Technology Category
- Analytics & Modeling - Digital Twin / Simulation
- Robots - Autonomous Guided Vehicles (AGV)
Applicable Industries
- Automotive
- Specialty Vehicles
Applicable Functions
- Product Research & Development
Use Cases
- Digital Twin
- Virtual Reality
About The Customer
Accuride Corporation is a global leader in the supply and manufacture of commercial and passenger vehicle components. Their product range includes steel and aluminum vehicle wheels and wheel-end components, and assemblies for the European automotive and global agricultural, construction, and industrial equipment markets. With its headquarters in Livonia, Michigan, Accuride has facilities across North America, Europe, and Asia. The company leverages over 125 years of experience and advanced engineering analysis methods to create efficient designs and deliver value to its customers. Accuride has been focusing on implementing company-wide virtual product development methods to democratize the product development process.
The Challenge
Accuride Corporation, a leading global commercial and passenger vehicle component supplier, faced a significant challenge in their product development process. The creation of a solid hexahedral mesh, a crucial step in developing truck and passenger wheels, was a complex and time-consuming task. This process required an in-depth understanding of advanced meshing techniques and component quality standards. Moreover, the task was so specialized that only a few engineers at Accuride could handle it, leading to potential delays in time-critical projects. The company also struggled to share this meshing knowledge beyond department boundaries, making it difficult to include everyone in the process, especially simulation beginners.
The Solution
To address this challenge, Accuride collaborated with Altair to develop an automated solution that significantly reduced the time spent on preparing surfaces and elements, thereby easing the overall development efforts. They utilized the model build and assembly tools of Altair® HyperWorks®, an AI-driven simulation solution, to develop a process that enabled engineers to manage multiple configurations, mesh variants, and part instances independently of finite element (FE) specialists. The HyperWorks solution automated the Hexa-Mesh creation of truck and passenger car wheels based on user inputs like element size, the density of the solid mesh, and more, through a customized graphical user interface (GUI). This solution allowed the Accuride team to run a complete analysis and deliver reliable results in a much shorter timeframe.
Operational Impact
Quantitative Benefit
Case Study missing?
Start adding your own!
Register with your work email and create a new case study profile for your business.
Related Case Studies.
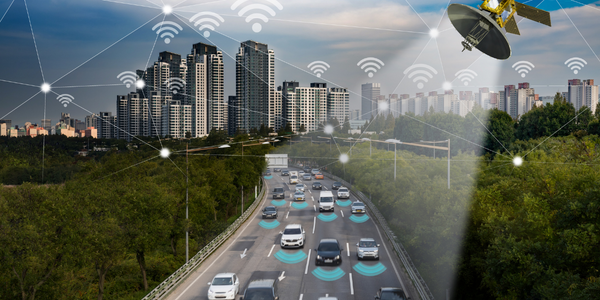
Case Study
Transformation for IoT Business Model in Connected Industrial Vehicles
CNH Industrial wanted to put IoT-enabled viechles onto the market. Whether monitoring a single machine or integrating an entire fleet, operators are able to track the status, speed, and movement of machines and their performance and also receive alerts on issues that may require service by a qualified technician to improve uptime and overall effectiveness of the vehicle.
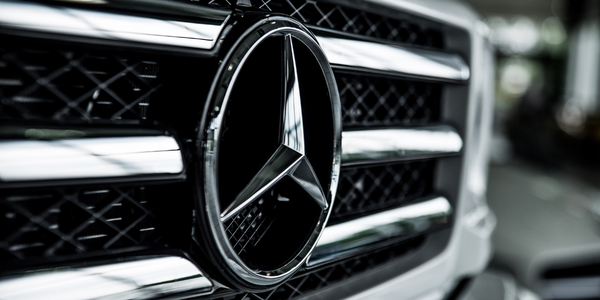
Case Study
Integral Plant Maintenance
Mercedes-Benz and his partner GAZ chose Siemens to be its maintenance partner at a new engine plant in Yaroslavl, Russia. The new plant offers a capacity to manufacture diesel engines for the Russian market, for locally produced Sprinter Classic. In addition to engines for the local market, the Yaroslavl plant will also produce spare parts. Mercedes-Benz Russia and his partner needed a service partner in order to ensure the operation of these lines in a maintenance partnership arrangement. The challenges included coordinating the entire maintenance management operation, in particular inspections, corrective and predictive maintenance activities, and the optimizing spare parts management. Siemens developed a customized maintenance solution that includes all electronic and mechanical maintenance activities (Integral Plant Maintenance).