Applicable Industries
- Chemicals
- Consumer Goods
About The Customer
Henkel is a renowned multinational company that operates worldwide with leading innovations, brands, and technologies in three business areas: Adhesive Technologies, Beauty Care, and Laundry & Home Care. Founded in 1876, Henkel holds globally leading market positions both in the consumer and industrial businesses with well-known brands such as Persil, Schwarzkopf, and Loctite. The company is committed to leadership in sustainability and aims to maintain high ethical standards. It seeks to optimize its processes wherever possible to conserve valuable resources and contribute to its sustainability goals.
The Challenge
Henkel, a global leader in consumer goods and chemicals, was facing a significant challenge in optimizing its energy-intensive spray drying process in detergent production. The process was not only consuming a substantial amount of energy but also lacked the efficiency required for a streamlined production process. The company was in dire need of a solution that could modernize this process, conserve valuable resources, and contribute to its sustainability goals. The challenge was to find a system that could seamlessly integrate with their existing infrastructure and provide real-time insights for better decision-making.
The Solution
To address this challenge, Henkel implemented ProLeiT by Schneider Electric’s Plant iT control system and leading-edge industrial software from AVEVA. The Plant iT control system provided a robust and reliable solution for managing the complex spray drying process. It offered real-time monitoring and control capabilities, enabling Henkel to optimize its operations and reduce energy consumption. On the other hand, AVEVA's industrial software provided advanced analytics and reporting features. It allowed Henkel to gain valuable insights into its operations, identify areas for improvement, and make data-driven decisions. The combination of these two solutions empowered the operators and significantly improved the energy efficiency of the spray drying process.
Operational Impact
Quantitative Benefit
Case Study missing?
Start adding your own!
Register with your work email and create a new case study profile for your business.
Related Case Studies.
.png)
Case Study
Improving Vending Machine Profitability with the Internet of Things (IoT)
The vending industry is undergoing a sea change, taking advantage of new technologies to go beyond just delivering snacks to creating a new retail location. Intelligent vending machines can be found in many public locations as well as company facilities, selling different types of goods and services, including even computer accessories, gold bars, tickets, and office supplies. With increasing sophistication, they may also provide time- and location-based data pertaining to sales, inventory, and customer preferences. But at the end of the day, vending machine operators know greater profitability is driven by higher sales and lower operating costs.
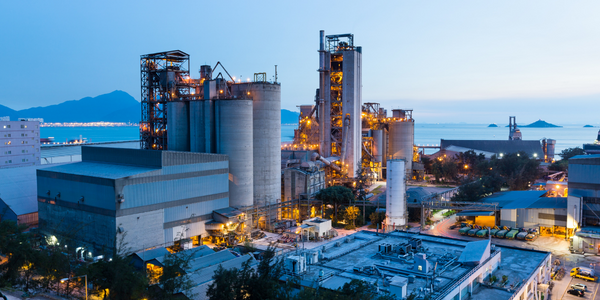
Case Study
Honeywell - Tata Chemicals Improves Data Accessibility with OneWireless
Tata was facing data accessibility challenges in the cement plant control room tapping signals from remote process control areas and other distant locations, including the gas scrubber. Tata needed a wireless solution to extend its control network securely to remote locations that would also provide seamless communication with existing control applications.

Case Study
Advanced Elastomer Systems Upgrades Production
In order to maintain its share of the international market for thermoplastic elastomers AES recently expanded its Florida plant by adding a new production line. While the existing lines were operating satisfactorily using a PROVOX distributed control system with traditional analog I/O, AES wanted advanced technology on the new line for greater economy, efficiency, and reliability. AES officials were anxious to get this line into production to meet incoming orders, but two hurricanes slowed construction.
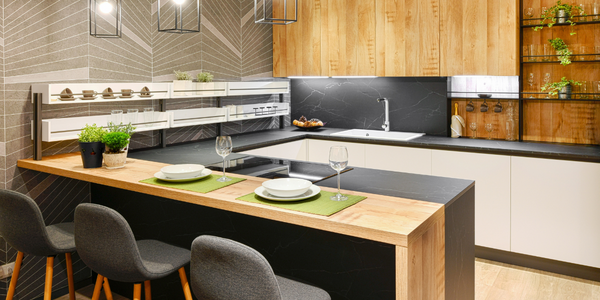
Case Study
Series Production with Lot-size-1 Flexibility
Nobilia manufactures customized fitted kitchens with a lot size of 1. They require maximum transparency of tracking design data and individual processing steps so that they can locate a particular piece of kitchen furniture in the sequence of processes.