Technology Category
- Analytics & Modeling - Digital Twin / Simulation
- Sensors - Level Sensors
Applicable Industries
- Automotive
- Packaging
Applicable Functions
- Product Research & Development
- Quality Assurance
Use Cases
- Digital Twin
- Virtual Reality
Services
- Testing & Certification
About The Customer
Prodrive is one of the world’s largest and most successful motorsport and technology businesses, with over 29 years of experience running race and rallying programmes for some of the biggest names in the sport, including Aston Martin, BMW, and MINI. Prodrive has been responsible for the Aston Martin Racing programme since 2004, handling all aspects of the programme, from the design and development of the range of GT race cars, to running the works team in sports car series across the world. The company is known for its commitment to optimizing weight, performance, reliability, and efficiency in race cars, a process that involves several engineering tasks.
The Challenge
Prodrive, a leading motorsport and technology business, was faced with the challenge of optimizing the performance of race car engines within a compressed timeframe. The main target was to analyze and improve the fluid flow within the water jacket of Aston Martin Racing engines and achieve reliable results quickly. The task was complicated by the need to solve several iterations of a model with complex geometry, and the work was to be done by relatively inexperienced users. The complexity and level of detail of the model, due to the cavities of the casting inside the engine head and the cylinder block, added to the challenge. Furthermore, Prodrive's simulation capabilities were limited by computer hardware, necessitating a solution that could maximize processing power without increasing license costs.
The Solution
Prodrive implemented AcuSolve, a leading general purpose Computational Fluid Dynamics (CFD) flow solver known for its robustness, speed, and accuracy. An automated process was generated with AcuSolve, which allowed for easy repeatability and streamlined the analysis of new geometry. This enabled the CAE engineers to generate reports for the Engine Development group for analysis and result interpretation. The first model in this process was a V8 engine water jacket. After a quick defeaturing process, the simulation could be loaded onto the solver in a matter of minutes. Altair’s token licensing system played a crucial role in maximizing Prodrive’s processing power, allowing the CAE Engineers to fully utilize the Hyperworks software suite as necessary, without dealing with increased license costs. Prodrive also plans to enhance the model by fully utilizing other capabilities within Altair’s Hyperworks Suite, such as Conjugate Heat Transfer analysis and further Post Processing Automation.
Operational Impact
Case Study missing?
Start adding your own!
Register with your work email and create a new case study profile for your business.
Related Case Studies.
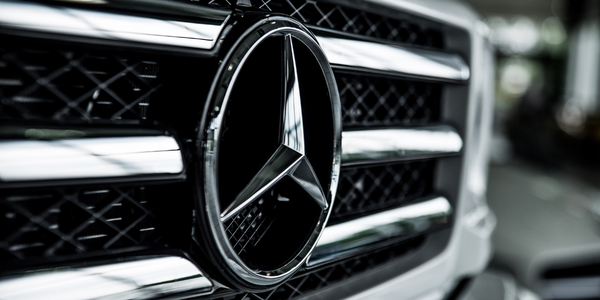
Case Study
Integral Plant Maintenance
Mercedes-Benz and his partner GAZ chose Siemens to be its maintenance partner at a new engine plant in Yaroslavl, Russia. The new plant offers a capacity to manufacture diesel engines for the Russian market, for locally produced Sprinter Classic. In addition to engines for the local market, the Yaroslavl plant will also produce spare parts. Mercedes-Benz Russia and his partner needed a service partner in order to ensure the operation of these lines in a maintenance partnership arrangement. The challenges included coordinating the entire maintenance management operation, in particular inspections, corrective and predictive maintenance activities, and the optimizing spare parts management. Siemens developed a customized maintenance solution that includes all electronic and mechanical maintenance activities (Integral Plant Maintenance).

Case Study
IoT Data Analytics Case Study - Packaging Films Manufacturer
The company manufactures packaging films on made to order or configure to order basis. Every order has a different set of requirements from the product characteristics perspective and hence requires machine’s settings to be adjusted accordingly. If the film quality does not meet the required standards, the degraded quality impacts customer delivery causes customer dissatisfaction and results in lower margins. The biggest challenge was to identify the real root cause and devise a remedy for that.

Case Study
Monitoring of Pressure Pumps in Automotive Industry
A large German/American producer of auto parts uses high-pressure pumps to deburr machined parts as a part of its production and quality check process. They decided to monitor these pumps to make sure they work properly and that they can see any indications leading to a potential failure before it affects their process.