Driving Innovation in Collegiate Racing: A Case Study on Michigan Baja Racing and Altair HyperWorks™ Suite
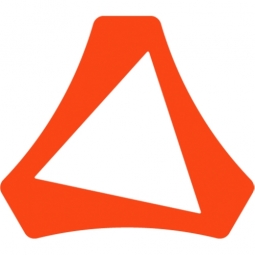
Technology Category
- Robots - Autonomous Guided Vehicles (AGV)
- Sensors - Autonomous Driving Sensors
Applicable Industries
- Automotive
Applicable Functions
- Product Research & Development
Use Cases
- Smart Parking
- Vehicle Performance Monitoring
Services
- Testing & Certification
About The Customer
Michigan Baja Racing (MBR) is a collegiate race team that competes in the North American Baja SAE intercollegiate competition. Each year, the team designs, builds, and tests a new single-seater off-road race car from scratch to compete against hundreds of other teams across the United States. The competition consists of a design presentation and other static events, as well as dynamic events including acceleration, maneuverability, hill climb, suspension and traction (S&T), and a four-hour endurance race. The team is tasked with finding innovative solutions to design challenges within a tight six-month timeline.
The Challenge
Michigan Baja Racing (MBR), a collegiate race team participating in the North American Baja SAE intercollegiate competition, faced a significant challenge in designing a competitive off-road race car. The team had to create a vehicle that was light and nimble enough for acceleration, maneuverability, and hill climb events, but also durable enough to withstand the suspension and traction (S&T) and endurance race. The design process required innovative solutions to reduce mass while maintaining strength, ensuring the vehicle could travel as fast as possible for as long as possible. Adding to the complexity of the challenge, the team had a tight six-month timeline from rulebook to manufactured vehicle, leaving little room for prototyping and testing and no room for critical design mistakes.
The Solution
To overcome these challenges, MBR leveraged the Altair HyperWorks™ suite. Altair HyperMesh™ was used as the default preprocessor, with support from Altair HyperCrash™ to set up crash scenarios, and Altair HyperView™ was used to view the results. Linear static analysis via Altair OptiStruct™ was run on every component as a baseline for stress and stiffness calculations. Loads were collected from strain gauge testing, predicted g-loading, and comparisons with prior year designs. Nonlinear quasi-static analysis from OptiStruct was used in suspension link design to derive reactionary forces from forced displacement. This allowed MBR to predict the forces at the link yields, plastically deforms, fractures, and the failure location. Full vehicle dynamic crash simulation via Altair Radioss™ was run on the computing cluster at the University of Michigan to evaluate the current crashworthiness of the car in a frontal, side-impact, and roll-over situation. Preliminary drag calculations of the roll cage were calculated with Altair AcuSolve™, driving the design towards a more aerodynamic shape rather than a lightweight one.
Operational Impact
Quantitative Benefit
Case Study missing?
Start adding your own!
Register with your work email and create a new case study profile for your business.
Related Case Studies.
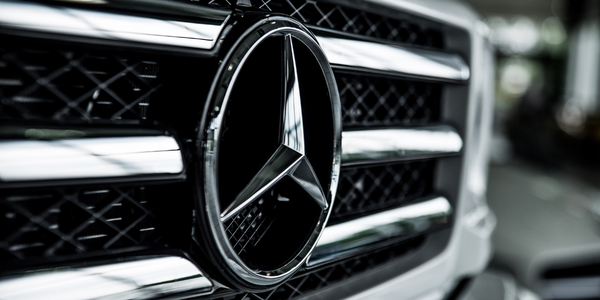
Case Study
Integral Plant Maintenance
Mercedes-Benz and his partner GAZ chose Siemens to be its maintenance partner at a new engine plant in Yaroslavl, Russia. The new plant offers a capacity to manufacture diesel engines for the Russian market, for locally produced Sprinter Classic. In addition to engines for the local market, the Yaroslavl plant will also produce spare parts. Mercedes-Benz Russia and his partner needed a service partner in order to ensure the operation of these lines in a maintenance partnership arrangement. The challenges included coordinating the entire maintenance management operation, in particular inspections, corrective and predictive maintenance activities, and the optimizing spare parts management. Siemens developed a customized maintenance solution that includes all electronic and mechanical maintenance activities (Integral Plant Maintenance).

Case Study
Monitoring of Pressure Pumps in Automotive Industry
A large German/American producer of auto parts uses high-pressure pumps to deburr machined parts as a part of its production and quality check process. They decided to monitor these pumps to make sure they work properly and that they can see any indications leading to a potential failure before it affects their process.