Technology Category
- Analytics & Modeling - Digital Twin / Simulation
- Sensors - Electrical Conductivity Sensors
Applicable Industries
- Automotive
- Transportation
Applicable Functions
- Product Research & Development
Use Cases
- Transportation Simulation
- Virtual Prototyping & Product Testing
About The Customer
EVR Motors Ltd. is a new player in the e-mobility industry. Based in Israel, the company designs and develops cost-effective radial flux Permanent Magnet (PM) electric machines for a range of power conversion applications such as renewable energies and vehicle electrification. Established in 2012, EVR initially developed patents for wind turbine generators. However, they adjusted their roadmap when public taste favored e-mobility, and then developed an innovative electric motor called TS – RFPM (Trapezoidal Stator Radial Flux Motor) based on new, patented technology that provides superior power and torque density – all at lower production costs.
The Challenge
The shift towards e-mobility has put immense pressure on the automotive industry to develop more sustainable and affordable transportation solutions. This has led to a rush to electrify products and compete with e-vehicles that match the performance of internal combustion engine models. EVR Motors Ltd., an Israel-based company that designs and develops cost-effective radial flux Permanent Magnet (PM) electric machines, faced a unique challenge. For several decades, motors for electric vehicles have been optimized using the same topology, called Radial Flux Permanent Magnet Motor topology (RFPM). However, EVR chose to take a different approach. Instead of optimizing existing technology, they decided to invent a new topology and develop a completely new type of motor for the electric vehicle industry called the Trapezoid Stator RFPM topology. As the base of EVR topology is different from other well-known motor topologies, the use of multiphysics and optimization tools was highly important. Therefore, the team needed a reliable, robust simulation tool.
The Solution
In their quest for a powerful and accurate electromagnetic and mechanical simulation tool, EVR Motors chose Altair® FluxMotor®, Altair® Flux®, Altair® SimLab®, and Altair® HyperMesh®. These tools are part of Altair’s complete solution for electric motor design and were used to simulate their motors before prototyping. Motor development involves numerous design iterations to meet all electromagnetic and NVH requirements. EVR used the Altair tools, particularly the highly flexible Flux software, to improve the simulations so they became more accurate and delivered results close to the real prototypes they were building physically. Today, EVR has achieved a simulation accuracy of about 90%, but they’re aiming to improve this to even higher accuracy of 95-96%. Despite their electromagnetic design being brand new and very different than everything that exists today, Altair’s solutions helped EVR meet this challenge and minimized the number of prototypes while meeting all requirements and saving time.
Operational Impact
Quantitative Benefit
Case Study missing?
Start adding your own!
Register with your work email and create a new case study profile for your business.
Related Case Studies.
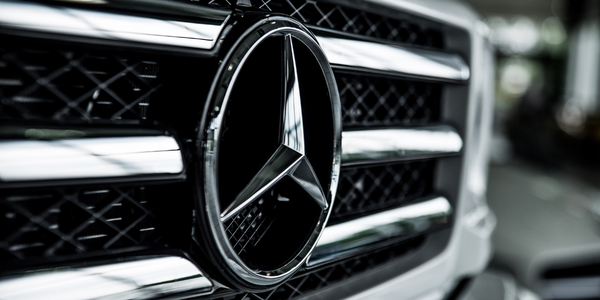
Case Study
Integral Plant Maintenance
Mercedes-Benz and his partner GAZ chose Siemens to be its maintenance partner at a new engine plant in Yaroslavl, Russia. The new plant offers a capacity to manufacture diesel engines for the Russian market, for locally produced Sprinter Classic. In addition to engines for the local market, the Yaroslavl plant will also produce spare parts. Mercedes-Benz Russia and his partner needed a service partner in order to ensure the operation of these lines in a maintenance partnership arrangement. The challenges included coordinating the entire maintenance management operation, in particular inspections, corrective and predictive maintenance activities, and the optimizing spare parts management. Siemens developed a customized maintenance solution that includes all electronic and mechanical maintenance activities (Integral Plant Maintenance).
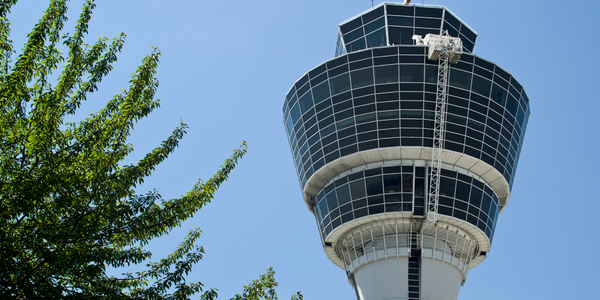
Case Study
Airport SCADA Systems Improve Service Levels
Modern airports are one of the busiest environments on Earth and rely on process automation equipment to ensure service operators achieve their KPIs. Increasingly airport SCADA systems are being used to control all aspects of the operation and associated facilities. This is because unplanned system downtime can cost dearly, both in terms of reduced revenues and the associated loss of customer satisfaction due to inevitable travel inconvenience and disruption.
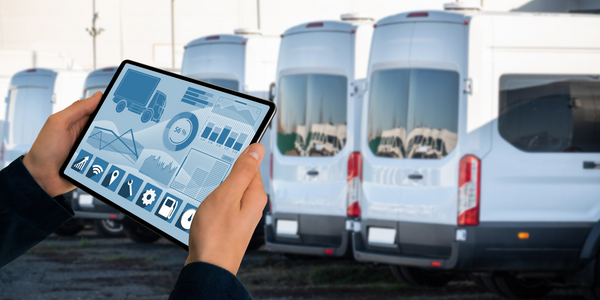
Case Study
IoT-based Fleet Intelligence Innovation
Speed to market is precious for DRVR, a rapidly growing start-up company. With a business model dependent on reliable mobile data, managers were spending their lives trying to negotiate data roaming deals with mobile network operators in different countries. And, even then, service quality was a constant concern.
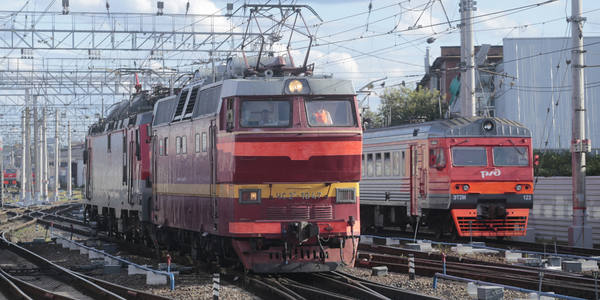
Case Study
Digitize Railway with Deutsche Bahn
To reduce maintenance costs and delay-causing failures for Deutsche Bahn. They need manual measurements by a position measurement system based on custom-made MEMS sensor clusters, which allow autonomous and continuous monitoring with wireless data transmission and long battery. They were looking for data pre-processing solution in the sensor and machine learning algorithms in the cloud so as to detect critical wear.