Customer Company Size
Large Corporate
Region
- Europe
Country
- Netherlands
Product
- Artificial Turf
- Abaqus FEA
Tech Stack
- Finite Element Analysis
- Simulation Modeling
Implementation Scale
- Enterprise-wide Deployment
Impact Metrics
- Productivity Improvements
- Innovation Output
Technology Category
- Analytics & Modeling - Digital Twin / Simulation
Applicable Functions
- Product Research & Development
Use Cases
- Digital Twin
- Virtual Prototyping & Product Testing
Services
- Software Design & Engineering Services
About The Customer
Royal TenCate is the world’s leading producer of synthetic grass fibers and other components for playing fields. The company caters to various sports including soccer, American football, rugby, field hockey, or lacrosse. A playing field must be able to take a significant amount of pounding from feet, sports balls, and falling bodies. Add different climates (hot versus cold, wet versus dry) and impact patterns (heavily padded American football teams versus bare-kneed soccer players) and you begin to get an idea of the design variables that TenCate must take into account when designing artificial turf. The company makes distinct types of polyethylene grass fibers, plus thermoplastic infill material, and polypropylene woven backing fabrics—all of which must work together for optimum results.
The Challenge
The Fédération Internationale de Football Association (FIFA) has set detailed regulations about the materials, substructure, installation, testing, and certification of artificial turf for playing fields. This means that turf manufacturers have to consider a multitude of factors when designing their products for performance and safety. These factors include the make-up of the individual blades to mimic the look and playing-feel of natural grass, the type of yarn/fiber to use, the shape of the fiber, its height above the field surface, its density per square meter, stiffness and dissipative behavior. All these factors affect wear, safety, and playing characteristics. Furthermore, what’s below the visible surface of the grass is just as critical. The fiber travels down through infill made of rubber or thermoplastic granulate, which provides shock absorption, controls rebound and prevents skin damage caused by sliding. Beneath that are additional layers of rubber and sand and, finally, the backing in which the grass blade is imbedded.
The Solution
To meet the stringent requirements set by FIFA, TenCate turned to Abaqus finite element analysis (FEA) to model their turf design. The software was chosen due to the breadth of its materials models and its ability to model the individual characteristics of each component and relate that to the behavior of the total system. When creating artificial turf models, TenCate looks at the problem at a number of levels: micro, the properties of an individual fiber; meso, grains of infill interacting with fibers; and macro, a ball or player impacting the field. A grass-fiber model in Abaqus can be subjected to virtual bending tests, and its mass, shape, height, etc. modified and retested, until the desired characteristics are achieved. Infill models can be adjusted for morphology, size, material, distribution, friction and layer thickness, and then run through triaxial (three-dimensional) compression tests. An entire square of turf, with fibers, infill and backing characteristics built into the model, can be evaluated for compression by a virtual foot or a bouncing ball.
Operational Impact
Case Study missing?
Start adding your own!
Register with your work email and create a new case study profile for your business.
Related Case Studies.
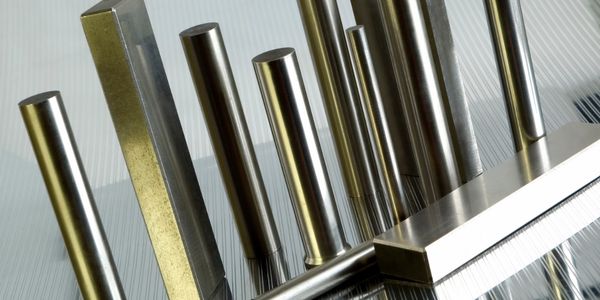
Case Study
RobotStudio Case Study: Benteler Automobiltechnik
Benteler has a small pipe business area for which they produce fuel lines and coolant lines made of aluminum for Porsche and other car manufacturers. One of the problems in production was that when Benteler added new products, production had too much downtime.
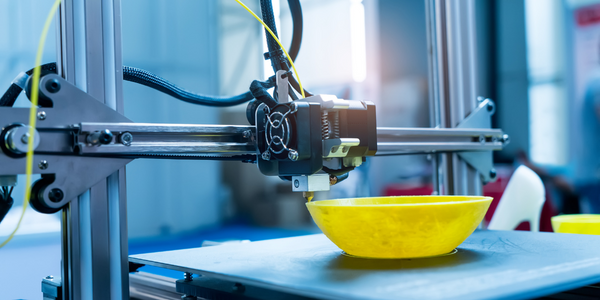
Case Study
Intralox Using Demo3D Case Study
Intralox strives to create significant economic value for our customers by optimizing their conveyance systems. Intralox wants to emulate real-world production environments for end users and OEMs working in multiple industries, including packaging, warehousing, parcel, beverage, brewery, food, tire, and consumer goods. They frequently had to perform physical tests to demonstrate to customers how ARB equipment would handle their products.