Technology Category
- Analytics & Modeling - Machine Learning
- Networks & Connectivity - RFID
Applicable Industries
- Consumer Goods
- Packaging
Applicable Functions
- Human Resources
- Product Research & Development
Use Cases
- Construction Management
- Inventory Management
Services
- Cloud Planning, Design & Implementation Services
- Data Science Services
About The Customer
Anheuser-Busch InBev, headquartered in Leuven, Belgium, is a global beverage company operating in more than 50 countries on six continents. The company is known for its popular beer brands such as Budweiser, Corona, Stella Artois, Beck’s, and Foster’s. AB InBev is not just a beverage company, but also a technology company, using technology to drive commercial and operational growth and increase sustainability. The company has a Beer Garage in Silicon Valley and a Global Analytics Center in Bengaluru, India, where it pushes the innovation envelope. AB InBev is also involved in many better-world initiatives, focusing on sustainability and giving back to the communities.
The Challenge
Anheuser-Busch InBev (AB InBev), a global beverage company, was facing challenges in managing its technology platforms across more than 50 countries. The company had divided its business into six different zones, each managing its own IT processes, and had 16 corporate datacenters. This resulted in siloed information and operations, duplication of research efforts, and difficulty in embracing innovation company-wide. The company wanted to centralize its IT functions and move away from managing core infrastructure to focus on innovative services. Additionally, AB InBev was looking to develop a global analytics platform to gain valuable insights into the vast amounts of data harvested from each step in its manufacturing process.
The Solution
AB InBev chose Microsoft Azure as the platform to support its IT transformation. The company began by moving its IT operations to the cloud, breaking down data silos, and building a global analytics platform. It used application modernization and containerization strategies with technologies like Docker and Kubernetes to move applications into Azure. The company also shifted its legacy data warehouses to an Azure platform as a service (PaaS) environment using Azure Synapse Analytics. AB InBev developed a global analytics platform using Synapse Analytics, bringing together data from multiple departments. The company also made extensive use of Hadoop for big data analytics processes, Azure HDInsight service, Azure Data Lake, and Azure Blob storage. AB InBev also started pilot testing an RFID program in its warehouses using Azure Internet of Things (IoT) services including Azure IoT Hub and Azure Stream Analytics.
Operational Impact
Quantitative Benefit
Case Study missing?
Start adding your own!
Register with your work email and create a new case study profile for your business.
Related Case Studies.
.png)
Case Study
Improving Vending Machine Profitability with the Internet of Things (IoT)
The vending industry is undergoing a sea change, taking advantage of new technologies to go beyond just delivering snacks to creating a new retail location. Intelligent vending machines can be found in many public locations as well as company facilities, selling different types of goods and services, including even computer accessories, gold bars, tickets, and office supplies. With increasing sophistication, they may also provide time- and location-based data pertaining to sales, inventory, and customer preferences. But at the end of the day, vending machine operators know greater profitability is driven by higher sales and lower operating costs.

Case Study
IoT Data Analytics Case Study - Packaging Films Manufacturer
The company manufactures packaging films on made to order or configure to order basis. Every order has a different set of requirements from the product characteristics perspective and hence requires machine’s settings to be adjusted accordingly. If the film quality does not meet the required standards, the degraded quality impacts customer delivery causes customer dissatisfaction and results in lower margins. The biggest challenge was to identify the real root cause and devise a remedy for that.
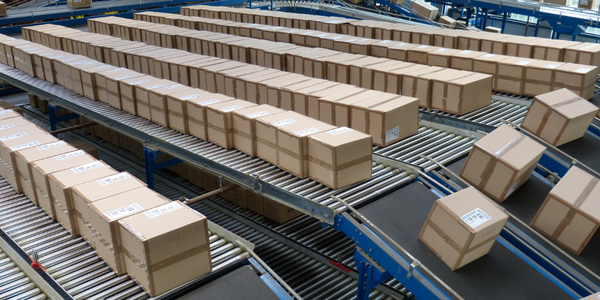
Case Study
Zenon the Ideal Basis for An Ergonomic HMI
KHS develops and produces machines and equipment for filling and packaging in the drinks industry. Because drinks manufacturing, filling and packaging consist of a number of highly complex processes, the user-friendly and intuitive operation of equipment is increasingly gaining in significance. In order to design these processes as simple as possible for the user, KHS decided to introduce a uniform, transparent and standardized solution to the company. The HMI interface should meet the requirement for people with different qualifications and enable them to work on a standard platform.
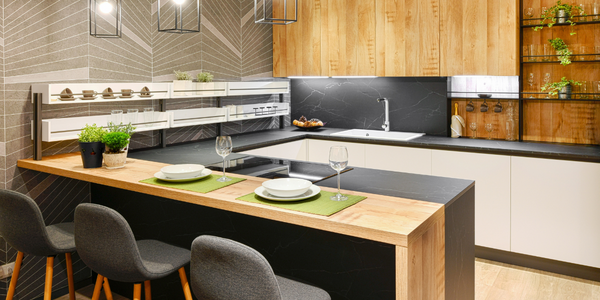
Case Study
Series Production with Lot-size-1 Flexibility
Nobilia manufactures customized fitted kitchens with a lot size of 1. They require maximum transparency of tracking design data and individual processing steps so that they can locate a particular piece of kitchen furniture in the sequence of processes.