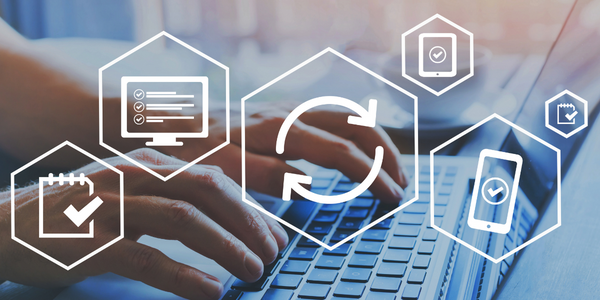
- Analytics & Modeling - Big Data Analytics
- Plastics
- Process Manufacturing
- Process Control & Optimization
Ascend operations must access multiple software systems to manage day-to-day operations in an effective and secure manner. These systems generate large sets of data which contain critical information pertaining to management systems, planning and cost information in business systems and energy consumption. As a result, Ascend management was challenged with creating relevant reports reflecting performance measures in overall context of their operational process. The company’s previous process entailed collecting and analyzing data manually which was not effective, since the information collected was generated after the fact, and was too complex for collaborative use across the organization.
Wonderware Intelligence software addresses the challenges faced by Ascend to leverage the hidden insights in industrial data. The software automates the transformation of time series and transactional data across multiple sources and turns large amounts of Industrial “Big Data” into actionable metrics and Key Performance Indicator (KPI) information. Metrics and context data is kept in an open information model, providing a single version of the current data. This is stored in data warehouses and enterprise business intelligence tools enabling Ascend management to make strategic sense out of the production data. With Wonderware Workflow, companies can institutionalize work processes that manage normal, unscheduled or disruptive events within their operations environment. This industrial workflow application benefits operations, maintenance, engineering, quality, environmental & safety departments within an organization.
Case Study missing?
Start adding your own!
Register with your work email and create a new case study profile for your business.
Related Case Studies.
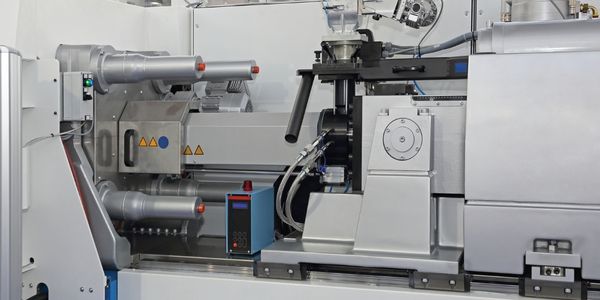
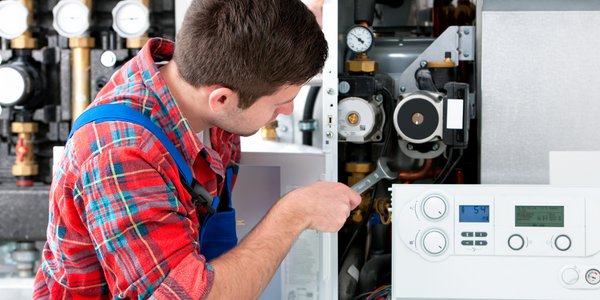
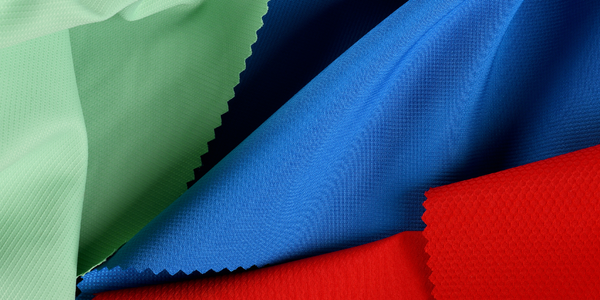
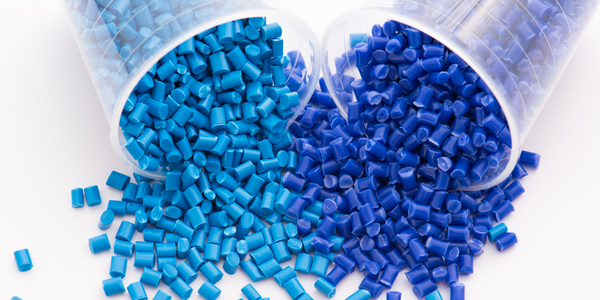