Technology Category
- Analytics & Modeling - Digital Twin / Simulation
- Drones - Fixed-Wing Drones
Applicable Industries
- Aerospace
- Equipment & Machinery
Applicable Functions
- Maintenance
- Product Research & Development
Use Cases
- Manufacturing Process Simulation
- Structural Health Monitoring
Services
- System Integration
- Testing & Certification
About The Customer
Swift Engineering, Inc., based in San Clemente, California, is a product development company with over 30 years of experience designing, developing, and building high-performance advanced composite vehicles, unmanned systems, full-scale demonstrators, build-to-print, and automated robotics. Swift specializes in the design, development, and manufacturing of lightweight composite structures, components, and vehicles. Founded in 1983 as a leading developer of high-performance racecars, Swift has been applying its depth of composite talent to the aerospace and aviation industries since 1997. Swift has emerged as a premier air vehicle designer and manufacturer, as demonstrated through the successful KillerBee Unmanned Aerial Systems (UAS), the Boeing Sikorsky Joint Multi-Role (JMR) Demonstrator, the Eclipse Concept Jet program, and many other similar aerospace and oceanic build-to-print composite manufacturing projects.
The Challenge
Swift Engineering, Inc., a product development company with over 30 years of experience in designing, developing, and building high-performance advanced composite vehicles, unmanned systems, and automated robotics, faced a challenge with their Swift020 Unmanned Aerial System (UAS). The challenge was to define the specification for the maximum weight of the maintenance tooling used on the Swift020 UAS. The concern arose from the fact that the flight surfaces of the UAS were minimum gauge, and heavy tools dropped on the structure could cause irreparable damage, downtime, and expensive component replacement. The objective was to determine the maximum maintenance tool weight that, if dropped from a nominal height of 0.762 meters, would not cause permanent damage to any part of the Swift020 UAS.
The Solution
To solve this challenge, Swift Engineering utilized RADIOSS Explicit Dynamic Impact Simulation. An explicit model of the UAS was generated in HyperMesh® and impacted by a steel penetrator at defined drop energies. A parametric curve of maximum composite compression strain vs. impact energy and limit strain for the impacted composite material was used to yield the specification for the maximum tool weight. A full-scale model of the Swift020 was generated in HyperMesh. The primary structural components comprised of graphite, fiberglass, and Kevlar® epoxy advanced composite materials were modeled using MAT25 material property in RADIOSS. The penetrator was modeled as a 0.0254-meter diameter hemispherical tip rod. Initial velocity (INIVEL) of 3.867 m/s was imposed on the penetrator to simulate a 0.762-meter drop using Conservation of Energy. The impact energy was modulated using the density of the penetrator in the material card.
Operational Impact
Quantitative Benefit
Case Study missing?
Start adding your own!
Register with your work email and create a new case study profile for your business.
Related Case Studies.
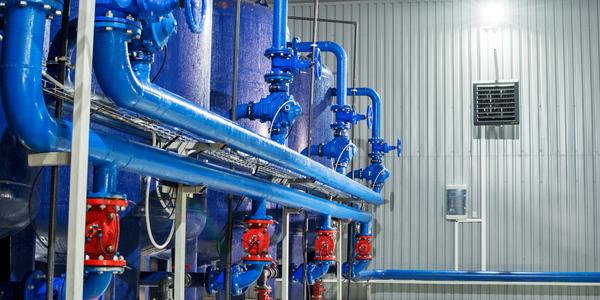
Case Study
Smart Water Filtration Systems
Before working with Ayla Networks, Ozner was already using cloud connectivity to identify and solve water-filtration system malfunctions as well as to monitor filter cartridges for replacements.But, in June 2015, Ozner executives talked with Ayla about how the company might further improve its water systems with IoT technology. They liked what they heard from Ayla, but the executives needed to be sure that Ayla’s Agile IoT Platform provided the security and reliability Ozner required.
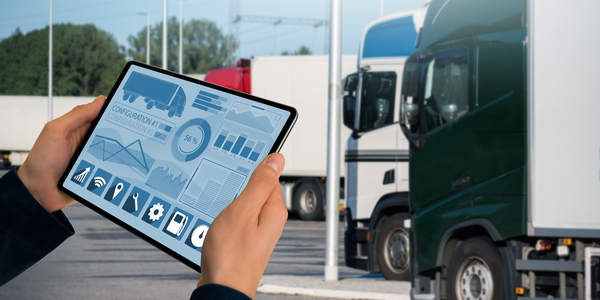
Case Study
IoT enabled Fleet Management with MindSphere
In view of growing competition, Gämmerler had a strong need to remain competitive via process optimization, reliability and gentle handling of printed products, even at highest press speeds. In addition, a digitalization initiative also included developing a key differentiation via data-driven services offers.
