Copper Mountain Ski Resort Lifts Customer Experience with Superior Scanning Technology from Honeywell
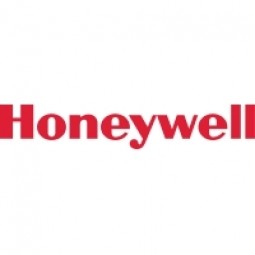
Customer Company Size
Large Corporate
Region
- America
Country
- United States
Product
- Honeywell CN70a
- Honeywell SG20 USB
Tech Stack
- Barcode Scanning Technology
- Wireless Network Integration
Implementation Scale
- Enterprise-wide Deployment
Impact Metrics
- Customer Satisfaction
- Productivity Improvements
- Revenue Growth
Technology Category
- Functional Applications - Inventory Management Systems
- Functional Applications - Remote Monitoring & Control Systems
- Networks & Connectivity - Wireless Local Area Network
Applicable Functions
- Facility Management
- Warehouse & Inventory Management
Use Cases
- Inventory Management
- Track & Trace of Assets
- Remote Control
Services
- System Integration
- Hardware Design & Engineering Services
About The Customer
Copper Mountain is a renowned ski resort located in the heart of the Rocky Mountains. Spanning over 2,500 acres of ski terrain, it attracts a large number of visitors, with around 10,000 skiers using the ski lifts each day. The resort is known for its extensive and diverse ski areas, catering to skiers of all levels. Copper Mountain places a high emphasis on customer experience and operational efficiency, making it a popular destination for winter sports enthusiasts. The resort's commitment to providing top-notch services and facilities is evident in its continuous efforts to upgrade and enhance its technological infrastructure.
The Challenge
Copper Mountain, a premier ski resort, faced significant challenges in managing the high volume of skiers entering their lifts daily. With over 10,000 skiers on average and up to 14,000 on busy days, the resort needed a fast and efficient scanning solution to ensure smooth operations. The existing scanning devices were heavy, had poor battery life, and struggled in extreme weather conditions, leading to frequent network drop-offs and potential revenue loss. The resort required a robust, lightweight, and reliable scanning solution to handle the high throughput and harsh environmental conditions.
The Solution
Copper Mountain partnered with Honeywell and SK&T to implement a superior scanning solution. They deployed the Honeywell CN70a mobile device for lift operations, which proved to be significantly lighter and more efficient than previous scanners. The CN70a's robust battery life ensured uninterrupted operations throughout the day, eliminating the need for frequent battery changes. Additionally, the device's rugged design allowed it to perform reliably in extreme weather conditions, from 45 degrees Fahrenheit to -45 degrees Fahrenheit. For their retail and rental locations, Copper Mountain utilized the Honeywell SG20 USB wired scanners, which offered versatile scanning capabilities, including reading damaged barcodes and operating at various angles. The CN70a was also employed for retail inventory management during the off-season, providing faster and more accurate scans.
Operational Impact
Quantitative Benefit
Case Study missing?
Start adding your own!
Register with your work email and create a new case study profile for your business.
Related Case Studies.
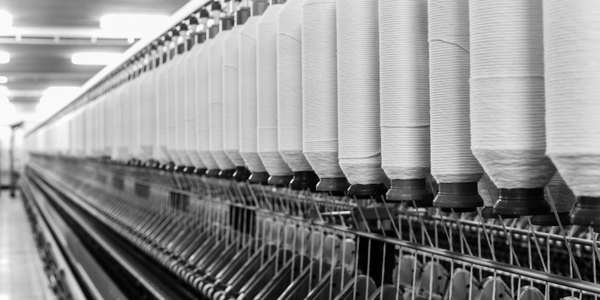
Case Study
IoT Applications and Upgrades in Textile Plant
At any given time, the textile company’s manufacturing facility has up to 2,000 textile carts in use. These carts are pushed from room to room, carrying materials or semi-finished products. Previously, a paper with a hand-written description was attached to each cart. This traditional method of processing made product tracking extremely difficult. Additionally, making sure that every cart of materials or semi-finished products went to its correct processing work station was also a problem. Therefore, the company desired an intelligent solution for tracking assets at their factories. They also wanted a solution that would help them collect process data so they could improve their manufacturing efficiency.
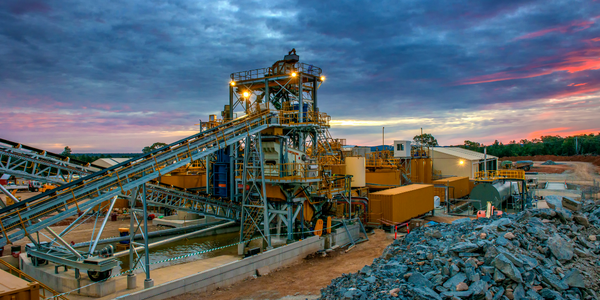
Case Study
Goldcorp: Internet of Things Enables the Mine of the Future
Goldcorp is committed to responsible mining practices and maintaining maximum safety for its workers. At the same time, the firm is constantly exploring ways to improve the efficiency of its operations, extend the life of its assets, and control costs. Goldcorp needed technology that can maximize production efficiency by tracking all mining operations, keep employees safe with remote operations and monitoring of hazardous work areas and control production costs through better asset and site management.
