Customer Company Size
Large Corporate
Region
- Europe
Country
- United Kingdom
Product
- HPE SimpliVity
- HPE Synergy
- HPE Apollo 6500 Gen10 System
- HPE Nimble Storage
- HPE Moonshot
Tech Stack
- HPE OneView
- HPE InfoSight
- Citrix Virtual Apps and Desktops
Implementation Scale
- Enterprise-wide Deployment
Impact Metrics
- Productivity Improvements
- Innovation Output
Technology Category
- Infrastructure as a Service (IaaS) - Cloud Computing
- Infrastructure as a Service (IaaS) - Cloud Storage Services
- Application Infrastructure & Middleware - Data Exchange & Integration
- Platform as a Service (PaaS) - Data Management Platforms
Applicable Industries
- Automotive
Applicable Functions
- Discrete Manufacturing
- Product Research & Development
Use Cases
- Predictive Maintenance
- Manufacturing System Automation
- Real-Time Location System (RTLS)
Services
- Cloud Planning, Design & Implementation Services
- Data Science Services
- System Integration
About The Customer
Aston Martin Red Bull Racing is a Formula 1 racing team that competes in over 20 races each year. The team consists of over 850 members who work tirelessly to make changes that can shave vital milliseconds off their car's performance, which could be the difference between winning or losing the next race. Each Formula 1 circuit is different, with its own challenges and characteristics, and the car is customized for each race location. Between races, the team has just days to make changes, simulate, manufacture, and test new designs. A typical F1 car can go through some 30,000 changes throughout the season and from week-to-week, this can involve 1,000 design elements. The team needs a robust technology infrastructure in place to make them agile, efficient, and business-like, both on and off the track.
The Challenge
Aston Martin Red Bull Racing, a Formula 1 team, is in a constant race against time, not just on the track but also off it. Each Formula 1 circuit is different, with its own challenges and characteristics and the car is customized for each race location. Between races, the clock is ticking to create new designs and adapt the car for the next circuit. An F1 car can go through some 30,000 changes throughout the season and from week-to-week, this can involve 1,000 design elements. The result is a constant evolution of change in the design process, all of which needs to be simulated, manufactured, and tested. With a typical year consisting of more than 20 races, Aston Martin Red Bull Racing needs a robust technology infrastructure in place to make the team agile, efficient, and business-like, both on and off the track.
The Solution
Aston Martin Red Bull Racing has a strict development cycle for every component and HPE technology plays an important role in each step. HPE Synergy hosts the team's mixed workloads, including Computer Aided Design (CAD) and Product Lifecycle Management (PLM) software applications, Oracle databases, and SQL Server based applications. The solution replaced the team's legacy blade enclosures and rackmount server estate at its factory headquarters. This system used in conjunction with HPE OneView provides an agile, scalable approach to infrastructure deployment allowing resources to be quickly and easily re-allocated where required, enabling the team to meet changing needs. This highly capable infrastructure supports mission-critical car development processes. At the factory, 80% of the team's business-critical applications run on HPE SimpliVity. This not only includes systems used to design, manufacture and race the car, but also communication tools such as email and unified communications. HPE InfoSight uses advanced analytics to predict problems before they occur and this ensures that the HPE SimpliVity estate operates at peak performance levels and with very high availability.
Operational Impact
Quantitative Benefit
Case Study missing?
Start adding your own!
Register with your work email and create a new case study profile for your business.
Related Case Studies.
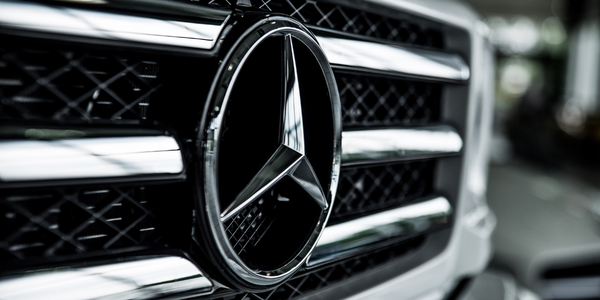
Case Study
Integral Plant Maintenance
Mercedes-Benz and his partner GAZ chose Siemens to be its maintenance partner at a new engine plant in Yaroslavl, Russia. The new plant offers a capacity to manufacture diesel engines for the Russian market, for locally produced Sprinter Classic. In addition to engines for the local market, the Yaroslavl plant will also produce spare parts. Mercedes-Benz Russia and his partner needed a service partner in order to ensure the operation of these lines in a maintenance partnership arrangement. The challenges included coordinating the entire maintenance management operation, in particular inspections, corrective and predictive maintenance activities, and the optimizing spare parts management. Siemens developed a customized maintenance solution that includes all electronic and mechanical maintenance activities (Integral Plant Maintenance).

Case Study
Monitoring of Pressure Pumps in Automotive Industry
A large German/American producer of auto parts uses high-pressure pumps to deburr machined parts as a part of its production and quality check process. They decided to monitor these pumps to make sure they work properly and that they can see any indications leading to a potential failure before it affects their process.