Technology Category
- Analytics & Modeling - Digital Twin / Simulation
- Automation & Control - Human Machine Interface (HMI)
Applicable Industries
- Aerospace
- Equipment & Machinery
Applicable Functions
- Product Research & Development
Services
- System Integration
- Testing & Certification
About The Customer
GE Aviation’s Systems business is a unit that designs and produces systems critical to the interface between jet engines and the airframe onto which they are installed. Although Systems works closely with GE Aviation, the products it produces are differentiated enough that many of the typical design tools used for engines are not ideally suited for the accessories produced by Systems. However, by leveraging the experience of GE Aviation and its digital tools team, tools such as Flow Simulator are able to be used by Systems to design and analyze subcomponents that are critical to producing next-gen generators and electrical systems.
The Challenge
GE Aviation’s Systems business, a unit that designs and produces systems critical to the interface between jet engines and the airframe, was tasked with providing a backup generator (BUG) for a new aircraft. This generator was to provide electrical power in the event of multiple failures of other systems. The BUG had to be mounted onto a newly designed engine to receive mechanical power, but maintain independence from the engine to ensure functionality. It had its own oil network, pump, and sump to provide lubrication and cooling to the electromagnetic components and bearings in the generator. The lubrication system relied on a gravity drain to return the oil from a bearing cavity to the onboard sump where the oil pump was located. The team needed to ensure that the drain was adequately sized to allow for passage of the worst-case level of oil flow so that oil does not build up and cause excess heat generation or any other sinister effects within the bearings. Due to the constraints on size and program timing, an analytical approach was desired to determine the capability of the current drainage passage network and the minimum size that will be required.
The Solution
The team needed a tool with enough flexibility to quickly and accurately model a new system along with redesign iterations. They found their solution in Flow Simulator. The tool's graphical user interface (GUI) allowed for a quick identification and setup of the complex network of tubes, bends, junctions and plenums. The elemental “building block” style setup allows for each element to be linked appropriately and automatically accounts differences in size, shape, pressures, and flows from a number of different branches in one model. The results from Flow Simulator were validated with proven excel-based tools used throughout GE Aviation. The system contains features which allowed for evaluation of the geometry using multiple configurations. The team was able to test the drain’s capability using a pressure difference in the inlet and exit cavity as well as a gravity-fed elevation approach. Once an initial model is built, design iterations could be tested rapidly for a wide range of pressures, temperatures, and geometries.
Case Study missing?
Start adding your own!
Register with your work email and create a new case study profile for your business.
Related Case Studies.
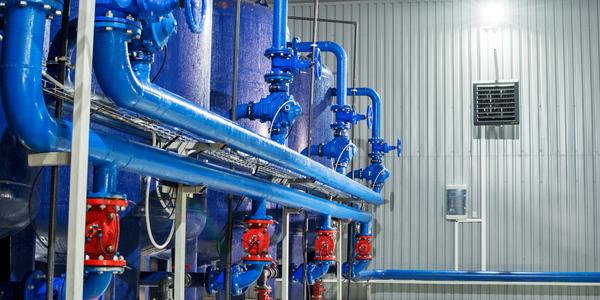
Case Study
Smart Water Filtration Systems
Before working with Ayla Networks, Ozner was already using cloud connectivity to identify and solve water-filtration system malfunctions as well as to monitor filter cartridges for replacements.But, in June 2015, Ozner executives talked with Ayla about how the company might further improve its water systems with IoT technology. They liked what they heard from Ayla, but the executives needed to be sure that Ayla’s Agile IoT Platform provided the security and reliability Ozner required.
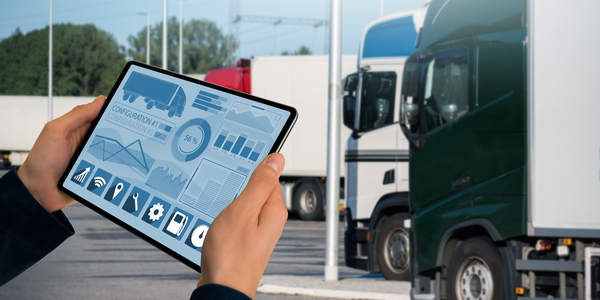
Case Study
IoT enabled Fleet Management with MindSphere
In view of growing competition, Gämmerler had a strong need to remain competitive via process optimization, reliability and gentle handling of printed products, even at highest press speeds. In addition, a digitalization initiative also included developing a key differentiation via data-driven services offers.
