Technology Category
- Drones - Multirotor Drones
- Robots - Autonomous Guided Vehicles (AGV)
Applicable Industries
- Automotive
Applicable Functions
- Product Research & Development
Use Cases
- Time Sensitive Networking
- Vehicle Performance Monitoring
About The Customer
TRW Automotive is a leading automotive supplier based in the U.S.A. The company is among the world's largest automotive suppliers and is recognized as one of the top financial performers in the industry. TRW Automotive supplies more than 40 major vehicle manufacturers and holds leading positions in all of its primary product categories. One of these categories is braking systems, where the company has developed a reputation for innovation and quality. The company's commitment to leveraging technology to improve efficiency and competitiveness is evident in its approach to the design and validation of brake rotors.
The Challenge
TRW Automotive, one of the world's largest automotive suppliers, faced a significant challenge in the design and validation process of brake rotors. Vehicle manufacturers require both virtual and empirical validation for design proposals, and the maturity of these proposals often determines the awarding of new business contracts. To remain competitive, suppliers like TRW Automotive must become more efficient in their design and validation processes. This need for efficiency has driven the automotive supplier base to further leverage and expedite upfront Computer-Aided Engineering (CAE). However, the traditional CAE process, which involves a sequential approach to pre-processing, solving, and post-processing, was proving to be too long and inefficient. This process had to be repeated for each design concept and across various analysis types. If the final analysis did not meet performance targets, the process had to be started over, wasting valuable time.
The Solution
To address these challenges, TRW Automotive developed a novel approach for the evaluation of brake rotor designs that significantly improved analysis throughput and expedited the design cycle. They built a custom template within the ANSYS Workbench environment that captured various analysis types specific to brake rotor design needs. This brake rotor template automatically read in CAD model, applied loads and boundary conditions, and ran the entire analysis suite. The template approach allowed for simultaneous design evaluation of thermal, stress, and dynamic performance. It also enabled concurrent development of multiple design proposals and a full assessment of design performance. This innovative solution increased automation, brought analysis to the upfront of the design cycle, and allowed for a more thorough evaluation of design proposals.
Operational Impact
Quantitative Benefit
Case Study missing?
Start adding your own!
Register with your work email and create a new case study profile for your business.
Related Case Studies.
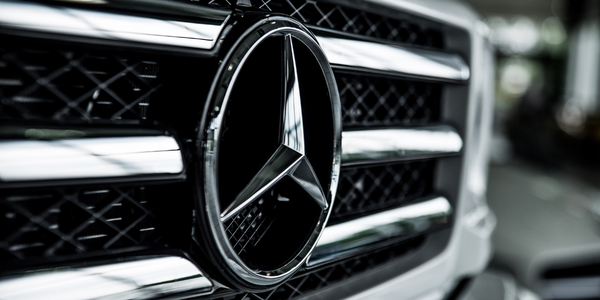
Case Study
Integral Plant Maintenance
Mercedes-Benz and his partner GAZ chose Siemens to be its maintenance partner at a new engine plant in Yaroslavl, Russia. The new plant offers a capacity to manufacture diesel engines for the Russian market, for locally produced Sprinter Classic. In addition to engines for the local market, the Yaroslavl plant will also produce spare parts. Mercedes-Benz Russia and his partner needed a service partner in order to ensure the operation of these lines in a maintenance partnership arrangement. The challenges included coordinating the entire maintenance management operation, in particular inspections, corrective and predictive maintenance activities, and the optimizing spare parts management. Siemens developed a customized maintenance solution that includes all electronic and mechanical maintenance activities (Integral Plant Maintenance).

Case Study
Monitoring of Pressure Pumps in Automotive Industry
A large German/American producer of auto parts uses high-pressure pumps to deburr machined parts as a part of its production and quality check process. They decided to monitor these pumps to make sure they work properly and that they can see any indications leading to a potential failure before it affects their process.