Technology Category
- Automation & Control - Automation & Process Control Systems
- Sensors - Utility Meters
Applicable Functions
- Quality Assurance
Use Cases
- Intelligent Urban Water Supply Management
- Leakage & Flood Monitoring
Services
- System Integration
- Testing & Certification
About The Customer
Aquapolo is Brazil's largest wastewater treatment plant. It plays a crucial role in providing potable water to the local community and meeting the water needs of the industrial sector. The plant is responsible for managing a wide range of KPIs related to water quality and quantity. Aquapolo is committed to reducing production costs and improving operational efficiency. The plant is also dedicated to ensuring sustainable water management and better regulatory compliance to protect the environment.
The Challenge
Aquapolo, Brazil's largest wastewater treatment plant, was faced with a significant challenge. The local community was experiencing a severe shortage of potable water, and there was an increasing demand for water for industrial use. Aquapolo was tasked with managing 20 different Key Performance Indicators (KPIs) related to water quality and quantity. The plant also needed to reduce production costs and improve operational efficiency. The challenge was not only to meet the immediate water needs of the community and industry but also to ensure sustainable and efficient water management for the future.
The Solution
Aquapolo turned to EcoStruxure, a suite of IoT-enabled solutions, to address these challenges. The solution included Apps, Analytics and Services such as EcoStruxure Augmented Operator Advisor, AVEVA Manufacturing Execution System, AVEVA Historian, and expert services. Edge Control was provided by Modicon M238 and M340 PLCs, and AVEVA Plant SCADA. Connected Products included Harmony HMI, Foxboro instrumentation, and ConneXium switches. AVEVA Plant SCADA and AVEVA Historian controlled and captured information on 20 qualitative and quantitative parameters. Foxboro sensors ensured the accuracy of the readings around effluent entry into the reverse osmosis/ultra-filtration plant and sent the information to the Modicon PLCs, which controlled the industrial water treatment, pumping stations, and reservoir operations. Operators monitored the process locally via the Harmony HMI, and the AVEVA Manufacturing Execution System supported invoice calculation.
Operational Impact
Quantitative Benefit
Case Study missing?
Start adding your own!
Register with your work email and create a new case study profile for your business.
Related Case Studies.
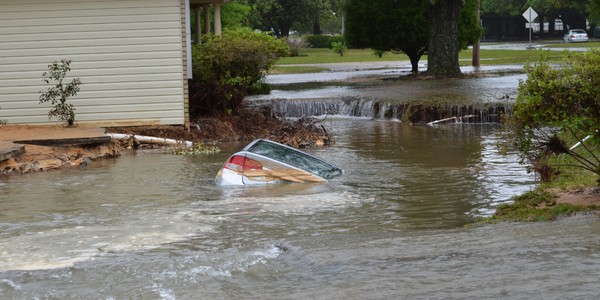
Case Study
Greater Peace of Mind with Pentair
When severe weather hits, the potential damage to a home could be disastrous. Insurance claims for flooding damage exceed $3 billion per year in the United States, and most homeowners are not even covered for even basic water damage to carpet, drywall, electrical, furniture and personal items. Sump pumps are one of the best defenses against flood damage, but when storms knock out electricity, traditional sump pumps are rendered useless. As a seller of water management and equipment protection, Pentair sought a communication platform that will support a wide range of Pentair Internet-connected products.
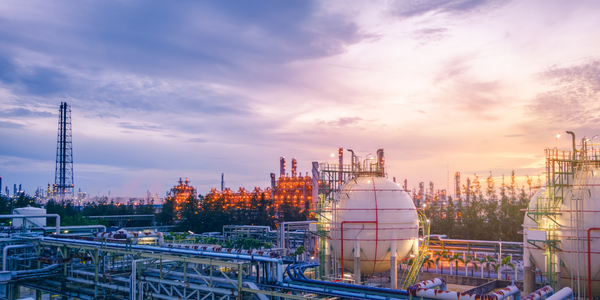
Case Study
Cisco Kinetic for Oil and Gas: Refineries and Plants
The plant manager and safety teams needed a solution that provided near real-time visibility of gas detection and personnel location, with easy to understand visualization and alerting dashboards. This would enable them to improve productivity through decreasing the time taken to start work, optimize evacuation route planning, and to meet critical staff safety and compliance goals.
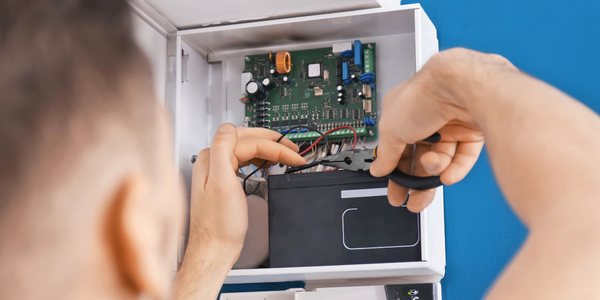
Case Study
MICROMEDIA’S ALERT ASSISTS AIR LIQUIDE’S SCADA SYSTEM FABVIEW
WIN-911’s partner product ALERT is a key element in the Supervisory Control and Data Acquisition (SCADA) system “FabView” from Air Liquide. Air Liquide is the second largest supplier of industrial gasses in the world. This SCADA alarm notification system is specifically designed to monitor, among other things, the distribution of gas in a semiconductor manufacturing plant located in Dresden Germany. Like most operations of its type, this facility can’t afford much downtime in its distribution facility. If ALERT detects a leak in a pipeline, the system evaluates how severe the leak is and transfers the data back to the central site or home office. Once the information is back in the main office, the SCADA alert system then transcribes the data into understandable messages to which employees can respond appropriately.
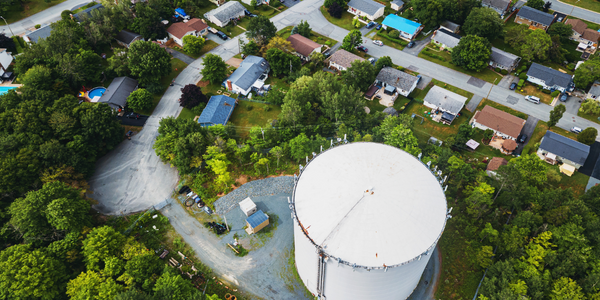
Case Study
IIC - Intelligent Urban Water Supply Testbed
Water, after air, is the second most critical natural resource our lives depend upon. Maintaining adequate clean and safe water supply to urban residents has become ever-challenging. This is especially so under the pressure from the rapid urbanization of the populations in developing countries and increasingly severe constraints of available water resources in many parts of the world. The situation is exacerbated by the inadequate and aging equipment deployed in the water supply infrastructure and the ineffectiveness in the management of the operations of the equipment. The consequence of these conditions impacts to the health and quality of lives of millions of urban residents. The prevailing conditions in the urban water supply systems include: • Safety: Inability to timely detect water quality issues that may lead to health problems • Service Availability: Inability to detect, address and prevent, on a timely basis, operational issues that cause unnecessary service outages • Efficiency: Inability to assess and identify water leakages, and to identify and address energy over-consumption in heavy operational assets (e.g. water-pressurizing bumps), both leading to wastefulness of valuable resources and in the latter case negatively impacting the environment • Effectiveness: Inability to optimize the operation of a group of water-pressuring pumps to provide equitable water supply and to avoid equipment damages under these conditions.