Technology Category
- Platform as a Service (PaaS) - Application Development Platforms
- Sensors - Temperature Sensors
Applicable Industries
- Automotive
- Mining
Applicable Functions
- Quality Assurance
Use Cases
- Behavior & Emotion Tracking
- Predictive Quality Analytics
Services
- Testing & Certification
About The Customer
Bender Group is a market leader in monitoring systems for electrical safety. With over six decades of experience, the company has developed and produced top-quality products for the measurement and monitoring of electrical systems. Bender's products are used worldwide and cater to various sectors including hospitals, mining, automotive industry, machinery manufacturers, ships and submarines, as well as e-mobility, wind power and solar power installations. Founded in 1971 with 28 employees, Bender now employs more than 600 people across the globe. The company is headquartered in Gruenberg, Germany and has offices, agencies and distributors in more than 60 countries.
The Challenge
Bender Group, a global leader in monitoring systems for electrical safety, was grappling with inefficient internal processes that were largely paper-based. These processes were not only time-consuming but also prone to errors and delays, which affected the overall productivity of the company. The company's Quality Management team, responsible for maintaining the high-quality standards of Bender's products, was particularly affected by these inefficiencies. The paper-based process for submitting faults was error-prone and typically took three to four days. Additionally, Bender was facing the challenge of knowledge retention, with many of its long-serving employees nearing retirement. The company wanted to capture and retain the valuable knowledge and understanding of its systems and products that these employees possessed.
The Solution
To address these challenges, Bender Group partnered with IPI GmbH, a Nintex partner, to introduce a SharePoint 2010-based collaboration environment with the Nintex Platform. This solution was aimed at capturing employee knowledge and automating the previously paper-based processes. Nintex's Advanced Workflows were used to rename documents and images uploaded to the company intranet before they were published, ensuring that file names met set naming conventions. The Quality Management team benefited from an electronic form submission process, which was routed via workflow to the team members. This workflow automation enabled the team to receive product failure reports on the same day they were made, thereby improving their ability to accurately report and react to faults.
Operational Impact
Quantitative Benefit
Case Study missing?
Start adding your own!
Register with your work email and create a new case study profile for your business.
Related Case Studies.
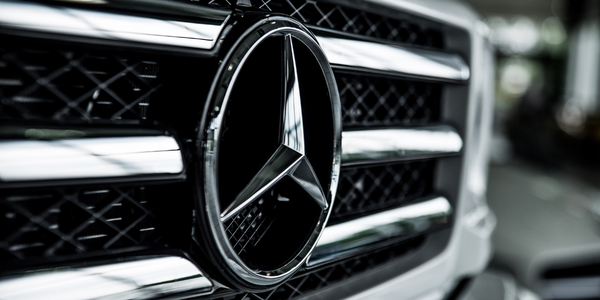
Case Study
Integral Plant Maintenance
Mercedes-Benz and his partner GAZ chose Siemens to be its maintenance partner at a new engine plant in Yaroslavl, Russia. The new plant offers a capacity to manufacture diesel engines for the Russian market, for locally produced Sprinter Classic. In addition to engines for the local market, the Yaroslavl plant will also produce spare parts. Mercedes-Benz Russia and his partner needed a service partner in order to ensure the operation of these lines in a maintenance partnership arrangement. The challenges included coordinating the entire maintenance management operation, in particular inspections, corrective and predictive maintenance activities, and the optimizing spare parts management. Siemens developed a customized maintenance solution that includes all electronic and mechanical maintenance activities (Integral Plant Maintenance).
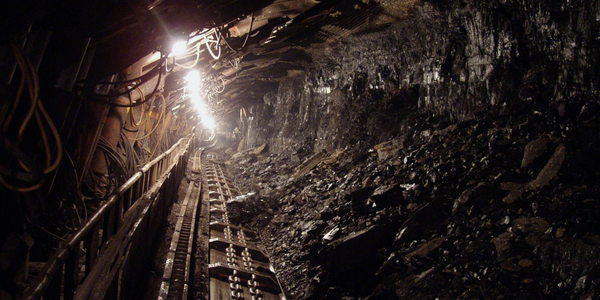
Case Study
Underground Mining Safety
The goal was to produce a safety system to monitor and support underground mining operations; existing systems were either too simple (i.e. phone line) or overly complex and expensive, inhibiting deployment, and providing little-to-no support in event of an accident. Given the dangerous nature of the mining work environment and the strict regulations placed on the industry, the solution would have to comply with Mine Safety and Health Administration (MSHA) regulations. Yet the product needed to allow for simple deployment to truly be a groundbreaking solution - increasing miner safety and changing daily operations for the better.

Case Study
Monitoring of Pressure Pumps in Automotive Industry
A large German/American producer of auto parts uses high-pressure pumps to deburr machined parts as a part of its production and quality check process. They decided to monitor these pumps to make sure they work properly and that they can see any indications leading to a potential failure before it affects their process.