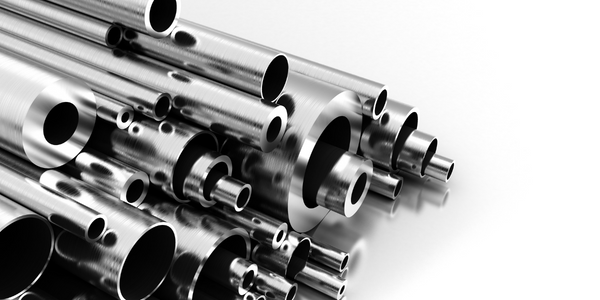
Technology Category
- Networks & Connectivity - RFID
- Wearables - Tags & Patches
Applicable Industries
- Metals
Applicable Functions
- Logistics & Transportation
Use Cases
- Track & Trace of Assets
The Customer
ThyssenKrupp Steel
About The Customer
ThyssenKrupp Steel Europe is one of the world’s leading suppliers of high-grade flat steel. With around 27,000 employees the group supplies high-quality steel products for innovative and demanding applications in a wide range of industries. Customer-speci
The Challenge
Steel slabs usually weigh between 20 to 40 tons each. After production, the surface is scaly and rusty. Outdoor storage and sea shipment expose the slabs to rough conditions. Loading ocean vessels is time consuming and total cost can easily exceed a few hundred thousand USD.
RFID technology offers many benefits. RFID transponders are small, store the identity of the labelled product and enable reading
out this data via antennas from a distance of several metres. However, there are special requirements for the use of RFID in the
steel sector. Firstly, the radio waves of the RFID readers are reflected by metal which creates major problems for reading out.
And secondly, they must be attached securely as the heavy slabs weigh tons and can rub against each other during the transport
on ships and trains, causing the labels to become detached or to be destroyed.
The Solution
“We had cooperated with other identification companies and system developers in the past. We knew that an RFID tag
that has been bent away from a steel slab can still be read. However, the problem was that the solutions suggested by
other companies did not have sufficient adhesion or applying the labels would have required costly special processes
and systems in our Brazilian plant,” Loïc Feinbier recalls.
The breakthrough was achieved by the cooperation with the experts from S+P Samson GmbH who brought their many
years of experience with identification for steel logistics to the project.
S+P Samson developed an adhesive label made from a film which had the transponder part bent away from the slab like
a flag, via a simple perforation, so that it can be read. Another benefit: S+P labels and tags could be printed using a standard Lexmark laser printer which has an additional RFID unit fitted that writes the chips. As printing and RFID programming is done at the same time, the number of work steps and potential errors are minimised, particularly, as the successful encoding if the RFID tag is verified during the printing process. “The readability of the RFID signals in a metallic environment had initially been regarded as the main challenge. Interestingly, reading out the RFID tags in the steel sector via flexible tags that were sticking out at a right angle was much quicker and easier to solve than expected. It was a much bigger challenge to develop a special adhesive for applying the labels to the rough surfaces of the slabs which have to adhere reliably in spite of wet conditions or surface issues such as scale,” explains Karl Tochtermann the contribution of S+P Samson to the success of the project.
that has been bent away from a steel slab can still be read. However, the problem was that the solutions suggested by
other companies did not have sufficient adhesion or applying the labels would have required costly special processes
and systems in our Brazilian plant,” Loïc Feinbier recalls.
The breakthrough was achieved by the cooperation with the experts from S+P Samson GmbH who brought their many
years of experience with identification for steel logistics to the project.
S+P Samson developed an adhesive label made from a film which had the transponder part bent away from the slab like
a flag, via a simple perforation, so that it can be read. Another benefit: S+P labels and tags could be printed using a standard Lexmark laser printer which has an additional RFID unit fitted that writes the chips. As printing and RFID programming is done at the same time, the number of work steps and potential errors are minimised, particularly, as the successful encoding if the RFID tag is verified during the printing process. “The readability of the RFID signals in a metallic environment had initially been regarded as the main challenge. Interestingly, reading out the RFID tags in the steel sector via flexible tags that were sticking out at a right angle was much quicker and easier to solve than expected. It was a much bigger challenge to develop a special adhesive for applying the labels to the rough surfaces of the slabs which have to adhere reliably in spite of wet conditions or surface issues such as scale,” explains Karl Tochtermann the contribution of S+P Samson to the success of the project.
Operational Impact
Quantitative Benefit
Case Study missing?
Start adding your own!
Register with your work email and create a new case study profile for your business.
Related Case Studies.
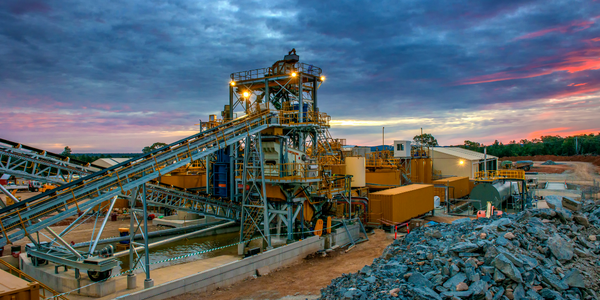
Case Study
Goldcorp: Internet of Things Enables the Mine of the Future
Goldcorp is committed to responsible mining practices and maintaining maximum safety for its workers. At the same time, the firm is constantly exploring ways to improve the efficiency of its operations, extend the life of its assets, and control costs. Goldcorp needed technology that can maximize production efficiency by tracking all mining operations, keep employees safe with remote operations and monitoring of hazardous work areas and control production costs through better asset and site management.

