Customer Company Size
Large Corporate
Region
- Asia
Country
- Taiwan
Product
- Advantech ABox
Tech Stack
- POS System
Implementation Scale
- Enterprise-wide Deployment
Impact Metrics
- Productivity Improvements
- Customer Satisfaction
Technology Category
- Functional Applications - Remote Monitoring & Control Systems
Applicable Industries
- Oil & Gas
Applicable Functions
- Sales & Marketing
- Business Operation
Use Cases
- Remote Asset Management
Services
- System Integration
About The Customer
The CPC Corporation is a state-run enterprise in Taiwan, responsible for the development and supply of petroleum and natural gas. As a cornerstone of Taiwan’s petrochemical industry, CPC is the leading enterprise in the country, employing approximately 14,977 employees and operating various functional units across the island. As the number one gas supplier in Taiwan, CPC gas stations are expected to provide speedy and comprehensive services.
The Challenge
CPC Corporation, Taiwan's leading enterprise in the development and supply of petroleum and natural gas, faced a challenge in ensuring operational efficiency in semi-outdoor environments. The company needed a high-performance POS system that could withstand environmental challenges associated with gas stations, including resistance to water, dust, shock, and oil. Additionally, the company needed to protect their customer database from unauthorized employee access, making traditional POS systems inappropriate.
The Solution
Advantech recommended its ABox computer with diverse I/O for connecting an external monitor and keyboard to provide a system that could function as a POS terminal. This strategy would enable managers to lock the computer in the checkout counter and thereby prevent unauthorized access to confidential financial information. The ABox Series computers are equipped with the latest Intel processor to deliver the extreme performance required, and their ultra-compact design saves installation space. The system’s fanless aluminum housing ensures not only ruggedness and increased heat dissipation, but also water, dust, shock, and oil resistance/tolerance, making it the ideal solution for outdoor environments.
Operational Impact
Case Study missing?
Start adding your own!
Register with your work email and create a new case study profile for your business.
Related Case Studies.
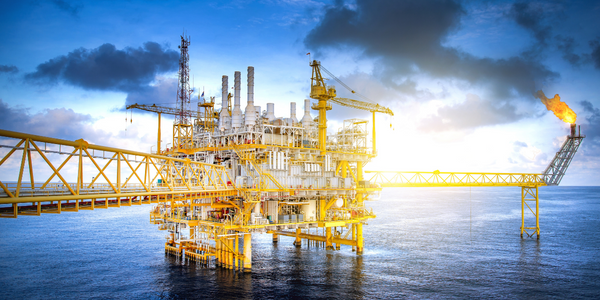
Case Study
Taking Oil and Gas Exploration to the Next Level
DownUnder GeoSolutions (DUG) wanted to increase computing performance by 5 to 10 times to improve seismic processing. The solution must build on current architecture software investments without sacrificing existing software and scale computing without scaling IT infrastructure costs.
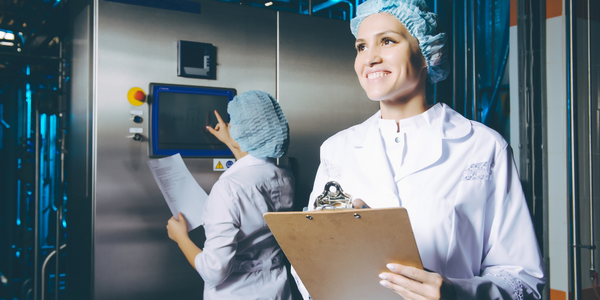
Case Study
Remote Wellhead Monitoring
Each wellhead was equipped with various sensors and meters that needed to be monitored and controlled from a central HMI, often miles away from the assets in the field. Redundant solar and wind generators were installed at each wellhead to support the electrical needs of the pumpstations, temperature meters, cameras, and cellular modules. In addition to asset management and remote control capabilities, data logging for remote surveillance and alarm notifications was a key demand from the customer. Terra Ferma’s solution needed to be power efficient, reliable, and capable of supporting high-bandwidth data-feeds. They needed a multi-link cellular connection to a central server that sustained reliable and redundant monitoring and control of flow meters, temperature sensors, power supply, and event-logging; including video and image files. This open-standard network needed to interface with the existing SCADA and proprietary network management software.
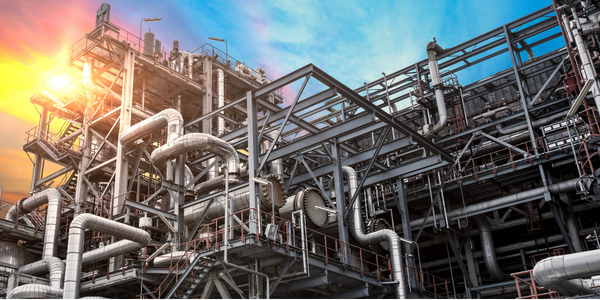
Case Study
Refinery Saves Over $700,000 with Smart Wireless
One of the largest petroleum refineries in the world is equipped to refine various types of crude oil and manufacture various grades of fuel from motor gasoline to Aviation Turbine Fuel. Due to wear and tear, eight hydrogen valves in each refinery were leaking, and each cost $1800 per ton of hydrogen vented. The plant also had leakage on nearly 30 flare control hydrocarbon valves. The refinery wanted a continuous, online monitoring system that could catch leaks early, minimize hydrogen and hydrocarbon production losses, and improve safety for maintenance.