Technology Category
- Sensors - Environmental Sensors
- Sensors - Utility Meters
Applicable Industries
- Aerospace
- Agriculture
Applicable Functions
- Maintenance
- Product Research & Development
Use Cases
- Agricultural Drones
- Intelligent Urban Water Supply Management
Services
- Cloud Planning, Design & Implementation Services
- Training
About The Customer
The customer in this case study is the Atmospheric Physics group at the Swiss Federal Institute of Technology in Zurich (ETH Zurich), led by Professor Ulrike Lohmann. The group is involved in climate research, with a focus on studying the formation and evolution of clouds, especially cloud-aerosol interactions. One of their projects, CLOUDLAB, is dedicated to improving the understanding of cloud microphysical processes and precipitation formation to better simulate and predict precipitation events. The group conducts cloud seeding experiments in wintertime stratus clouds to study ice crystal formation and growth, using a multi-dimensional set of observations and numerical modeling.
The Challenge
Clouds play a crucial role in regulating Earth’s climate, and understanding their microphysics is key to more accurate climate projections. However, clouds and cloud-aerosol interactions are major sources of uncertainties in these projections. Questions such as how clouds will change in a warming climate and their influence on Earth’s radiation budget are yet to be fully answered. The Atmospheric Physics group at the Swiss Federal Institute of Technology in Zurich (ETH Zurich) is dedicated to studying the formation and evolution of clouds, particularly cloud-aerosol interactions. Their project, CLOUDLAB, aims to improve understanding of cloud microphysical processes and precipitation formation. However, the data collection process for cloud particles, wind, and aerosol concentration has evolved over the years, with each method presenting its own challenges. Ground-based measurements were influenced by the ground and blowing snow, while measurements on a cable car and tethered balloons offered limited vertical structure and location possibilities.
The Solution
To overcome these challenges, the CLOUDLAB team adopted Meteomatics’ Weather Drones, or Meteodrones. These drones offered more flexible measurement paths using integrated atmospheric measurement sensors and allowed the team to perform targeted cloud seeding experiments. The Meteodrones were engineered to resist very low temperatures and high wind speeds, making them ideal for flying into supercooled clouds for cloud seeding. The team could control exactly where to inject particles into the cloud and directly measure the downstream ice crystals to infer ice crystal growth rates. Meteomatics created a bespoke solution for CLOUDLAB, providing two MM-670 ML Meteodrones adapted to their specific needs. One drone was equipped with flares for cloud seeding, and the other with an optical particle counter for measuring aerosol particles in-flight. The drone software was also adjusted to make it easier for the CLOUDLAB team to configure their flight missions.
Operational Impact
Quantitative Benefit
Case Study missing?
Start adding your own!
Register with your work email and create a new case study profile for your business.
Related Case Studies.
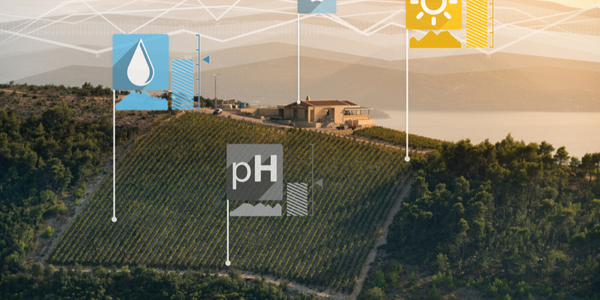
Case Study
Intelligent Farming with ThingWorx Analytics
Z Farms was facing three challenges: costly irrigation systems with water as a limited resource, narrow optimal ranges of soil moisture for growth with difficult maintenance and farm operators could not simply turn on irrigation systems like a faucet.
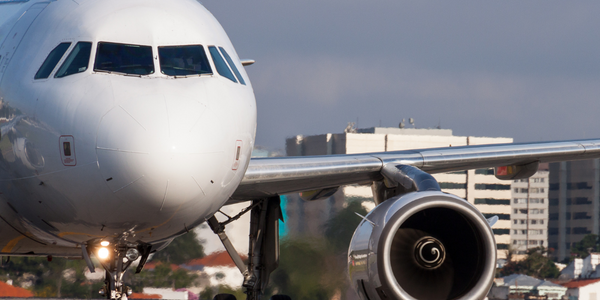
Case Study
Airbus Soars with Wearable Technology
Building an Airbus aircraft involves complex manufacturing processes consisting of thousands of moving parts. Speed and accuracy are critical to business and competitive advantage. Improvements in both would have high impact on Airbus’ bottom line. Airbus wanted to help operators reduce the complexity of assembling cabin seats and decrease the time required to complete this task.
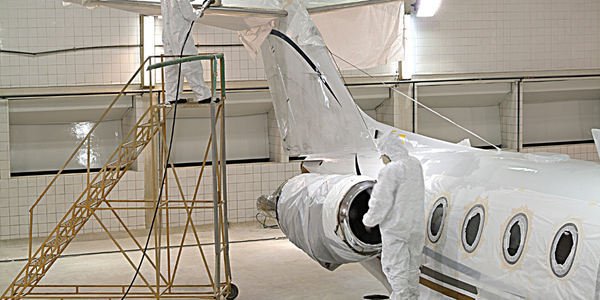
Case Study
Aircraft Predictive Maintenance and Workflow Optimization
First, aircraft manufacturer have trouble monitoring the health of aircraft systems with health prognostics and deliver predictive maintenance insights. Second, aircraft manufacturer wants a solution that can provide an in-context advisory and align job assignments to match technician experience and expertise.
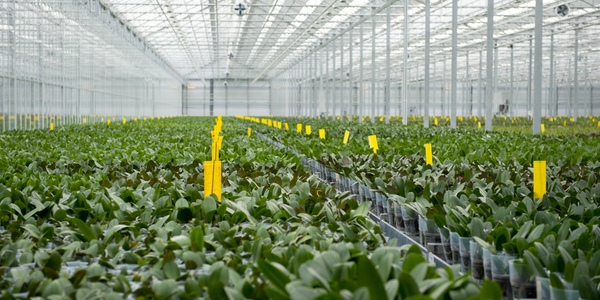
Case Study
Greenhouse Intelligent Monitoring and Control Solution
Farming Orchids is the most successful form of precision farming in Taiwan, and also the most exported flower. Orchids need a specific temperature and humidity conditions to grow and bloom, and its flowering time may not be in line with market demands, so the price collapses when there is overproduction. Therefore, some farmers began to import automated greenhouse control systems for breeding and forcing, which not only improves quality, but also effectively controls the production period and yield to ensure revenue. In 2012, an orchid farmer built a Forcing Greenhouse of about 200 pings (approximately 661 Square Meters) in Tainan, Taiwan. The system integrator adopted Advantech’s APAX-5000 series programmable automation controllers to build the control platform, coupled with Advantech WebAccess HMI/SCADA software, to achieve cloud monitoring. The staff of the orchid field can monitor important data anytime via smart phone, iPad, and other handheld devices, and control the growth and flowering conditions. System requirements: In the past, most environmental control systems of orchid greenhouses in Taiwan used PLCs (Programmable Logic Controller) with poorscalability and control, and could not be connected to the Internet formonitoring from the cloud. For advanced database analysis and networking capability, the PC platform must be adopted. Therefore, PAC Systems (Programmable Automation Controller) with both PLC programming capabilities andPC functions is a better choice.The environmental control of the Orchid greenhouse switches on and off devices like fan, shade net, cooling/heat pump, liquid flow control, water-cooling wall etc. It is controlled by a control panel of electric controllers, and is driven by a motor, to adjust the greenhouse temperature, humidity, and other environmental conditions to the set parameters.