Technology Category
- Analytics & Modeling - Digital Twin / Simulation
Applicable Industries
- Automotive
- Equipment & Machinery
Applicable Functions
- Product Research & Development
- Quality Assurance
Use Cases
- Additive Manufacturing
- Manufacturing Process Simulation
Services
- Testing & Certification
About The Customer
Ford Motor Company is a Fortune 50 automotive company that operates plants worldwide, producing millions of vehicles annually. Committed to being the world's most reliable mobility and intelligent vehicle design company, Ford maintains engineering centers in various locations, including the USA, India, Mexico, Germany, and Brazil. The company has been working with Altair for over 30 years to support its product development activities. Today, Ford employs Altair software globally to aid in the development of its cars, trucks, and heavy equipment.
The Challenge
Ford Motor Company, a global automotive giant, was facing challenges in the realm of Additive Manufacturing (AM), a process that involves adding material layer by layer to manufacture components. This technology, while promising significant benefits such as cost reduction, tooling improvements, and the ability to create complex designs, is relatively new. As a result, the industry's expertise in AM is not on par with traditional manufacturing. Ford found it challenging to set printer parameters correctly, as incorrect settings could lead to structural failures, performance deficiencies, and aesthetic issues in the printed components. The pursuit of mechanical design efficiency often led to overlooking critical considerations.
The Solution
Ford implemented AM along with Altair Inspire's 3D printing simulation within their product development process. This combination helped Ford identify potential error states throughout the manufacturing lifecycle, providing crucial information to optimize and ensure first-time quality through design. The focus was on bracket design, which aimed to improve heat management via internal cooling channel design. The simulation allowed the creation of complex, optimal geometries for brackets, promoting more effective heat dissipation and better mechanical behavior and dimension control. Altair Inspire's 3D printing simulation, coupled with a design of experiment process created with Altair HyperStudy, helped solve issues typically encountered at the printing stage, such as detachment of supports and aesthetic finish problems. It also enabled printer parameter optimization for peak performance.
Operational Impact
Case Study missing?
Start adding your own!
Register with your work email and create a new case study profile for your business.
Related Case Studies.
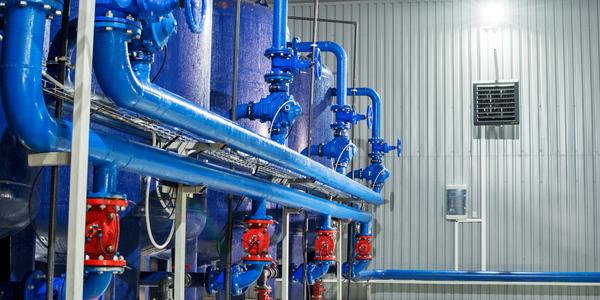
Case Study
Smart Water Filtration Systems
Before working with Ayla Networks, Ozner was already using cloud connectivity to identify and solve water-filtration system malfunctions as well as to monitor filter cartridges for replacements.But, in June 2015, Ozner executives talked with Ayla about how the company might further improve its water systems with IoT technology. They liked what they heard from Ayla, but the executives needed to be sure that Ayla’s Agile IoT Platform provided the security and reliability Ozner required.
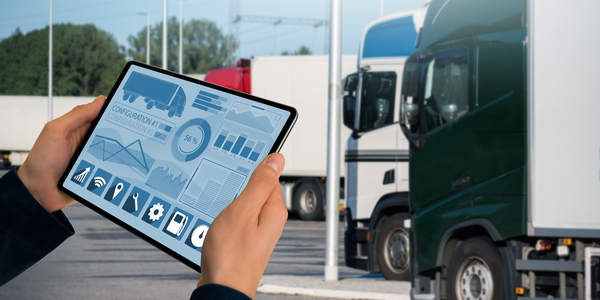
Case Study
IoT enabled Fleet Management with MindSphere
In view of growing competition, Gämmerler had a strong need to remain competitive via process optimization, reliability and gentle handling of printed products, even at highest press speeds. In addition, a digitalization initiative also included developing a key differentiation via data-driven services offers.
