- Application Infrastructure & Middleware - Middleware, SDKs & Libraries
- Networks & Connectivity - 5G
- Electrical Grids
- Electronics
- Product Research & Development
- Additive Manufacturing
- Manufacturing Process Simulation
Breville is a global brand that was founded in Sydney in 1932. It has become an iconic brand that enhances people’s lives through thoughtful design and brilliant innovation, delivering kitchen products to more than 70 countries around the globe. Its design facility in Sydney is staffed by around 200 engineers, industrial designers, product managers, and scientists, among other professionals. This fast-paced business requires a high degree of flexibility, which is why Breville decided to invest in cutting-edge tools to help with initiatives that support this growth and empower employees to make decisions quickly and accelerate the processes and innovations.
Breville, a global kitchen products brand, was facing challenges in its design facility in Sydney. The facility, staffed by around 200 professionals, required a high degree of flexibility to support its fast-paced business. The biggest problem was communication. Information was disseminated through multiple channels, leading to reduced efficiency and difficulty in completing projects on time. The communication between the designer and the manufacturer was inconsistent, leading to issues with ensuring the correct revision drawings were used. Additionally, the manufacturer would select components based on solutions that worked for them, which may not have been the best fit for the specific project.
Breville decided to invest in Altium 365 Pro to help with initiatives that support growth and empower employees to make decisions quickly and accelerate processes and innovations. Altium 365 Pro provided a platform where all communication stayed within the project, providing greater transparency, traceability, and accountability of all data. It also improved the communication between the designer and the manufacturer, ensuring the correct revision drawings were used. Breville also created and owned the component library, so the manufacturer could only select components from that library. The parts chosen were reliable components from preferred suppliers. Breville could now manage the component lifecycle, reducing time spent on sourcing by staying organized and with access to real-time supplier availability and pricing.
Case Study missing?
Start adding your own!
Register with your work email and create a new case study profile for your business.
Related Case Studies.
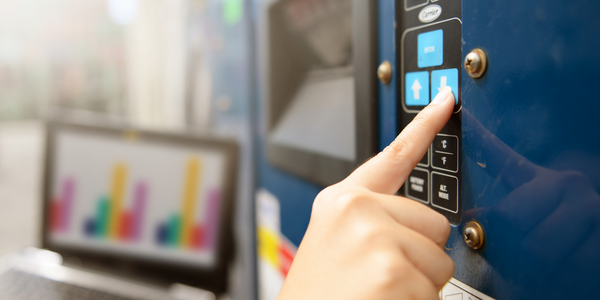

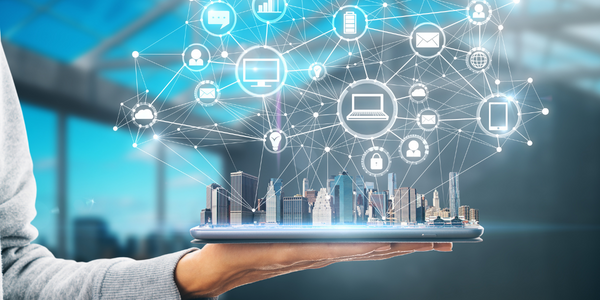
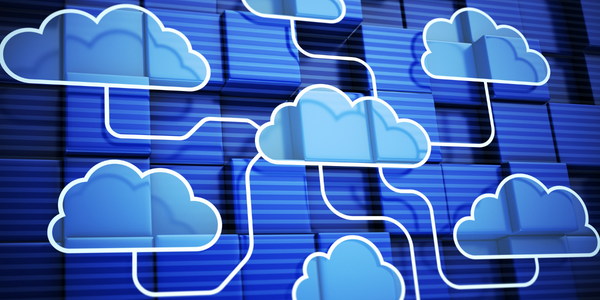