Customer Company Size
Mid-size Company
Region
- Europe
Country
- Spain
Product
- QlikView
Tech Stack
- Microsoft SQL Server 2000
- Microsoft SQL Server 2005
- Microsoft Access
- Oracle
- Excel
Implementation Scale
- Departmental Deployment
Impact Metrics
- Productivity Improvements
- Digital Expertise
Technology Category
- Analytics & Modeling - Real Time Analytics
Applicable Functions
- Human Resources
Use Cases
- Process Control & Optimization
- Real-Time Location System (RTLS)
Services
- Data Science Services
- System Integration
About The Customer
The Public Ports Authority of Andalusia (APPA) is responsible for the development and application of port policy and for the transportation of goods using delegated powers from the Andalusian Government. The APPA with its head office in Seville has 250 employees. They manage the port installations and the transportation of goods areas, responding to demands made by users, in addition to improving the technical and economic return on investments made. In 2009 the authority invoiced its customers for a total of €23 million.
The Challenge
The Public Ports Authority of Andalusia (APPA) needed a business intelligence (BI) tool that would allow it to process and analyse all the management data generated over the past 10 years of its operations. The authority wanted to install the BI tool in several departments including finance, human resources, planning, systems and telecommunications, operating and contracting and statistics. The company needed a BI solution that could be installed and brought into production in record time. The period that elapsed between installing QlikView in the company’s server and production of the first documents was just 30 days.
The Solution
The APPA installed QlikView, a business intelligence tool, in several departments including finance, human resources, planning, systems and telecommunications, operating and contracting and statistics. The BI software was installed using “zero footprint” and added different data management software such as Microsoft SQL Server 2000, Microsoft SQL Server 2005, Microsoft Access, Oracle, and Excel. Thanks to QlikView it was possible to integrate a total of 20 GB of data and 50 million for registers. These sources of integrated data are currently being accessed by 15 users in the company, including directors, heads of department, and technicians.
Operational Impact
Quantitative Benefit
Case Study missing?
Start adding your own!
Register with your work email and create a new case study profile for your business.
Related Case Studies.
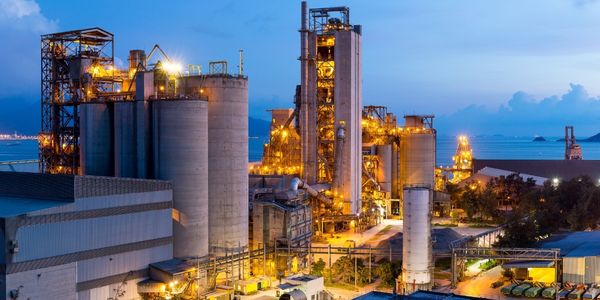
Case Study
System 800xA at Indian Cement Plants
Chettinad Cement recognized that further efficiencies could be achieved in its cement manufacturing process. It looked to investing in comprehensive operational and control technologies to manage and derive productivity and energy efficiency gains from the assets on Line 2, their second plant in India.
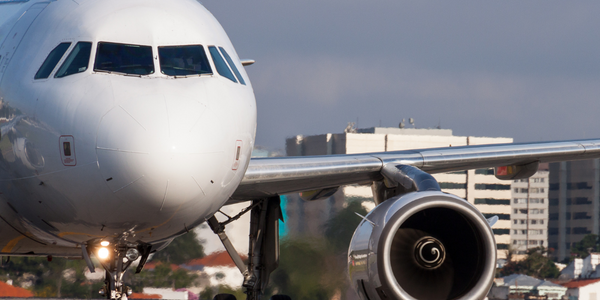
Case Study
Airbus Soars with Wearable Technology
Building an Airbus aircraft involves complex manufacturing processes consisting of thousands of moving parts. Speed and accuracy are critical to business and competitive advantage. Improvements in both would have high impact on Airbus’ bottom line. Airbus wanted to help operators reduce the complexity of assembling cabin seats and decrease the time required to complete this task.
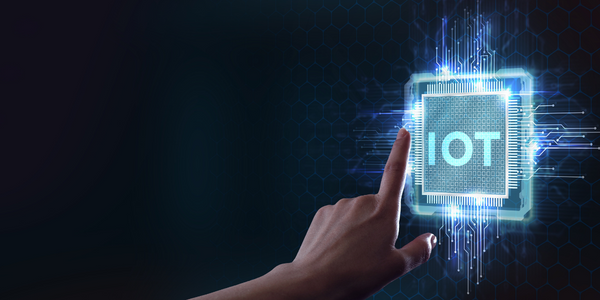
Case Study
Leading Tools Manufacturer Transforms Operations with IoT
Stanley Black & Decker required transparency of real-time overall equipment effectiveness and line productivity to reduce production line change over time.The goal was to to improve production to schedule, reduce actual labor costs and understanding the effects of shift changes and resource shifts from line to line.
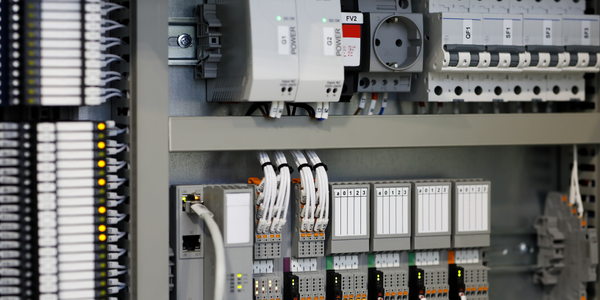
Case Study
Improving Production Line Efficiency with Ethernet Micro RTU Controller
Moxa was asked to provide a connectivity solution for one of the world's leading cosmetics companies. This multinational corporation, with retail presence in 130 countries, 23 global braches, and over 66,000 employees, sought to improve the efficiency of their production process by migrating from manual monitoring to an automatic productivity monitoring system. The production line was being monitored by ABB Real-TPI, a factory information system that offers data collection and analysis to improve plant efficiency. Due to software limitations, the customer needed an OPC server and a corresponding I/O solution to collect data from additional sensor devices for the Real-TPI system. The goal is to enable the factory information system to more thoroughly collect data from every corner of the production line. This will improve its ability to measure Overall Equipment Effectiveness (OEE) and translate into increased production efficiencies. System Requirements • Instant status updates while still consuming minimal bandwidth to relieve strain on limited factory networks • Interoperable with ABB Real-TPI • Small form factor appropriate for deployment where space is scarce • Remote software management and configuration to simplify operations