Customer Company Size
Large Corporate
Region
- Pacific
Country
- Australia
Product
- EcoStruxure
- M580 ePAC
- Altivar VSDs
- Citect SCADA system
Tech Stack
- IoT
- Automation
- Connectivity
- Software
Implementation Scale
- Enterprise-wide Deployment
Impact Metrics
- Cost Savings
- Environmental Impact Reduction
- Energy Saving
Technology Category
- Platform as a Service (PaaS) - Connectivity Platforms
- Application Infrastructure & Middleware - Data Exchange & Integration
Applicable Industries
- Transportation
Applicable Functions
- Facility Management
- Maintenance
Use Cases
- Energy Management System
- Predictive Maintenance
- Public Transportation Management
Services
- System Integration
- Cloud Planning, Design & Implementation Services
About The Customer
EastLink is a freeway network located east of Melbourne in Victoria’s greenbelt. The 40 kilometre road network is the largest privately operated freeway network in Victoria, and is a leader in transport sustainability. EastLink has the lowest toll prices in Australia, 480 hectares of landscaping, 4 million native trees, shrubs and plants, more than 60 wetlands that treat road surface rainwater run-off before it is released to local waterways, and the EastLink Trail – 35 kilometres of shared use path, distinctive public architecture and public artworks. Defining features of the freeway are the twin 1.6 km tunnels which protect the environmentally sensitive Mullum Mullum Valley above. The tunnels are each three lanes wide and reach a maximum depth of 53 metres underground. Up to 115,000 vehicles drive through the EastLink tunnels in a single day.
The Challenge
The EastLink freeway tunnels in Melbourne, Victoria, run beneath the environmentally sensitive Mullum Mullum Valley, requiring special attention to ventilation of vehicle emissions. The original tunnel ventilation system, commissioned when EastLink opened ten years ago, was designed to expel 100% of tunnel air, including pollutants from vehicles’ combustion engines, through two 45-metre high ventilation stacks. The ventilation system has 24 smaller jet fans which are located within the tunnels to control air flow direction, minimising a piston effect caused by traffic movement in the tunnel, and ten axial larger, 275kW, 690vAC, ventilation fans in the ventilation stacks to draw air up from the tunnels for expulsion at the stack tops. Since the opening of EastLink, the speed of airflows within the tunnels and stacks was controlled in a traditional way - by switching individual fans on and off at pre-programmed times of the day. When switched on, a fan always operated at full speed. This was inefficient, using more electricity than necessary and producing high operating noise levels. It was also causing unnecessary wear and tear on components.
The Solution
Schneider Electric worked with EastLink to upgrade the ten large ventilation fans from fixed speed fully off / fully on operation to a much more efficient self-regulating or closed loop variable speed operation. Schneider Electric’s EcoStruxure platform has been used in the solution to bring together automation, connectivity and software for real time control and visibility. The middle layer of the EcoStruxure solution is a Citect SCADA control system. This provides an interface so EastLink can see how the ventilation system is running, at any time, from anywhere. This allows them to monitor and maintain systems and to see exactly where energy savings are being made. Two pairs of Hot Standby Schneider Electric M580 ePAC (Ethernet Programmable Automation Controller) have been installed, one pair in each tunnel, to create the new closed-loop system with a ATV61 690vAC variable speed drive (VSD) with Active Front End (AFE) harmonic mitigation installed on each of the 10 axial fans. The ePACs use real-time data from air quality and air f low sensors to dynamically control the speed and number of axial and jet fans that are required to meet traffic demand. Every few seconds, the updated control system adjusts the VSD on each operating fan to ensure fan operation is fine-tuned according to conditions.
Operational Impact
Quantitative Benefit
Case Study missing?
Start adding your own!
Register with your work email and create a new case study profile for your business.
Related Case Studies.
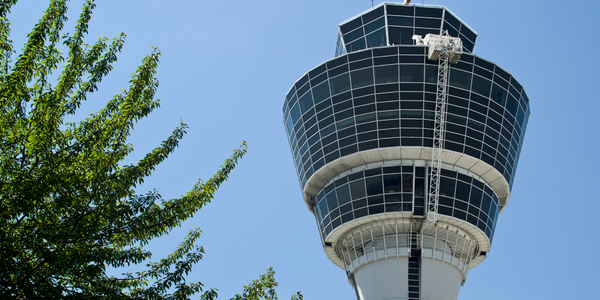
Case Study
Airport SCADA Systems Improve Service Levels
Modern airports are one of the busiest environments on Earth and rely on process automation equipment to ensure service operators achieve their KPIs. Increasingly airport SCADA systems are being used to control all aspects of the operation and associated facilities. This is because unplanned system downtime can cost dearly, both in terms of reduced revenues and the associated loss of customer satisfaction due to inevitable travel inconvenience and disruption.
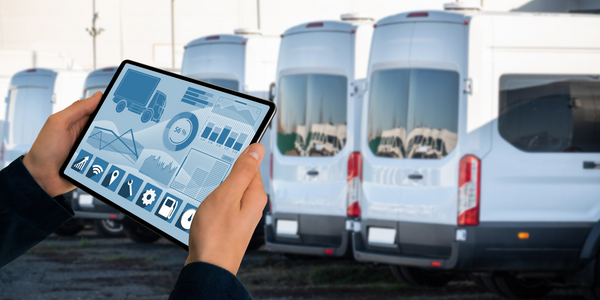
Case Study
IoT-based Fleet Intelligence Innovation
Speed to market is precious for DRVR, a rapidly growing start-up company. With a business model dependent on reliable mobile data, managers were spending their lives trying to negotiate data roaming deals with mobile network operators in different countries. And, even then, service quality was a constant concern.
