Applicable Industries
- Automotive
- Life Sciences
Applicable Functions
- Product Research & Development
Use Cases
- Manufacturing Process Simulation
- Structural Health Monitoring
Services
- System Integration
About The Customer
Tallent Automotive Ltd is a world-class designer, developer, and manufacturer of innovative chassis structural and suspension systems. The company has a global reputation for its high-quality products and supplies to some of the biggest names in the automobile industry, including BMW, Ford, General Motors, Honda, Jaguar, Land Rover, Nissan, Porsche, Renault, Saab, and Volkswagen. As the automotive industry evolves, Tallent Automotive is constantly seeking ways to innovate and improve its products to meet the growing demands for lightweight, fuel-efficient vehicles.
The Challenge
Tallent Automotive Ltd, a leading designer, developer, and manufacturer of innovative chassis structural and suspension systems, faced a significant challenge. The company supplies to major automobile manufacturers like BMW, Ford, General Motors, Honda, Jaguar, Land Rover, Nissan, Porsche, Renault, Saab, and Volkswagen. With the growing demand for lightweight, fuel-efficient vehicles, Tallent Automotive needed a more automated method to produce minimum mass sheet metal chassis components. The new method had to consider performance targets and manufacturing constraints. The traditional design process of CAD followed by CAE verification was not efficient enough to meet these demands.
The Solution
To overcome this challenge, Tallent Automotive collaborated with Altair ProductDesign’s process automation team to develop the ‘eDICT’ (evolutionary design in chassis technology) system. This system is a blend of custom design tools and a tailored interface for the optimization technology in the HyperWorks simulation suite. The eDICT system guides Tallent Automotive engineers through several stages of best practice development, tracking the efficiency of the design and highlighting the factors adding mass into the solution. The process starts by generating and analyzing the optimum material layout, known as the ‘skeleton’. eDICT then guides the user through interpretation of this idealized structural layout to manufacturable sheet metal solutions. The automated process continually tracks the efficiency of the solution and supports re-optimization to ensure the structural performance remains inside the predefined targets.
Operational Impact
Quantitative Benefit
Case Study missing?
Start adding your own!
Register with your work email and create a new case study profile for your business.
Related Case Studies.
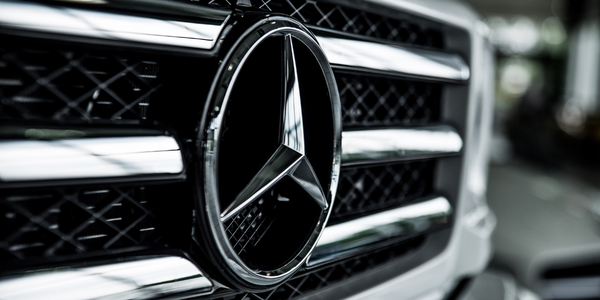
Case Study
Integral Plant Maintenance
Mercedes-Benz and his partner GAZ chose Siemens to be its maintenance partner at a new engine plant in Yaroslavl, Russia. The new plant offers a capacity to manufacture diesel engines for the Russian market, for locally produced Sprinter Classic. In addition to engines for the local market, the Yaroslavl plant will also produce spare parts. Mercedes-Benz Russia and his partner needed a service partner in order to ensure the operation of these lines in a maintenance partnership arrangement. The challenges included coordinating the entire maintenance management operation, in particular inspections, corrective and predictive maintenance activities, and the optimizing spare parts management. Siemens developed a customized maintenance solution that includes all electronic and mechanical maintenance activities (Integral Plant Maintenance).

Case Study
Monitoring of Pressure Pumps in Automotive Industry
A large German/American producer of auto parts uses high-pressure pumps to deburr machined parts as a part of its production and quality check process. They decided to monitor these pumps to make sure they work properly and that they can see any indications leading to a potential failure before it affects their process.