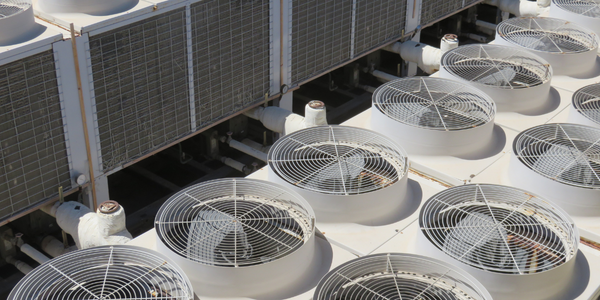
Case Study
Predictive Maintenance for Industrial Chillers
For global leaders in the industrial chiller manufacturing, reliability of the entire production process is of the utmost importance. Chillers are refrigeration systems that produce ice water to provide cooling for a process or industrial application. One of those leaders sought a way to respond to asset performance issues, even before they occur. The intelligence to guarantee maximum reliability of cooling devices is embedded (pre-alarming). A pre-alarming phase means that the cooling device still works, but symptoms may appear, telling manufacturers that a failure is likely to occur in the near future. Chillers who are not internet connected at that moment, provide little insight in this pre-alarming phase.
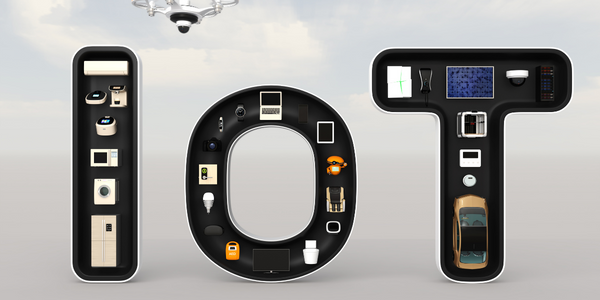
Case Study
Premium Appliance Producer Innovates with Internet of Everything
Sub-Zero faced the largest product launch in the company’s history:It wanted to launch 60 new products as scheduled while simultaneously opening a new “greenfield” production facility, yet still adhering to stringent quality requirements and manage issues from new supply-chain partners. A the same time, it wanted to increase staff productivity time and collaboration while reducing travel and costs.
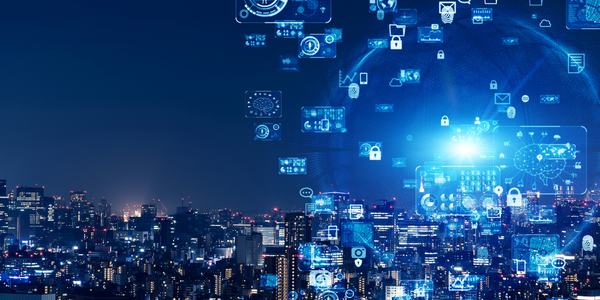
Case Study
Integration of PLC with IoT for Bosch Rexroth
The application arises from the need to monitor and anticipate the problems of one or more machines managed by a PLC. These problems, often resulting from the accumulation over time of small discrepancies, require, when they occur, ex post technical operations maintenance.
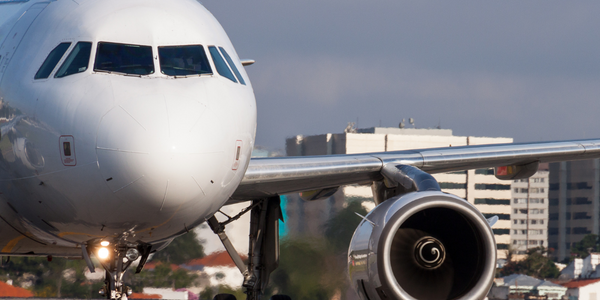
Case Study
Airbus Soars with Wearable Technology
Building an Airbus aircraft involves complex manufacturing processes consisting of thousands of moving parts. Speed and accuracy are critical to business and competitive advantage. Improvements in both would have high impact on Airbus’ bottom line. Airbus wanted to help operators reduce the complexity of assembling cabin seats and decrease the time required to complete this task.