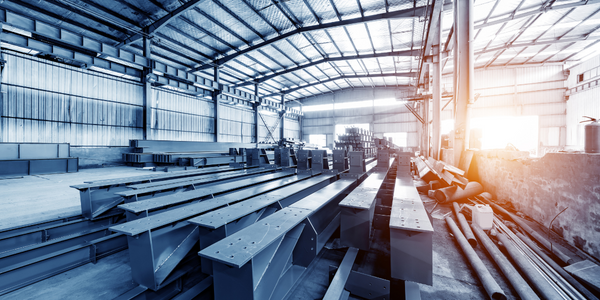
Case Study
Automated Predicitive Analytics For Steel/Metals Industry
Asset to be monitored: Wire Compactor that produces Steel RebarCustomer Faced The Following Challenges:Dependent upon machine uptime.Pressure cylinders within the compactor fail to control compression and speed causing problems in binding the coil.Equipment failure occurs in the final stage of production causing the entire line to stop, can you say bottleneck?Critical asset unequipped with sensors to produce data.