Technology Category
- Analytics & Modeling - Digital Twin / Simulation
- Sensors - Haptic Sensors
Applicable Industries
- Cement
- Oil & Gas
Applicable Functions
- Product Research & Development
- Quality Assurance
Use Cases
- Digital Twin
- Virtual Reality
Services
- System Integration
- Testing & Certification
About The Customer
Baker Hughes is a leading supplier of oilfield services, products, technology, and systems to the worldwide oil and natural gas industry. The company operates globally with approximately 60,000 employees and is headquartered in Houston, Texas. In 2013, the company reported a revenue of $22.4 billion USD. Baker Hughes is known for its innovative solutions to the challenges faced by the oil and natural gas industry, particularly in the areas of offshore deep-water drilling, Arctic environments, shale and hydraulic fracturing, and adherence to strict environmental and safety regulations.
The Challenge
Baker Hughes, a leading supplier of oilfield services, products, technology, and systems to the worldwide oil and natural gas industry, was facing several environmental and technological challenges. These included operating in offshore deep-water and Arctic environments, dealing with shale and hydraulic fracturing, and adhering to stricter environmental and safety regulations. Technological challenges included drilling deeper wells, dealing with extreme pressures and temperatures, and handling unconventional geological variations. The company was also tasked with the development of an Expandable Liner Hanger System, a mechanical system used to attach a liner string to the bottom of a previously run casing string during wellbore construction operations within the oil and gas industry. This system is used to hang heavier liner under extreme deep-water environment, subsalt plays, or deviated wells.
The Solution
To overcome these challenges, Baker Hughes integrated CAE Simulation with Product Development. This approach maximized the probability of product success, product quality & reliability, customer satisfaction, and employee morale. It also minimized the development cost and time by eliminating waste. The integration of CAE Simulation with PDM helped to develop a product with a “Right First Time” strategy, understand the design limitations, constraints, assembly interactions in early stages of development, and reduce the number of prototypes. The company followed a seven-step CAE Simulation methodology that included FE model building, verification, initial validation, refinement or rebuilding, optimization, reliability assessment/improvement, and iteration. This methodology was used to accelerate the development of the Expandable Liner Hanger System design, predict its hanging capacity and sealing integrity, optimize its performance, and improve its reliability.
Operational Impact
Quantitative Benefit
Case Study missing?
Start adding your own!
Register with your work email and create a new case study profile for your business.
Related Case Studies.
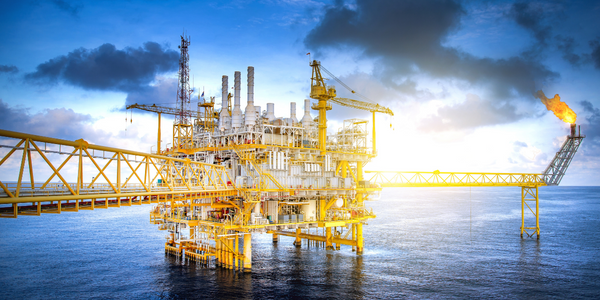
Case Study
Taking Oil and Gas Exploration to the Next Level
DownUnder GeoSolutions (DUG) wanted to increase computing performance by 5 to 10 times to improve seismic processing. The solution must build on current architecture software investments without sacrificing existing software and scale computing without scaling IT infrastructure costs.
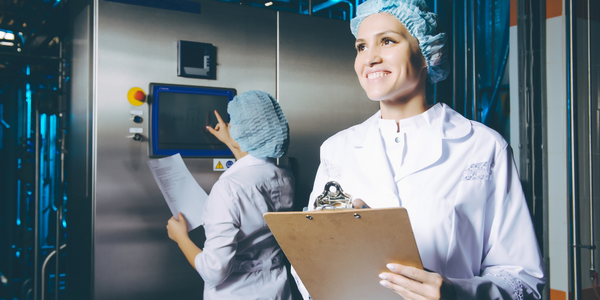
Case Study
Remote Wellhead Monitoring
Each wellhead was equipped with various sensors and meters that needed to be monitored and controlled from a central HMI, often miles away from the assets in the field. Redundant solar and wind generators were installed at each wellhead to support the electrical needs of the pumpstations, temperature meters, cameras, and cellular modules. In addition to asset management and remote control capabilities, data logging for remote surveillance and alarm notifications was a key demand from the customer. Terra Ferma’s solution needed to be power efficient, reliable, and capable of supporting high-bandwidth data-feeds. They needed a multi-link cellular connection to a central server that sustained reliable and redundant monitoring and control of flow meters, temperature sensors, power supply, and event-logging; including video and image files. This open-standard network needed to interface with the existing SCADA and proprietary network management software.
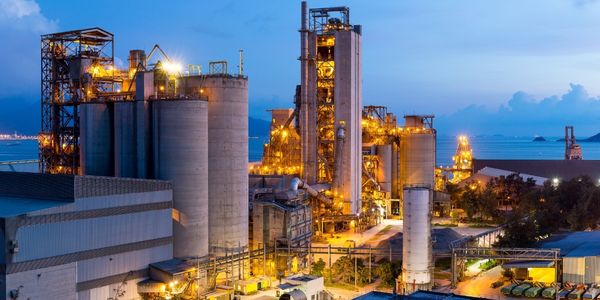
Case Study
System 800xA at Indian Cement Plants
Chettinad Cement recognized that further efficiencies could be achieved in its cement manufacturing process. It looked to investing in comprehensive operational and control technologies to manage and derive productivity and energy efficiency gains from the assets on Line 2, their second plant in India.
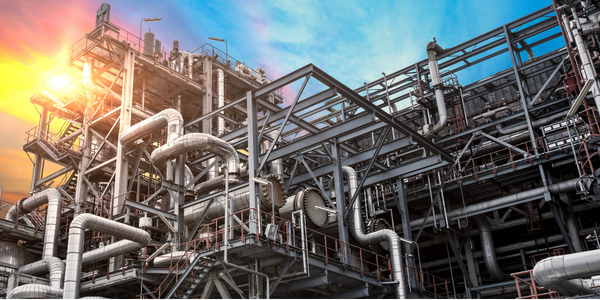
Case Study
Refinery Saves Over $700,000 with Smart Wireless
One of the largest petroleum refineries in the world is equipped to refine various types of crude oil and manufacture various grades of fuel from motor gasoline to Aviation Turbine Fuel. Due to wear and tear, eight hydrogen valves in each refinery were leaking, and each cost $1800 per ton of hydrogen vented. The plant also had leakage on nearly 30 flare control hydrocarbon valves. The refinery wanted a continuous, online monitoring system that could catch leaks early, minimize hydrogen and hydrocarbon production losses, and improve safety for maintenance.