Technology Category
- Sensors - Air Pollution Sensors
- Sensors - Environmental Sensors
Applicable Industries
- Aerospace
- Electronics
Applicable Functions
- Procurement
- Product Research & Development
Use Cases
- Vehicle Performance Monitoring
- Virtual Prototyping & Product Testing
Services
- System Integration
- Testing & Certification
About The Customer
The customer in this case is the United States Marine Corps, a branch of the United States Armed Forces responsible for providing power projection, using the mobility of the U.S. Navy to rapidly deliver combined-arms task forces. The Marines are known for taking on the military’s most difficult and daring assignments and rely heavily on advanced technology to safeguard its troops in brutal environments. They were in the process of rolling out a new Expeditionary Fighting Vehicle (EFV), a hybrid tank/boat designed to carry 20 personnel over both land and sea at high speeds. The EFV was more heavily armed and armored, yet faster and more maneuverable than its predecessor, and was set to be the Marines’ primary combat vehicle.
The Challenge
The United States Marine Corps was set to roll out a new Expeditionary Fighting Vehicle (EFV) by the end of the decade. This hybrid tank/boat was designed to carry 20 personnel over both land and sea at speeds of up to 30 miles an hour. However, the EFV contained an environmental control system (ECS) that was not up to the mark. The ECS, essentially a high-performance air conditioner, was supposed to keep the cabin air at a comfortable temperature even when outside temperatures were as high as 125º Fahrenheit, while operating quietly enough to pose no risk to the crew’s hearing. The initial prototype failed to meet these standards, leading to a re-bid process. Fairchild Controls Corporation won the re-bid and was tasked with improving the ECS unit’s airflow and minimizing operational noise, all within a strict budget and a tight deadline of 14 months.
The Solution
Fairchild Controls decided to replace the original model’s fast but loud vane axial fan with a slower, mixed flow fan with both rotating and stationary elements. To design the fan, the company used CFX software from ANSYS, Inc., a powerful solution for modeling fluid dynamics. The software allowed the engineers to create and analyze 3-D models of candidate fan designs, compare various combinations of blade shape, number, and height, and select a design that met all performance objectives. The software also allowed the team to simulate performance and explore what-if scenarios under a wide range of simulated operating conditions. Over the next three months, Fairchild Controls constructed a working prototype, imported the selected design’s geometry into its CAD system, coded its computer-automated machining tool directly from the solid, and assembled the working prototype.
Operational Impact
Quantitative Benefit
Case Study missing?
Start adding your own!
Register with your work email and create a new case study profile for your business.
Related Case Studies.
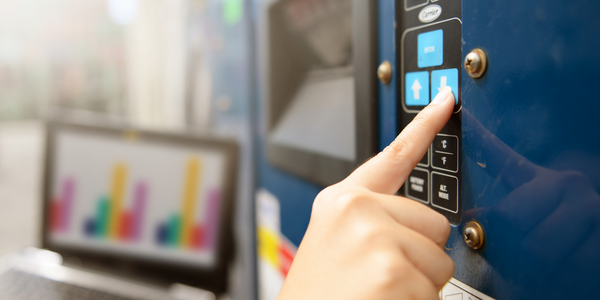
Case Study
Remote Temperature Monitoring of Perishable Goods Saves Money
RMONI was facing temperature monitoring challenges in a cold chain business. A cold chain must be established and maintained to ensure goods have been properly refrigerated during every step of the process, making temperature monitoring a critical business function. Manual registration practice can be very costly, labor intensive and prone to mistakes.
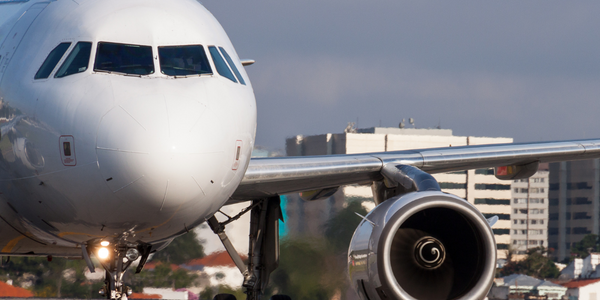
Case Study
Airbus Soars with Wearable Technology
Building an Airbus aircraft involves complex manufacturing processes consisting of thousands of moving parts. Speed and accuracy are critical to business and competitive advantage. Improvements in both would have high impact on Airbus’ bottom line. Airbus wanted to help operators reduce the complexity of assembling cabin seats and decrease the time required to complete this task.
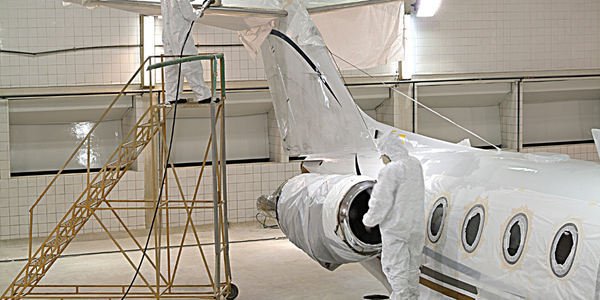
Case Study
Aircraft Predictive Maintenance and Workflow Optimization
First, aircraft manufacturer have trouble monitoring the health of aircraft systems with health prognostics and deliver predictive maintenance insights. Second, aircraft manufacturer wants a solution that can provide an in-context advisory and align job assignments to match technician experience and expertise.
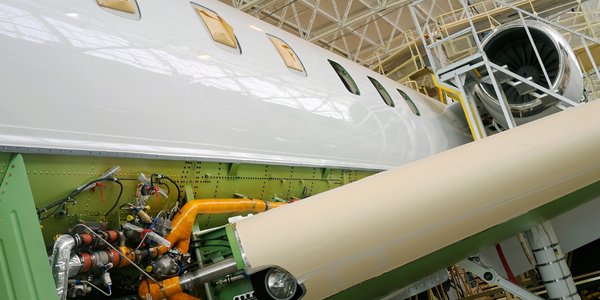
Case Study
Aerospace & Defense Case Study Airbus
For the development of its new wide-body aircraft, Airbus needed to ensure quality and consistency across all internal and external stakeholders. Airbus had many challenges including a very aggressive development schedule and the need to ramp up production quickly to satisfy their delivery commitments. The lack of communication extended design time and introduced errors that drove up costs.