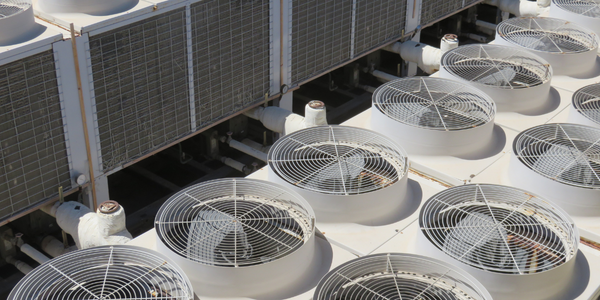
Case Study
Predictive Maintenance for Industrial Chillers
For global leaders in the industrial chiller manufacturing, reliability of the entire production process is of the utmost importance. Chillers are refrigeration systems that produce ice water to provide cooling for a process or industrial application. One of those leaders sought a way to respond to asset performance issues, even before they occur. The intelligence to guarantee maximum reliability of cooling devices is embedded (pre-alarming). A pre-alarming phase means that the cooling device still works, but symptoms may appear, telling manufacturers that a failure is likely to occur in the near future. Chillers who are not internet connected at that moment, provide little insight in this pre-alarming phase.
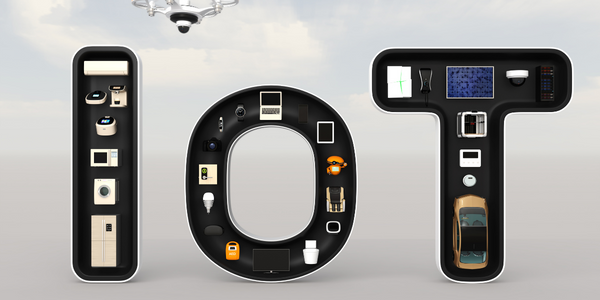
Case Study
Premium Appliance Producer Innovates with Internet of Everything
Sub-Zero faced the largest product launch in the company’s history:It wanted to launch 60 new products as scheduled while simultaneously opening a new “greenfield” production facility, yet still adhering to stringent quality requirements and manage issues from new supply-chain partners. A the same time, it wanted to increase staff productivity time and collaboration while reducing travel and costs.
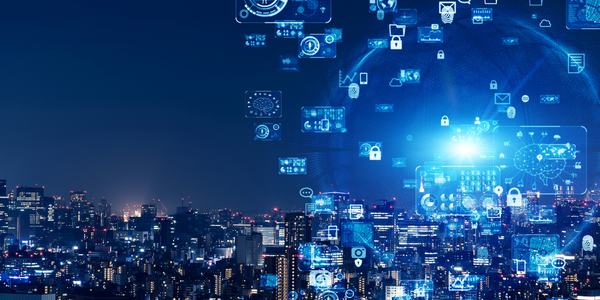
Case Study
Integration of PLC with IoT for Bosch Rexroth
The application arises from the need to monitor and anticipate the problems of one or more machines managed by a PLC. These problems, often resulting from the accumulation over time of small discrepancies, require, when they occur, ex post technical operations maintenance.
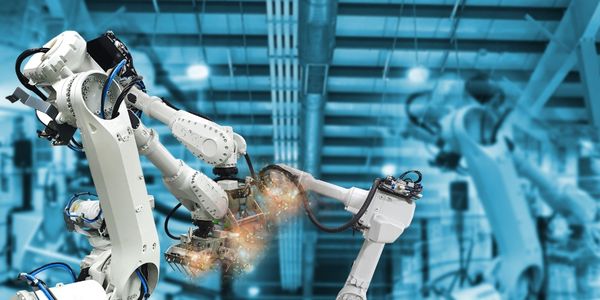
Case Study
Robot Saves Money and Time for US Custom Molding Company
Injection Technology (Itech) is a custom molder for a variety of clients that require precision plastic parts for such products as electric meter covers, dental appliance cases and spools. With 95 employees operating 23 molding machines in a 30,000 square foot plant, Itech wanted to reduce man hours and increase efficiency.