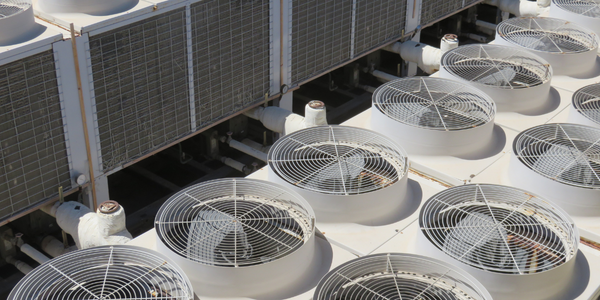
Case Study
Predictive Maintenance for Industrial Chillers
For global leaders in the industrial chiller manufacturing, reliability of the entire production process is of the utmost importance. Chillers are refrigeration systems that produce ice water to provide cooling for a process or industrial application. One of those leaders sought a way to respond to asset performance issues, even before they occur. The intelligence to guarantee maximum reliability of cooling devices is embedded (pre-alarming). A pre-alarming phase means that the cooling device still works, but symptoms may appear, telling manufacturers that a failure is likely to occur in the near future. Chillers who are not internet connected at that moment, provide little insight in this pre-alarming phase.
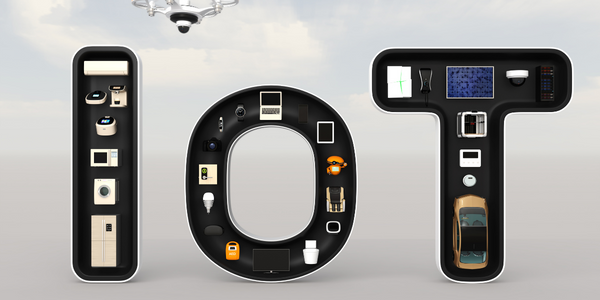
Case Study
Premium Appliance Producer Innovates with Internet of Everything
Sub-Zero faced the largest product launch in the company’s history:It wanted to launch 60 new products as scheduled while simultaneously opening a new “greenfield” production facility, yet still adhering to stringent quality requirements and manage issues from new supply-chain partners. A the same time, it wanted to increase staff productivity time and collaboration while reducing travel and costs.
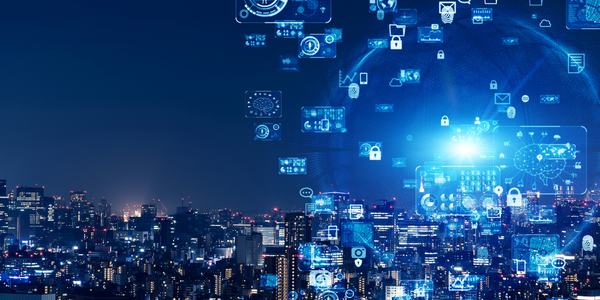
Case Study
Integration of PLC with IoT for Bosch Rexroth
The application arises from the need to monitor and anticipate the problems of one or more machines managed by a PLC. These problems, often resulting from the accumulation over time of small discrepancies, require, when they occur, ex post technical operations maintenance.
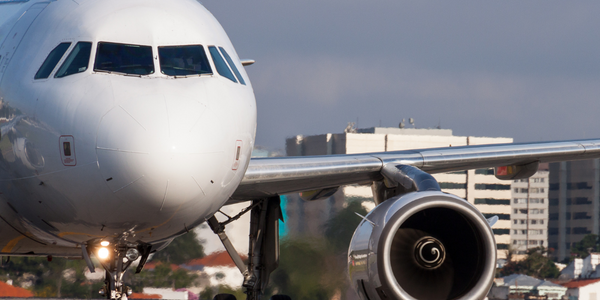
Case Study
Airbus Soars with Wearable Technology
Building an Airbus aircraft involves complex manufacturing processes consisting of thousands of moving parts. Speed and accuracy are critical to business and competitive advantage. Improvements in both would have high impact on Airbus’ bottom line. Airbus wanted to help operators reduce the complexity of assembling cabin seats and decrease the time required to complete this task.