Customer Company Size
Large Corporate
Region
- Asia
Product
- EcoStruxure
- Symmetra PX UPS
- Galaxy UPS
- Pro-face HMIs
- PowerLogic ION7650
Tech Stack
- IoT
- Cloud
- Analytics
- Cybersecurity
- Remote Monitoring
Implementation Scale
- Enterprise-wide Deployment
Impact Metrics
- Cost Savings
- Productivity Improvements
- Energy Saving
Technology Category
- Infrastructure as a Service (IaaS) - Cloud Computing
- Analytics & Modeling - Real Time Analytics
- Cybersecurity & Privacy - Network Security
Applicable Industries
- Electronics
Applicable Functions
- Discrete Manufacturing
- Maintenance
Use Cases
- Predictive Maintenance
- Energy Management System
- Remote Asset Management
Services
- System Integration
- Testing & Certification
About The Customer
Samsung SDI is a creative leader in Korea’s energy and advanced materials sectors. Since its foundation in 1970, it has expanded its business from a Braun tube manufacturer to flat TVs, small cells, medium and large batteries, and it is currently producing secondary batteries for IT, ESS and vehicles, and advanced materials for semiconductors, display and solar energy. With the goal of becoming a global No. 1 brand, the company has realized the vision and technology to further enrich human lives and shape a new future through constant innovation. In particular, Samsung SDI’s first priority is “safety”. Under the motto of ‘safety battery’, it manufactures easy-to-use lithium-ion batteries with no risk of explosion. Through its quality-first business philosophy and continued technology innovation, Samsung SDI has been recognized as one of the leading companies in the global lithium-ion battery industry since 2010. Development of next-generation technology such as the flexible battery which the company released for the first time in the world has positioned it to lead the small battery market. The Samsung SDI’s Cheonan plant using Schneider Electric’s solution has been a workplace of around 3,500 employees since it began manufacture in 1996.
The Challenge
Samsung SDI, a global leader in the energy industry, was facing challenges with its power supply. Due to South Korea's centralized power supply systems and geographical nature, long-distance transmission was inevitable. This led to voltage drops causing factory shutdowns about 3 to 4 times a year. Power outages would suspend the running of manufacturing facilities, which could be critical to supply lines of various hazardous materials such as chemicals. It not only took a considerable amount of time to recover the situation but also interrupted manufacturing. Samsung SDI needed equipment that enables reliable power supply. Another challenge was the need for cost reduction. An input voltage of 154,000 V at a production facility causes an instantaneous voltage drop for 10 ms to 50 ms. Most of the machines that read data within 50 ms cost about tens of millions to tens of billions of dollars. Samsung SDI was in need of a UPS that is flexibly-transformable based on on-site conditions, installable into a limited space, and scalable.
The Solution
Samsung SDI Cheonan factory has about 60 units of uninterruptible power supply (UPS) systems, 4 units of power quality (PQ) meters for power monitoring, 3 units of DC circuit breakers of energy storage system (ESS), and various types of switches of Schneider Electric. In Samsung SDI Cheonan plant, Schneider Electric’s Symmetra PX UPS and Galaxy UPS were installed. In particular, it is the first case where such systems are applied to lithium-ion battery production facility, and the UPS systems have greatly contributed to protecting sensitive manufacturing facility by supplying stable power against external environmental and geographical factors. To record errors for the 154,000 V lines supplied to Samsung SDI Cheonan factory, and monitor power quality below 22,900 V line in real-time, Schneider Electric has installed PQ meters such as PowerLogic ION7650 that keeps the highest accuracy among its energy and power quality meters. In addition, ESS system for Samsung SDI has 3 DC circuit breakers. Most ESS systems use AC circuit breakers, but only limited types are available making an optimized DC circuit breaker rather difficult to be found. However, Samsung SDI was able to effectively apply a DC circuit breaker of the Schneider Electric product portfolio in its facilities.
Operational Impact
Quantitative Benefit
Case Study missing?
Start adding your own!
Register with your work email and create a new case study profile for your business.
Related Case Studies.
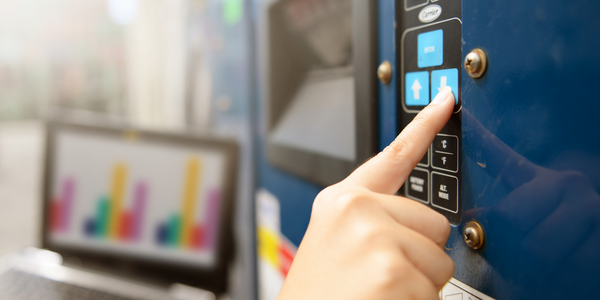
Case Study
Remote Temperature Monitoring of Perishable Goods Saves Money
RMONI was facing temperature monitoring challenges in a cold chain business. A cold chain must be established and maintained to ensure goods have been properly refrigerated during every step of the process, making temperature monitoring a critical business function. Manual registration practice can be very costly, labor intensive and prone to mistakes.
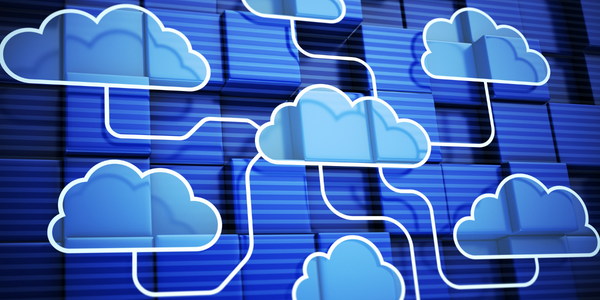
Case Study
Cloud Solution for Energy Management Platform-Schneider Electric
Schneider Electric required a cloud solution for its energy management platform to manage high computational operations, which were essential for catering to client requirements. As the business involves storage and analysis of huge amounts of data, the company also needed a convenient and scalable storage solution to facilitate operations efficiently.
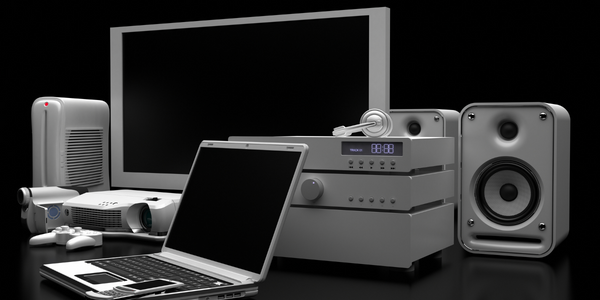
Case Study
Leveraging the IoT to Gain a Competitive Edge in International Competition
Many large manufacturers in and outside Japan are competing for larger market share in the same space, expecting a growing demand for projectors in the areas of entertainment, which requires glamor and strong visual performance as well as digital signage that can attract people’s attention. “It is becoming more and more difficult to differentiate ourselves with stand-alone hardware products,” says Kazuyuki Kitagawa, Director of Service & Support at Panasonic AVC Networks. “In order for Panasonic to grow market share and overall business, it is essential for us to develop solutions that deliver significant added value.” Panasonic believes projection failure and quality deterioration should never happen. This is what and has driven them to make their projectors IoT-enabled. More specifically, Panasonic has developed a system that collects data from projectors, visualizes detailed operational statuses, and predicts issues and address them before failure occurs. Their projectors are embedded with a variety of sensors that measure power supply, voltage, video input/ output signals, intake/exhaust air temperatures, cooling fan operations, and light bulb operating time. These sensors have been used to make the projector more intelligent, automatically suspending operation when the temperature rises excessively, and automatically switching light bulbs. Although this was a great first step, Panasonic projectors were still not equipped with any capability to send the data over a network.