Technology Category
- Sensors - Flow Meters
- Sensors - Liquid Detection Sensors
Applicable Industries
- Electrical Grids
- Oil & Gas
Use Cases
- Continuous Emission Monitoring Systems
- Leakage & Flood Monitoring
About The Customer
GE Power is a world energy leader that provides technology, solutions, and services across the entire energy value chain from the point of generation to consumption. The company is transforming the electricity industry by uniting all the resources and scale of the world’s first Digital Industrial company. GE Power's customers operate in more than 150 countries, and together they power more than a third of the world to illuminate cities, build economies and connect the world. The company holds the only two Guinness World Records for Gas Turbine combined cycle efficiency for 50Hz and 60Hz power generation plants in commercial operation.
The Challenge
GE Power, a global leader in energy technology, solutions, and services, faced the challenge of maintaining precise understanding of the flow of cooling and leakage air in their gas turbine engines. This precision was crucial for achieving low emissions of NOx and setting world records for gas turbine combined cycle efficiency. The complexity of the internal engine components and their interactions during various operations, from cold start to shut down, required a sophisticated tool. The company needed a solution that could manage the clearances between rotating and stationary components to the width of a few human hairs, understand the transient thermal response of the engine, and track the impact of cooling and leakage air on gas turbine efficiency and emissions.
The Solution
GE Power adopted the Flow Simulator tool, an internally developed 1-D network flow solver, to address these challenges. This tool became their day-to-day workhorse for designing the secondary flow circuit within a gas turbine engine, its bearing system, combustion, and accessory systems. The Flow Simulator's modern user interface made it easy for secondary flow designers to transition to it. The tool presents branches in the flow circuit on an engine cross-section, enabling a more intuitive understanding of the system. One of the greatest attributes of Flow Simulator is its solver speed, which allows designers to run full probabilistic analysis to understand every possible way customers can run their engines and the impact of manufacturing variation on pressures and flow rates. The numerical stability of the solver enables a broader range of parameter exploration than its predecessor. Boundary condition mapping is also easy and accuracy is ensured using an extensive database of peer-reviewed correlations and the facility to incorporate specialized proprietary correlations.
Operational Impact
Quantitative Benefit
Case Study missing?
Start adding your own!
Register with your work email and create a new case study profile for your business.
Related Case Studies.
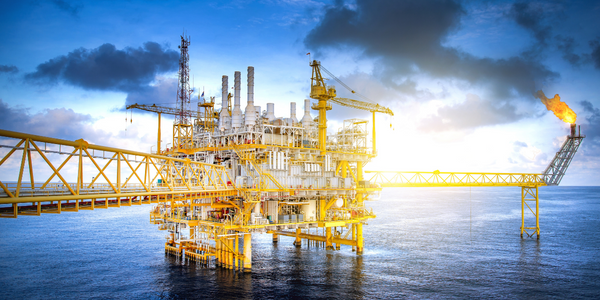
Case Study
Taking Oil and Gas Exploration to the Next Level
DownUnder GeoSolutions (DUG) wanted to increase computing performance by 5 to 10 times to improve seismic processing. The solution must build on current architecture software investments without sacrificing existing software and scale computing without scaling IT infrastructure costs.
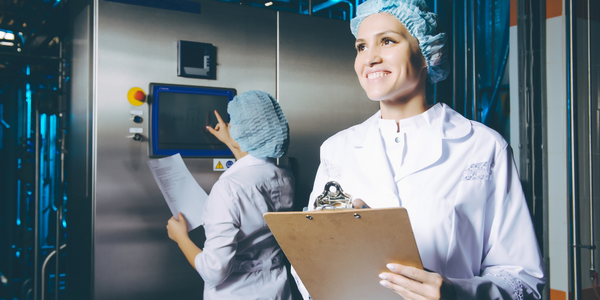
Case Study
Remote Wellhead Monitoring
Each wellhead was equipped with various sensors and meters that needed to be monitored and controlled from a central HMI, often miles away from the assets in the field. Redundant solar and wind generators were installed at each wellhead to support the electrical needs of the pumpstations, temperature meters, cameras, and cellular modules. In addition to asset management and remote control capabilities, data logging for remote surveillance and alarm notifications was a key demand from the customer. Terra Ferma’s solution needed to be power efficient, reliable, and capable of supporting high-bandwidth data-feeds. They needed a multi-link cellular connection to a central server that sustained reliable and redundant monitoring and control of flow meters, temperature sensors, power supply, and event-logging; including video and image files. This open-standard network needed to interface with the existing SCADA and proprietary network management software.
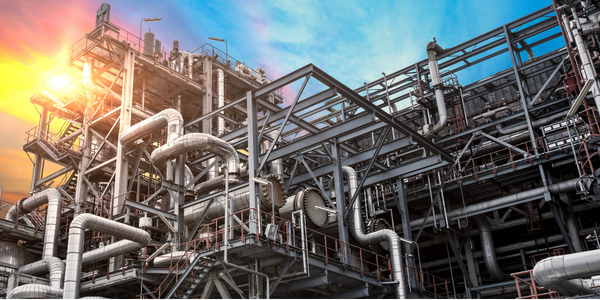
Case Study
Refinery Saves Over $700,000 with Smart Wireless
One of the largest petroleum refineries in the world is equipped to refine various types of crude oil and manufacture various grades of fuel from motor gasoline to Aviation Turbine Fuel. Due to wear and tear, eight hydrogen valves in each refinery were leaking, and each cost $1800 per ton of hydrogen vented. The plant also had leakage on nearly 30 flare control hydrocarbon valves. The refinery wanted a continuous, online monitoring system that could catch leaks early, minimize hydrogen and hydrocarbon production losses, and improve safety for maintenance.