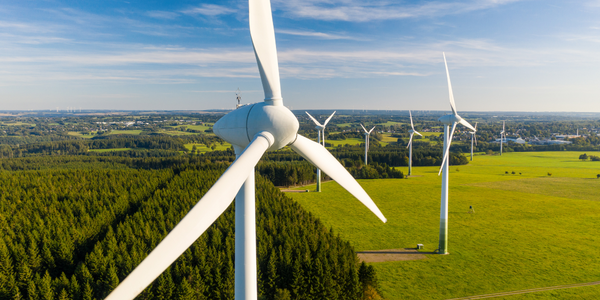
Case Study
Remote Monitoring and Control for a Windmill Generator
As concerns over global warming continue to grow, green technologies are becoming increasingly popular. Wind turbine companies provide an excellent alternative to burning fossil fuels by harnessing kinetic energy from the wind and converting it into electricity. A typical wind farm may include over 80 wind turbines so efficient and reliable networks to manage and control these installations are imperative. Each wind turbine includes a generator and a variety of serial components such as a water cooler, high voltage transformer, ultrasonic wind sensors, yaw gear, blade bearing, pitch cylinder, and hub controller. All of these components are controlled by a PLC and communicate with the ground host. Due to the total integration of these devices into an Ethernet network, one of our customers in the wind turbine industry needed a serial-to-Ethernet solution that can operate reliably for years without interruption.
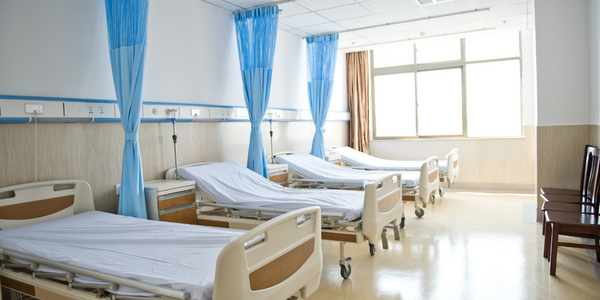
Case Study
Hospital Inventory Management
The hospital supply chain team is responsible for ensuring that the right medical supplies are readily available to clinicians when and where needed, and to do so in the most efficient manner possible. However, many of the systems and processes in use at the cancer center for supply chain management were not best suited to support these goals. Barcoding technology, a commonly used method for inventory management of medical supplies, is labor intensive, time consuming, does not provide real-time visibility into inventory levels and can be prone to error. Consequently, the lack of accurate and real-time visibility into inventory levels across multiple supply rooms in multiple hospital facilities creates additional inefficiency in the system causing over-ordering, hoarding, and wasted supplies. Other sources of waste and cost were also identified as candidates for improvement. Existing systems and processes did not provide adequate security for high-cost inventory within the hospital, which was another driver of cost. A lack of visibility into expiration dates for supplies resulted in supplies being wasted due to past expiry dates. Storage of supplies was also a key consideration given the location of the cancer center’s facilities in a dense urban setting, where space is always at a premium. In order to address the challenges outlined above, the hospital sought a solution that would provide real-time inventory information with high levels of accuracy, reduce the level of manual effort required and enable data driven decision making to ensure that the right supplies were readily available to clinicians in the right location at the right time.
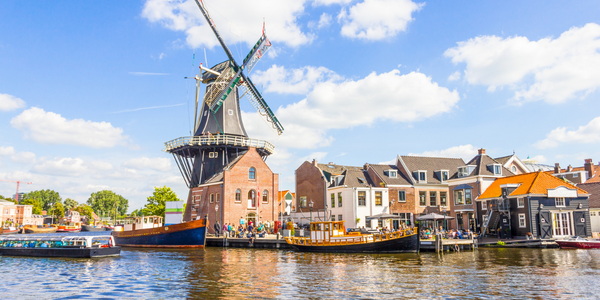
Case Study
Buoy Status Monitoring with LoRa
The Netherlands are well-known for their inland waterways, canals, sluices and of course port activities. The Dutch Ministry of Infrastructure indicates that there are thousands of buoys and fixed items in and near water environments that would profit from IoT monitoring. One of the problems with buoys for example, is that they get hit by ships and the anchor cable breaks. Without connectivity, it takes quite some time to find out that something has happened with that buoy. Not to mention the costs of renting a boat to go to the buoy to fix it. Another important issue, is that there is no real-time monitoring of the buoys at this moment. Only by physically visiting the object on the water, one gains insight in its status.