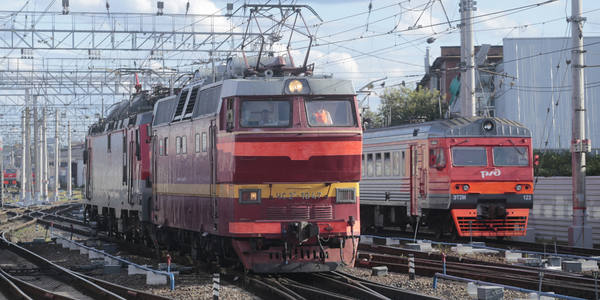
Case Study
Digitize Railway with Deutsche Bahn
To reduce maintenance costs and delay-causing failures for Deutsche Bahn. They need manual measurements by a position measurement system based on custom-made MEMS sensor clusters, which allow autonomous and continuous monitoring with wireless data transmission and long battery. They were looking for data pre-processing solution in the sensor and machine learning algorithms in the cloud so as to detect critical wear.
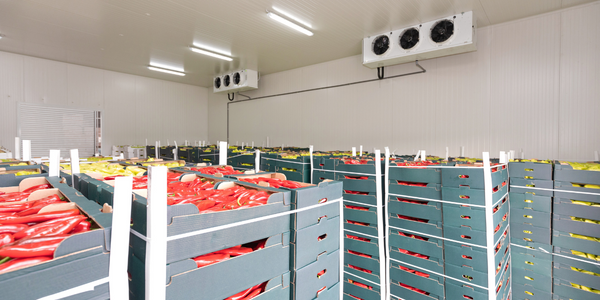
Case Study
Cold Chain Transportation and Refrigerated Fleet Management System
1) Create a digital connected transportation solution to retrofit cold chain trailers with real-time tracking and controls. 2) Prevent multi-million dollar losses due to theft or spoilage. 3) Deliver a digital chain-of-custody solution for door to door load monitoring and security. 4) Provide a trusted multi-fleet solution in a single application with granular data and access controls.
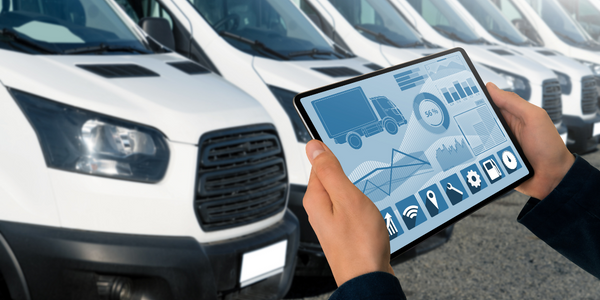
Case Study
Vehicle Fleet Analytics
Organizations frequently implement a maintenance strategy for their fleets of vehicles using a combination of time and usage based maintenance schedules. While effective as a whole, time and usage based schedules do not take into account driving patterns, environmental factors, and sensors currently deployed within the vehicle measuring crank voltage, ignition voltage, and acceleration, all of which have a significant influence on the overall health of the vehicle.In a typical fleet, a large percentage of road calls are related to electrical failure, with battery failure being a common cause. Battery failures result in unmet service agreement levels and costly re-adjustment of scheduled to provide replacement vehicles. To reduce the impact of unplanned maintenance, the transportation logistics company was interested in a trial of C3 Vehicle Fleet Analytics.
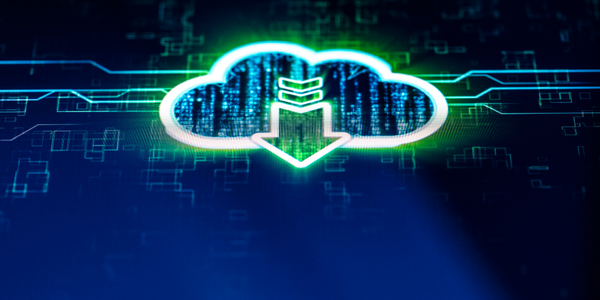
Case Study
3M Gains Real-Time Insight with Cloud Solution
The company has a long track record of innovative technology solutions. For example, 3M helps its customers optimize parking operations by automating fee collection and other processes. To improve support for this rapidly expanding segment, 3M needed to automate its own data collection and reporting. The company had recently purchased the assets of parking, tolling, and automatic license plate reader businesses, and required better insight into these acquisitions. Chad Reed, Global Business Manager for 3M Parking Systems, says, “With thousands of installations across the world, we couldn’t keep track of our software and hardware deployments, which made it difficult to understand our market penetration.” 3M wanted a tracking application that sales staff could use to get real-time information about the type and location of 3M products in parking lots and garages. So that it could be used on-site with potential customers, the solution would have to provide access to data anytime, anywhere, and from an array of mobile devices. Jason Fox, Mobile Application Architect at 3M, upped the ante by volunteering to deliver the new app in one weekend. For Fox and his team, these requirements meant turning to the cloud instead of an on-premises datacenter. “My first thought was to go directly to the cloud because we needed to provide access not only to our salespeople, but to resellers who didn’t have access to our internal network,” says Fox. “The cloud just seemed like a logical choice.”