Technology Category
- Analytics & Modeling - Digital Twin / Simulation
- Sensors - Environmental Sensors
Applicable Industries
- Automotive
Applicable Functions
- Product Research & Development
- Quality Assurance
Use Cases
- Virtual Prototyping & Product Testing
- Virtual Reality
Services
- Hardware Design & Engineering Services
- Testing & Certification
About The Customer
Banco Products India Ltd. is a leading manufacturer and supplier of equipment such as engine cooling systems and sealing gaskets for commercial vehicles, passenger vehicles, and industrial products. The company is one of India’s largest exporters of aftermarket radiators to Europe, with a growing presence in North America, the Middle-East, Africa, and South America. They design a range of radiators that must operate reliably under a wide range of conditions, catering to the diverse cooling requirements of various vehicles.
The Challenge
Banco Products India Ltd., a leading manufacturer and supplier of equipment such as engine cooling systems and sealing gaskets, faced a significant challenge in the development of their radiators. Radiators, key components in automotive engine cooling systems, must be designed to meet a wide range of conditions due to the diversity of vehicles. The radiator's complex geometry, which includes several thin sheets with thousands of dimples in the radiator core, is required to meet cooling performance and strength requirements. This complexity made simulation difficult. Furthermore, radiator performance is usually determined by the coolant outlet temperature, and Banco designs several types of radiators to meet the cooling requirements of various vehicles. Physically testing each design was not only time-consuming but also costly.
The Solution
To overcome these challenges, Banco developed an engineering approach to effectively use simulation for design. They employed the ANSYS product family to prepare the complex geometry for simulation. The CAD geometry was cleaned up in ANSYS DesignModeler within ANSYS Workbench, and high-quality meshes were generated using ANSYS meshing capabilities to obtain accurate CFD results. The coolant outlet temperature was accurately predicted using ANSYS Fluent technology, accelerated by ANSYS HPC. Additionally, the natural frequency for the radiator was determined, and stress analysis of the radiator header tanks was performed using ANSYS Mechanical. This approach not only reduced the need for physical prototyping but also delivered cost savings, met higher performance and strength targets, and accelerated product development.
Operational Impact
Quantitative Benefit
Case Study missing?
Start adding your own!
Register with your work email and create a new case study profile for your business.
Related Case Studies.
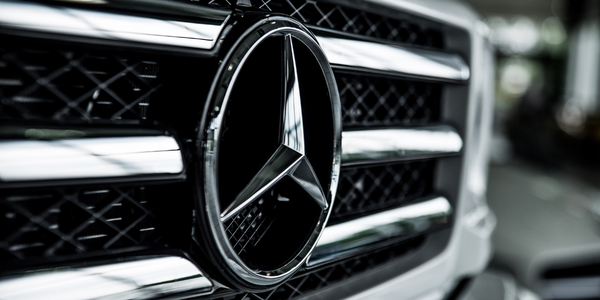
Case Study
Integral Plant Maintenance
Mercedes-Benz and his partner GAZ chose Siemens to be its maintenance partner at a new engine plant in Yaroslavl, Russia. The new plant offers a capacity to manufacture diesel engines for the Russian market, for locally produced Sprinter Classic. In addition to engines for the local market, the Yaroslavl plant will also produce spare parts. Mercedes-Benz Russia and his partner needed a service partner in order to ensure the operation of these lines in a maintenance partnership arrangement. The challenges included coordinating the entire maintenance management operation, in particular inspections, corrective and predictive maintenance activities, and the optimizing spare parts management. Siemens developed a customized maintenance solution that includes all electronic and mechanical maintenance activities (Integral Plant Maintenance).

Case Study
Monitoring of Pressure Pumps in Automotive Industry
A large German/American producer of auto parts uses high-pressure pumps to deburr machined parts as a part of its production and quality check process. They decided to monitor these pumps to make sure they work properly and that they can see any indications leading to a potential failure before it affects their process.