Technology Category
- Application Infrastructure & Middleware - Middleware, SDKs & Libraries
- Functional Applications - Manufacturing Execution Systems (MES)
Applicable Industries
- Automotive
- Chemicals
Applicable Functions
- Product Research & Development
Use Cases
- Predictive Maintenance
- Vehicle Performance Monitoring
Services
- System Integration
About The Customer
The customer in this case study is Michigan Engineering Services, LLC (MES), a research and development company that specializes in developing commercial software and advanced technology for engineering simulations. MES operates in both the defense and commercial industrial sectors. Through its engineering services, MES facilitates an efficient technology transition to its customers. In this particular case, MES was working with automotive companies that needed to control the airborne noise generated within the interior of their vehicles due to various external sources.
The Challenge
Michigan Engineering Services, LLC (MES), a research and development company specializing in commercial software and advanced technology for engineering simulations, was faced with a challenge from automotive companies. These companies needed to control the airborne noise generated within the interior of a vehicle due to external sources such as motors, engines, transmissions, and tires. The goal was to achieve the least amount of noise with minimal penalties in cost and weight. The challenge was that conventional Finite Element Analysis (FEA) methods, used for simulations up to 8KHz to 10KHz (the typical upper frequencies of interest for airborne noise), were either computationally expensive or infeasible due to the small size of finite elements required to model the vehicle at such high frequencies.
The Solution
MES developed a solution using Energy Finite Element Analysis (EFEA). The EFEA requires a smaller number of elements in the model because the new primary variables are based on the energy of the structural vibration and of the acoustic field. The EFEA uses a library of elements (similar to the FEA) for modeling any physical system and a library of joints (similar to the coupling loss factors in Statistical Energy Analysis) for representing the power transfer mechanisms which exist in the system. The EFEA model can be developed using the same tools (i.e., Altair HyperMesh™) and by following a process similar to developing FEA models. Due to the significantly fewer elements required compared to FEA, alternative designs can be evaluated rapidly enough to influence the design.
Operational Impact
Case Study missing?
Start adding your own!
Register with your work email and create a new case study profile for your business.
Related Case Studies.
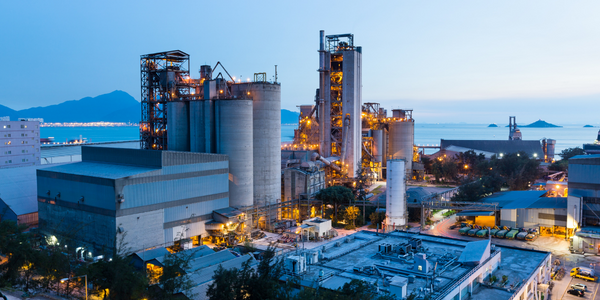
Case Study
Honeywell - Tata Chemicals Improves Data Accessibility with OneWireless
Tata was facing data accessibility challenges in the cement plant control room tapping signals from remote process control areas and other distant locations, including the gas scrubber. Tata needed a wireless solution to extend its control network securely to remote locations that would also provide seamless communication with existing control applications.
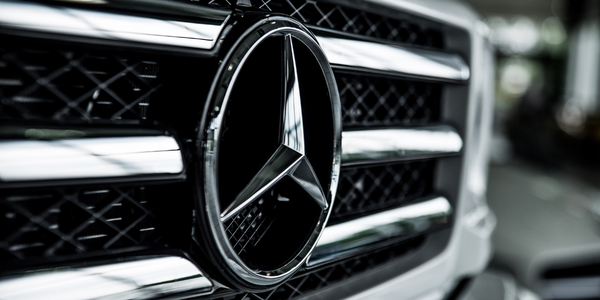
Case Study
Integral Plant Maintenance
Mercedes-Benz and his partner GAZ chose Siemens to be its maintenance partner at a new engine plant in Yaroslavl, Russia. The new plant offers a capacity to manufacture diesel engines for the Russian market, for locally produced Sprinter Classic. In addition to engines for the local market, the Yaroslavl plant will also produce spare parts. Mercedes-Benz Russia and his partner needed a service partner in order to ensure the operation of these lines in a maintenance partnership arrangement. The challenges included coordinating the entire maintenance management operation, in particular inspections, corrective and predictive maintenance activities, and the optimizing spare parts management. Siemens developed a customized maintenance solution that includes all electronic and mechanical maintenance activities (Integral Plant Maintenance).

Case Study
Advanced Elastomer Systems Upgrades Production
In order to maintain its share of the international market for thermoplastic elastomers AES recently expanded its Florida plant by adding a new production line. While the existing lines were operating satisfactorily using a PROVOX distributed control system with traditional analog I/O, AES wanted advanced technology on the new line for greater economy, efficiency, and reliability. AES officials were anxious to get this line into production to meet incoming orders, but two hurricanes slowed construction.