Automotive Parts Supplier Launches IoT Initiative in SixWeek Sprints Powered by PTC IoT Manufacturing Solutions
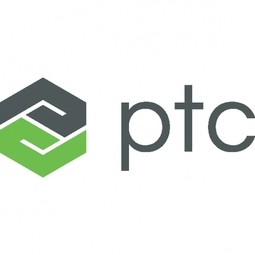
Customer Company Size
Large Corporate
Region
- America
Country
- United States
Product
- ThingWorx IoT Platform
- KEPServerEX
- IoT Gateway Advanced Plug-In
- Manufacturing Suite
Tech Stack
- IoT
- Cloud Computing
- Data Analytics
- ERP Systems
Implementation Scale
- Enterprise-wide Deployment
Impact Metrics
- Productivity Improvements
- Cost Savings
- Digital Expertise
Technology Category
- Platform as a Service (PaaS) - Connectivity Platforms
- Analytics & Modeling - Real Time Analytics
Applicable Industries
- Automotive
Applicable Functions
- Discrete Manufacturing
- Maintenance
Use Cases
- Predictive Maintenance
- Manufacturing System Automation
- Asset Health Management (AHM)
Services
- System Integration
- Data Science Services
About The Customer
HIROTEC AMERICA is part of the HIROTEC Group Companies, a $1.6 billion corporation with over 60 years of mass production experience and engineering discipline. With 26 facilities in nine countries around the world, HIROTEC Group is globally recognized as a premier automation manufacturing equipment and parts supplier. For over 50 years, top vehicle producers like General Motors and Mazda have used HIROTEC’s proven, high-quality industrial manufacturing concepts and systems. The parts and tooling supplier designs and builds roughly 7 million doors and 1.5 million exhaust systems a year, making it one of the largest private production companies in today’s global automotive market.
The Challenge
HIROTEC AMERICA, a part of the HIROTEC Group Companies, faced significant operational downtime issues. The machinery involved ran without condition-based monitoring, operating until a failure occurred. This reactive maintenance approach led to lost opportunities and inefficiencies. HIROTEC had been collecting industrial data from sensors and machines across customer production facilities and its own systems. However, this data was manually separated and stored across multiple sources, making it inaccessible for collective and systematic analysis. To improve quality, reduce downtime, and optimize production schedules, HIROTEC needed to implement a modern, automated solution that could gather maintenance and operational information into one source and offer actionable recommendations to its quality professionals.
The Solution
HIROTEC turned to the ThingWorx IoT Platform and Kepware’s KEPServerEX to enable company-wide device-to-cloud connectivity through one overarching toolset. The ThingWorx platform provided analytical insight into HIROTEC’s data through industrial data streamed from the IoT Gateway for KEPServerEX, an advanced plug-in capable of pushing information from KEPServerEX into Big Data and analytic software applications. HIROTEC collaborated with representatives at PTC to build an IoT framework supported by short, six-week Agile sprints. The Scrum model provided company executives with visible and quantifiable progress in just weeks. HIROTEC’s North American shop in Detroit, Michigan was chosen as the test bed for the first small sprint because of the unique data types generated among its eight Computer Numerical Control (CNC) machines.
Operational Impact
Case Study missing?
Start adding your own!
Register with your work email and create a new case study profile for your business.
Related Case Studies.
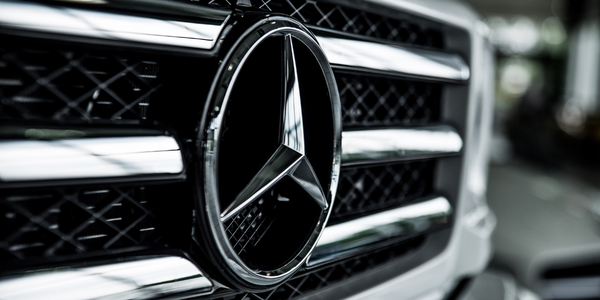
Case Study
Integral Plant Maintenance
Mercedes-Benz and his partner GAZ chose Siemens to be its maintenance partner at a new engine plant in Yaroslavl, Russia. The new plant offers a capacity to manufacture diesel engines for the Russian market, for locally produced Sprinter Classic. In addition to engines for the local market, the Yaroslavl plant will also produce spare parts. Mercedes-Benz Russia and his partner needed a service partner in order to ensure the operation of these lines in a maintenance partnership arrangement. The challenges included coordinating the entire maintenance management operation, in particular inspections, corrective and predictive maintenance activities, and the optimizing spare parts management. Siemens developed a customized maintenance solution that includes all electronic and mechanical maintenance activities (Integral Plant Maintenance).

Case Study
Monitoring of Pressure Pumps in Automotive Industry
A large German/American producer of auto parts uses high-pressure pumps to deburr machined parts as a part of its production and quality check process. They decided to monitor these pumps to make sure they work properly and that they can see any indications leading to a potential failure before it affects their process.