Technology Category
- Infrastructure as a Service (IaaS) - Cloud Computing
- Sensors - Temperature Sensors
Applicable Industries
- Automotive
- Cement
Applicable Functions
- Product Research & Development
- Quality Assurance
Use Cases
- Construction Management
- Infrastructure Inspection
Services
- Hardware Design & Engineering Services
- Testing & Certification
About The Customer
Ford Motor Company is a leading automotive manufacturer, producing cars, trucks, vans, and SUVs that are safer, quieter, and more comfortable than ever. Many of the intangibles that contribute to Ford's quality flow from the innovative use of high-performance computing (HPC) techniques. At Ford’s Numerically Intensive Computing Department (NIC) in Dearborn, Michigan, engineers run simulations in codes such as NASTRAN and LS-DYNA for predictive analysis of cylinder cooling, wind noise, vibration, ride quality, crashworthiness, durability, and other characteristics that contribute to industry-leading automotive design.
The Challenge
Ford's Numerically Intensive Computing Department (NIC) had built a substantial heterogeneous High-Performance Computing (HPC) environment over the years, combining both capacity and capability. This environment included Beowulf clusters based on Xeon, Itanium, and Alpha processors, SGI Origin and Altix servers, IBMP650 capacity, and large SMP Cray systems. While this infrastructure enabled NIC to process compute-intensive jobs in a timely manner, it also resulted in a complex infrastructure of platforms and applications. Additionally, NIC faced complexity on the solver side, running many application versions, none of which ran on all architectures. The challenge was to find a solution that could efficiently manage this complex infrastructure and provide a simple tool for users.
The Solution
NIC adopted PBS Professional to manage its complex hardware and software with job attributes. The previous workload manager had reached its scalability limits and could not efficiently handle NIC's increasing processor count. After evaluating commercially available workload management software, NIC chose PBS Professional due to its cost, flexibility, and availability of source code. The availability of PBS Professional source code allowed NIC to run the PBS Professional server infrastructure and develop a custom scheduling package that runs on top of it. PBS Professional infrastructure gave NIC the freedom to move in a technology market where processors are rising in performance and dropping in cost. It allowed NIC to bring in the latest technologies to ensure that Ford is getting maximum value for its hardware dollar, and PBS Professional enabled NIC to plug them in and present them to users as part of a single resource.
Operational Impact
Quantitative Benefit
Case Study missing?
Start adding your own!
Register with your work email and create a new case study profile for your business.
Related Case Studies.
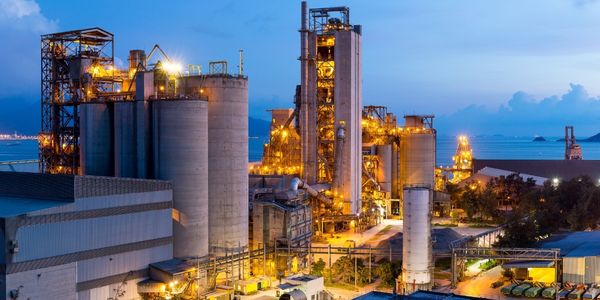
Case Study
System 800xA at Indian Cement Plants
Chettinad Cement recognized that further efficiencies could be achieved in its cement manufacturing process. It looked to investing in comprehensive operational and control technologies to manage and derive productivity and energy efficiency gains from the assets on Line 2, their second plant in India.
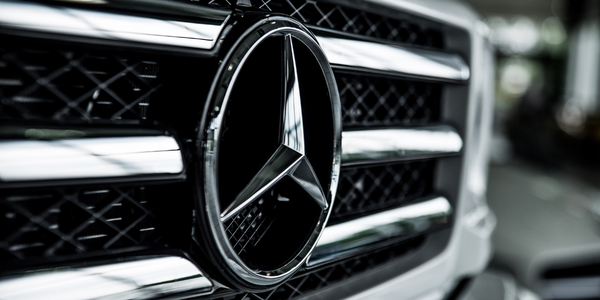
Case Study
Integral Plant Maintenance
Mercedes-Benz and his partner GAZ chose Siemens to be its maintenance partner at a new engine plant in Yaroslavl, Russia. The new plant offers a capacity to manufacture diesel engines for the Russian market, for locally produced Sprinter Classic. In addition to engines for the local market, the Yaroslavl plant will also produce spare parts. Mercedes-Benz Russia and his partner needed a service partner in order to ensure the operation of these lines in a maintenance partnership arrangement. The challenges included coordinating the entire maintenance management operation, in particular inspections, corrective and predictive maintenance activities, and the optimizing spare parts management. Siemens developed a customized maintenance solution that includes all electronic and mechanical maintenance activities (Integral Plant Maintenance).

Case Study
Monitoring of Pressure Pumps in Automotive Industry
A large German/American producer of auto parts uses high-pressure pumps to deburr machined parts as a part of its production and quality check process. They decided to monitor these pumps to make sure they work properly and that they can see any indications leading to a potential failure before it affects their process.