Customer Company Size
Large Corporate
Region
- America
Country
- United States
- Canada
Product
- TIBCO Spotfire
- ZEMA
Tech Stack
- Self-service business intelligence
- Data management
- Statistical quantitative modeling
Implementation Scale
- Enterprise-wide Deployment
Impact Metrics
- Productivity Improvements
- Customer Satisfaction
- Digital Expertise
Technology Category
- Analytics & Modeling - Predictive Analytics
- Analytics & Modeling - Real Time Analytics
- Application Infrastructure & Middleware - Data Exchange & Integration
Applicable Industries
- Metals
- Transportation
Applicable Functions
- Business Operation
- Quality Assurance
Use Cases
- Real-Time Location System (RTLS)
Services
- Data Science Services
- System Integration
About The Customer
Cargill is a global corporation specializing in food, agriculture, financial, and industrial products and services. The company operates in 70 countries and employs over 155,000 people. Cargill's Energy, Transportation, and Metals (ETM) division focuses on managing supply chains in these sectors, leveraging commercial expertise to optimize operations. The division's unique combination of commercial know-how and supply chain management capabilities makes it a key player in the energy and commodity markets.
The Challenge
Like many companies in the energy industry, the challenge for Cargill was the volume of its diverse data and the difficulty of processing it quickly to enable fast response to market events. Without a strategic partnership, Cargill would have had to develop these solutions internally, which would not be ideal. The company needed a way to manage and analyze large volumes of data efficiently to make timely and informed decisions.
The Solution
To address its challenges, Cargill partnered with ZE PowerGroup and TIBCO, combining TIBCO’s self-service business intelligence capabilities with ZE’s data management expertise. ZE’s ZEMA software suite, which includes TIBCO Spotfire as an embedded capability, was implemented to streamline data collection, analysis, and visualization. Cargill started by building a crude refinery research analysis dashboard, transforming a 300,000-row spreadsheet into a comprehensive analytical tool. This new framework allowed Cargill to quickly see and understand results across its refinery complex, including turnarounds, capacity, yields, and margins. The partnership enabled Cargill to develop trading tools in days rather than months, significantly improving its market responsiveness.
Operational Impact
Quantitative Benefit
Case Study missing?
Start adding your own!
Register with your work email and create a new case study profile for your business.
Related Case Studies.
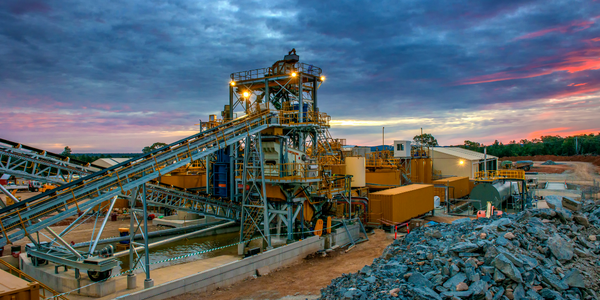
Case Study
Goldcorp: Internet of Things Enables the Mine of the Future
Goldcorp is committed to responsible mining practices and maintaining maximum safety for its workers. At the same time, the firm is constantly exploring ways to improve the efficiency of its operations, extend the life of its assets, and control costs. Goldcorp needed technology that can maximize production efficiency by tracking all mining operations, keep employees safe with remote operations and monitoring of hazardous work areas and control production costs through better asset and site management.

Case Study
KSP Steel Decentralized Control Room
While on-site in Pavlodar, Kazakhstan, the DAQRI team of Business Development and Solutions Architecture personnel worked closely with KSP Steel’s production leadership to understand the steel production process, operational challenges, and worker pain points.
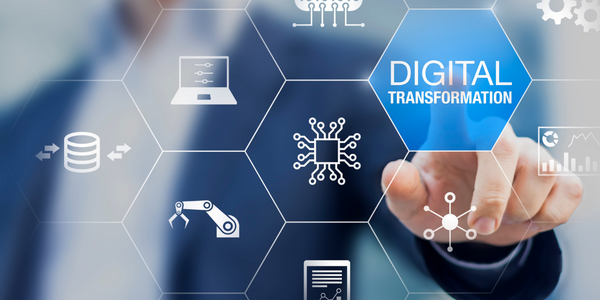
Case Study
Bluescope Steel on Path to Digitally Transform Operations and IT
Increasing competition and fluctuations in the construction market prompted BlueScope Steel to look toward digital transformation of its four businesses, including modern core applications and IT infrastructure. BlueScope needed to modernize its infrastructure and adopt new technologies to improve operations and supply chain efficiency while maintaining and updating an aging application portfolio.
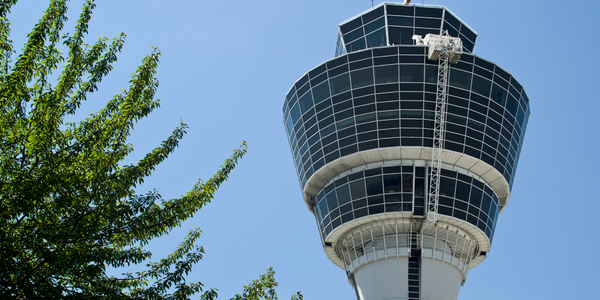
Case Study
Airport SCADA Systems Improve Service Levels
Modern airports are one of the busiest environments on Earth and rely on process automation equipment to ensure service operators achieve their KPIs. Increasingly airport SCADA systems are being used to control all aspects of the operation and associated facilities. This is because unplanned system downtime can cost dearly, both in terms of reduced revenues and the associated loss of customer satisfaction due to inevitable travel inconvenience and disruption.
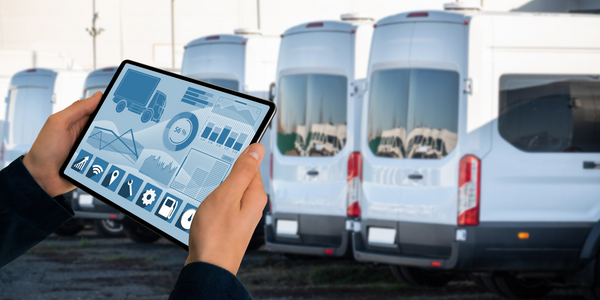
Case Study
IoT-based Fleet Intelligence Innovation
Speed to market is precious for DRVR, a rapidly growing start-up company. With a business model dependent on reliable mobile data, managers were spending their lives trying to negotiate data roaming deals with mobile network operators in different countries. And, even then, service quality was a constant concern.
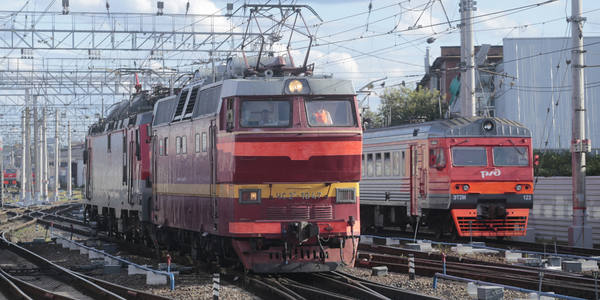
Case Study
Digitize Railway with Deutsche Bahn
To reduce maintenance costs and delay-causing failures for Deutsche Bahn. They need manual measurements by a position measurement system based on custom-made MEMS sensor clusters, which allow autonomous and continuous monitoring with wireless data transmission and long battery. They were looking for data pre-processing solution in the sensor and machine learning algorithms in the cloud so as to detect critical wear.