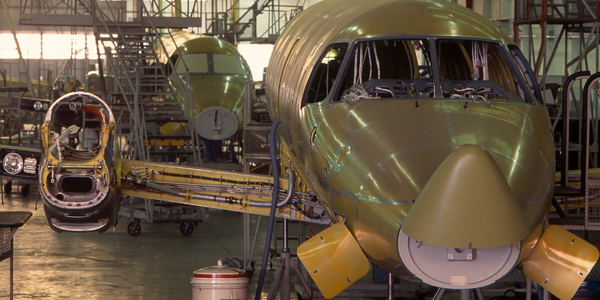
Technology Category
- Functional Applications - Computerized Maintenance Management Systems (CMMS)
- Functional Applications - Enterprise Asset Management Systems (EAM)
Applicable Industries
- Aerospace
- Construction & Infrastructure
Applicable Functions
- Maintenance
- Quality Assurance
Use Cases
- Asset Health Management (AHM)
- Asset Lifecycle Management
Services
- System Integration
- Testing & Certification
The Customer
Dubai Aerospace Enterprise (DAE)
About The Customer
Dubai Aerospace Enterprise (DAE) is a global aviation corporation specializing in aircraft leasing and engineering services. It leases its $16B USD fleet of 425 advanced Boeing, ATR, and Airbus aircraft to more than 108 operators in 52 countries. DAE is committed to driving efficiency throughout the asset lifecycle and reducing its carbon footprint through a comprehensive decommissioning strategy for older aircraft. The company also places a high emphasis on operational efficiency and waste reduction as part of its environmental strategy.
The Challenge
Dubai Aerospace Enterprise (DAE) was faced with the challenge of managing over 2 million records related to its $16B USD fleet of 425 advanced Boeing, ATR, and Airbus aircraft leased to more than 108 operators in 52 countries. The sheer volume of maintenance documentation, compliance, inspection audits, and lease transfers with airline customers was overwhelming. The data was siloed across multiple systems or locations, creating bottlenecks and inefficiencies, which impacted the delivery of information to customers. DAE had digitized part of its information, but the platform was outdated and discontinued in terms of future development and support. This meant more time and effort required to respond to customers with accurate information. Additionally, the security of hundreds of thousands of paper records was at risk in the event of a disaster such as a flood or fire.
The Solution
DAE selected GE Digital’s Asset Transfer System (ATS) to manage its records and project management requirements. The ATS software, part of GE Digital's Asset Records portfolio, is designed to digitize, index, and archive aircraft maintenance records with a cloud-based solution. This system supports the latest international regulatory standards for transmitting documents between lessors and operators. It provides users with quick, efficient access to documents spanning many years. The fully integrated Records and Project Management modules allow for digital auditing, storage, and document search during the lease period while optimizing the exchange and review of asset records at the end of the lease period. Powered by Microsoft Azure, it operates with minimal additional IT infrastructure, allowing organizations to connect through secure web-based access.
Operational Impact
Quantitative Benefit
Case Study missing?
Start adding your own!
Register with your work email and create a new case study profile for your business.
Related Case Studies.
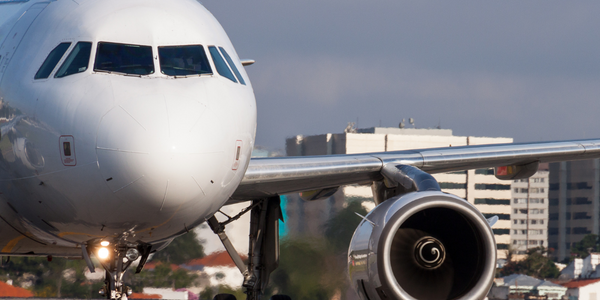
Case Study
Airbus Soars with Wearable Technology
Building an Airbus aircraft involves complex manufacturing processes consisting of thousands of moving parts. Speed and accuracy are critical to business and competitive advantage. Improvements in both would have high impact on Airbus’ bottom line. Airbus wanted to help operators reduce the complexity of assembling cabin seats and decrease the time required to complete this task.
