Technology Category
- Analytics & Modeling - Digital Twin / Simulation
- Functional Applications - Manufacturing Execution Systems (MES)
Applicable Industries
- Automotive
- Consumer Goods
Applicable Functions
- Product Research & Development
- Quality Assurance
Use Cases
- Manufacturing Process Simulation
- Transportation Simulation
Services
- Testing & Certification
About The Customer
APEL Extrusions Limited is a full-service extrusion manufacturer that specializes in aluminum extrusion and finishing. Founded in 1972 in Calgary, Alberta, Canada, APEL has since expanded its presence to Coburg, Oregon. The company services both western Canada and the western United States. APEL takes pride in being one of the very few full-service extrusion shops in North America, providing all services under one roof to maintain its customer-focused organization. The aluminum extrusions that APEL manufactures are used in a variety of applications such as residential and commercial construction, HVAC systems, recreational vehicles, consumer goods, and more. The company is committed to adapting to the wants and needs of customers while continuing to provide quality solutions that exceed extremely tight tolerances.
The Challenge
APEL Extrusions Limited, a full-service extrusion manufacturer specializing in aluminum extrusion and finishing, was facing a significant challenge in testing die extrusion performance while limiting time and cost. The company, which has a presence in both Canada and the United States, provides aluminum extrusions for a variety of applications including residential and commercial construction, HVAC systems, recreational vehicles, and consumer goods. The aluminum extrusion industry has been experiencing an increased demand for flat rolled and extruded aluminum products, primarily from the transportation sector. This trend, expected to continue through 2020, has put pressure on companies like APEL to adapt to customer needs while maintaining high-quality solutions that meet extremely tight tolerances. A critical step in APEL's process of providing high-quality products is the testing phase that occurs before the actual extrusion process begins.
The Solution
To address the challenge of testing die extrusion performance while limiting time and cost, APEL employed the extrusion simulation software, solidThinking Click2Extrude. This software allows the company to simulate the extrusion process prior to production. APEL places a high value on designing business solutions that meet its customers' needs, and believes that extensive research is a crucial part of its overall extrusion process. The company dedicates many resources to scientific research, instrumental development, and die performance research. By using solidThinking Click2Extrude, APEL was able to run numerous simulations in a short period of time to better determine the outcome of specific die designs. The software also allows APEL to detect any visible or invisible defects during the simulation, saving the company thousands of dollars by avoiding costly tooling, materials, and trials.
Operational Impact
Quantitative Benefit
Case Study missing?
Start adding your own!
Register with your work email and create a new case study profile for your business.
Related Case Studies.
.png)
Case Study
Improving Vending Machine Profitability with the Internet of Things (IoT)
The vending industry is undergoing a sea change, taking advantage of new technologies to go beyond just delivering snacks to creating a new retail location. Intelligent vending machines can be found in many public locations as well as company facilities, selling different types of goods and services, including even computer accessories, gold bars, tickets, and office supplies. With increasing sophistication, they may also provide time- and location-based data pertaining to sales, inventory, and customer preferences. But at the end of the day, vending machine operators know greater profitability is driven by higher sales and lower operating costs.
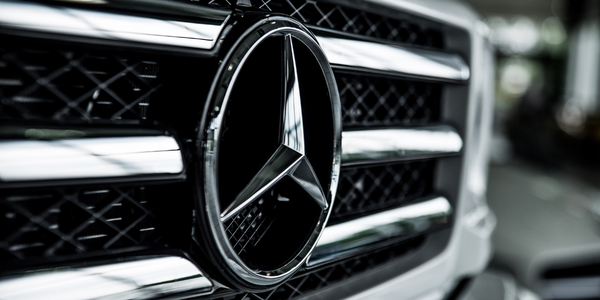
Case Study
Integral Plant Maintenance
Mercedes-Benz and his partner GAZ chose Siemens to be its maintenance partner at a new engine plant in Yaroslavl, Russia. The new plant offers a capacity to manufacture diesel engines for the Russian market, for locally produced Sprinter Classic. In addition to engines for the local market, the Yaroslavl plant will also produce spare parts. Mercedes-Benz Russia and his partner needed a service partner in order to ensure the operation of these lines in a maintenance partnership arrangement. The challenges included coordinating the entire maintenance management operation, in particular inspections, corrective and predictive maintenance activities, and the optimizing spare parts management. Siemens developed a customized maintenance solution that includes all electronic and mechanical maintenance activities (Integral Plant Maintenance).