Case Study
KSP Steel Decentralized Control Room
While on-site in Pavlodar, Kazakhstan, the DAQRI team of Business Development and Solutions Architecture personnel worked closely with KSP Steel’s production leadership to understand the steel production process, operational challenges, and worker pain points.
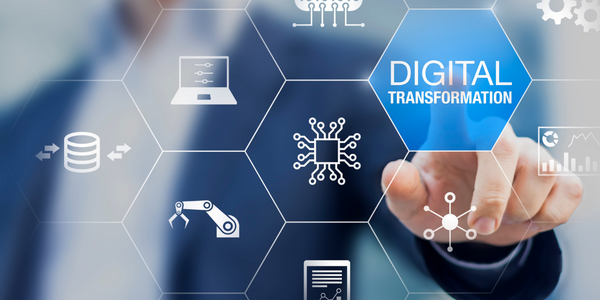
Case Study
Bluescope Steel on Path to Digitally Transform Operations and IT
Increasing competition and fluctuations in the construction market prompted BlueScope Steel to look toward digital transformation of its four businesses, including modern core applications and IT infrastructure. BlueScope needed to modernize its infrastructure and adopt new technologies to improve operations and supply chain efficiency while maintaining and updating an aging application portfolio.
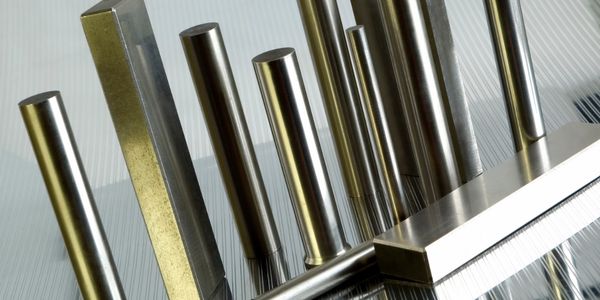
Case Study
RobotStudio Case Study: Benteler Automobiltechnik
Benteler has a small pipe business area for which they produce fuel lines and coolant lines made of aluminum for Porsche and other car manufacturers. One of the problems in production was that when Benteler added new products, production had too much downtime.
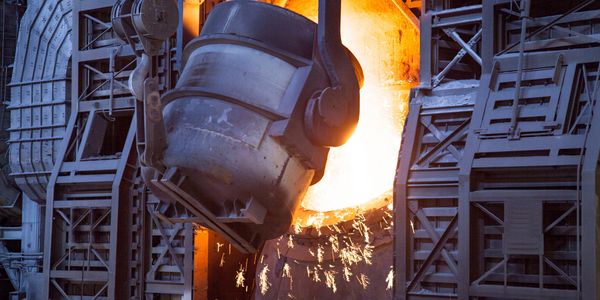
Case Study
Continuous Casting Machines in a Steel Factory
With a very broad range of applications, steel is an important material and has been developed into the most extensive alloy in the engineering world. Since delivering high quality is absolutely crucial for steel plants, ensuring maximum productivity and the best quality production are the keys to competitiveness in the steel industry. Additionally, working conditions in steel factories are not suitable for workers to stay in for long periods of time, so manufactures usually adopt various machines to complete the steel production processes. However, the precision of these machines is often overestimated and the lack of flexibility also makes supervisors unable to adjust operating procedures. A renowned steel factory in Asia planned to improve its Distributed Control System (DCS) of furnaces as well as addressing the problem of insufficient accuracy. However, most well-known international equipment suppliers can not provide a satisfactory solution and local maintenance because the project needed new technologies to more accurately control equipment operations. By implementing Advantech’s automated monitoring and control solution, steel factories can not only improve the manufacturing processes but can also allow users to add additional functions to the existing system so as to make sure the operation runs at high efficiency.
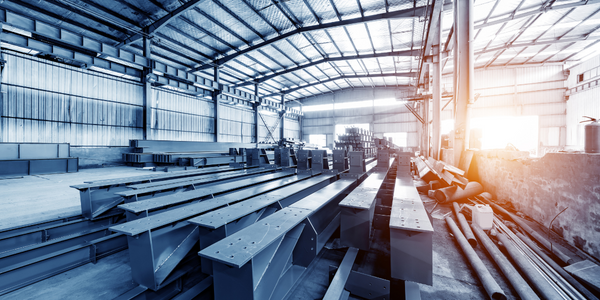
Case Study
Automated Predicitive Analytics For Steel/Metals Industry
Asset to be monitored: Wire Compactor that produces Steel RebarCustomer Faced The Following Challenges:Dependent upon machine uptime.Pressure cylinders within the compactor fail to control compression and speed causing problems in binding the coil.Equipment failure occurs in the final stage of production causing the entire line to stop, can you say bottleneck?Critical asset unequipped with sensors to produce data.