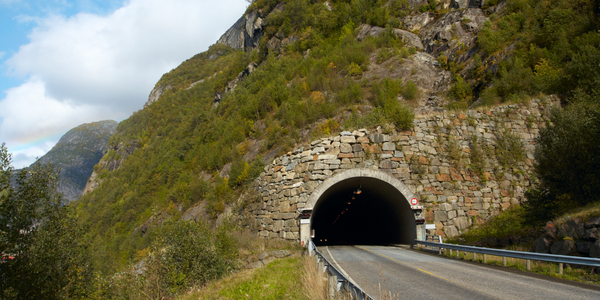
Case Study
IoT System for Tunnel Construction
The Zenitaka Corporation ('Zenitaka') has two major business areas: its architectural business focuses on structures such as government buildings, office buildings, and commercial facilities, while its civil engineering business is targeted at structures such as tunnels, bridges and dams. Within these areas, there presented two issues that have always persisted in regard to the construction of mountain tunnels. These issues are 'improving safety" and "reducing energy consumption". Mountain tunnels construction requires a massive amount of electricity. This is because there are many kinds of electrical equipment being used day and night, including construction machinery, construction lighting, and ventilating fan. Despite this, the amount of power consumption is generally not tightly managed. In many cases, the exact amount of power consumption is only ascertained when the bill from the power company becomes available. Sometimes, corporations install demand-monitoring equipment to help curb the maximum power demanded. However, even in these cases, the devices only allow the total volume of power consumption to be ascertained, or they may issue warnings to prevent the contracted volume of power from being exceeded. In order to tackle the issue of reducing power consumption, it was first necessary to obtain an accurate breakdown of how much power was being used in each particular area. In other words, we needed to be able to visualize the amount of power being consumed. Safety, was also not being managed very rigorously. Even now, tunnel construction sites often use a 'name label' system for managing entry into the work site. Specifically, red labels with white reverse sides that bear the workers' names on both sides are displayed at the tunnel work site entrance. The workers themselves then flip the name label to the appropriate side when entering or exiting from the work site to indicate whether or not they are working inside the tunnel at any given time. If a worker forgets to flip his or her name label when entering or exiting from the tunnel, management cannot be performed effectively. In order to tackle the challenges mentioned above, Zenitaka decided to build a system that could improve the safety of tunnel construction as well as reduce the amount of power consumed. In other words, this new system would facilitate a clear picture of which workers were working in each location at the mountain tunnel construction site, as well as which processes were being carried out at those respective locations at any given time. The system would maintain the safety of all workers while also carefully controlling the electrical equipment to reduce unnecessary power consumption. Having decided on the concept, our next concern was whether there existed any kind of robust hardware that would not break down at the construction work site, that could move freely in response to changes in the working environment, and that could accurately detect workers and vehicles using radio frequency identification (RFID). Given that this system would involve many components that were new to Zenitaka, we decided to enlist the cooperation of E.I.Sol Co., Ltd. ('E.I.Sol') as our joint development partner, as they had provided us with a highly practical proposal.
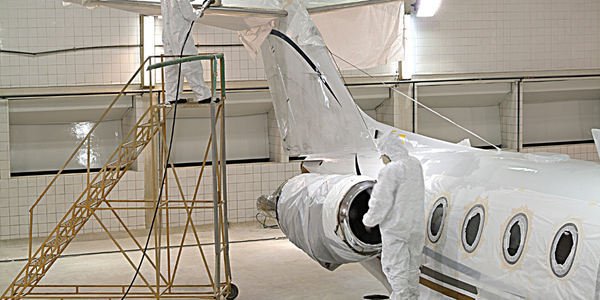
Case Study
Aircraft Predictive Maintenance and Workflow Optimization
First, aircraft manufacturer have trouble monitoring the health of aircraft systems with health prognostics and deliver predictive maintenance insights. Second, aircraft manufacturer wants a solution that can provide an in-context advisory and align job assignments to match technician experience and expertise.
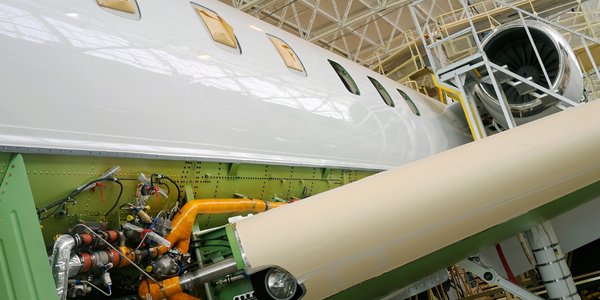
Case Study
Aerospace & Defense Case Study Airbus
For the development of its new wide-body aircraft, Airbus needed to ensure quality and consistency across all internal and external stakeholders. Airbus had many challenges including a very aggressive development schedule and the need to ramp up production quickly to satisfy their delivery commitments. The lack of communication extended design time and introduced errors that drove up costs.
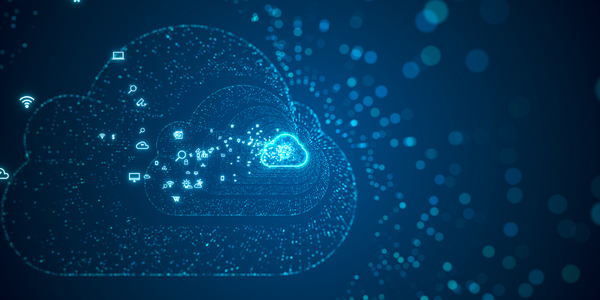
Case Study
Splunk Partnership Ties Together Big Data & IoT Services
Splunk was faced with the need to meet emerging customer demands for interfacing IoT projects to its suite of services. The company required an IoT partner that would be able to easily and quickly integrate with its Splunk Enterprise platform, rather than allocating development resources and time to building out an IoT interface and application platform.