Technology Category
- Application Infrastructure & Middleware - Data Visualization
- Sensors - Autonomous Driving Sensors
Applicable Industries
- Aerospace
- Automotive
Applicable Functions
- Maintenance
- Product Research & Development
Use Cases
- Smart Parking
- Vehicle-to-Infrastructure
Services
- Data Science Services
About The Customer
Prodrive was founded in 1984 with a focus on motorsports, and today develops innovative engineering solutions for businesses within the automotive, aerospace, defense, and marine sectors. The firm has been behind some of the greatest names in motorsports. For example, it has built nearly 400 Aston Martin GT cars and continues to support the company through each race it runs. Its composite materials division manufactures lightweight carbon fiber-reinforced polymer and visual carbon components. Prodrive is the largest company of its kind in the U.K. and is a world leader in motorsport technology, resulting in its long list of wins in Formula 1, The Dakar Rally, Le Mans, and the World Rally Championship.
The Challenge
Prodrive, a leading motorsport technology company, faced a significant challenge with its legacy analytics system. The system collected sensor data from its cars, but struggled with large datasets collected over long periods of time. Analyzing engine data over a car’s lifetime was crucial for Prodrive as it could provide valuable insight into design and manufacturing tweaks that could improve vehicle performance. Furthermore, accurately predicting when critical components are likely to fail would help racing teams optimize pit stop timing during races. Given the number of sensors in Prodrive-built cars and their sampling frequencies, the amount of data collected over a car’s lifetime was significant. Each car could produce about half a terabyte of data during an average race weekend and five to ten terabytes of data every week during test runs. Prodrive needed data analytics software that could manage very large volumes of data, provide better management capabilities, and support fast development and implementation cycles.
The Solution
Prodrive sought a solution that could process and visualize multiple streams of high frequency, real-time data, and improve communications about important findings with the executive staff. They had been using Python and similar tools to develop custom dashboards and stream processing applications, but these tools couldn’t meet their capacity demands, weren’t user friendly, needed long development times, and required a team of experienced coders. Prodrive turned to Altair, a trusted supplier for over 16 years, and investigated whether Altair’s data analytics platforms were the solution they needed. The team selected Altair Panopticon™ to address the data visualization and stream processing requirements and then worked with Altair to conduct a proof of concept deployment – which proved successful. Today, Prodrive uses Panopticon to display historic and real-time data streaming in from its cars in dashboards the Prodrive engineers can design, deploy, and maintain without IT assistance. Its stream processing applications make on-the-fly comparisons and apply sophisticated statistical functions to data to identify outliers and anomalies automatically.
Operational Impact
Quantitative Benefit
Case Study missing?
Start adding your own!
Register with your work email and create a new case study profile for your business.
Related Case Studies.
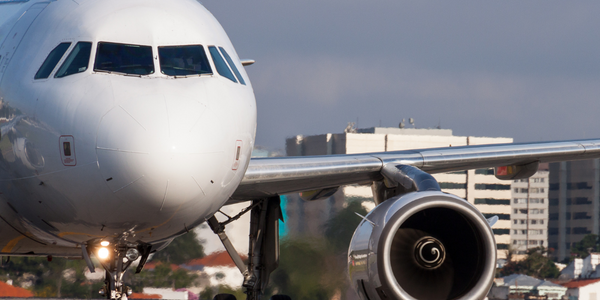
Case Study
Airbus Soars with Wearable Technology
Building an Airbus aircraft involves complex manufacturing processes consisting of thousands of moving parts. Speed and accuracy are critical to business and competitive advantage. Improvements in both would have high impact on Airbus’ bottom line. Airbus wanted to help operators reduce the complexity of assembling cabin seats and decrease the time required to complete this task.
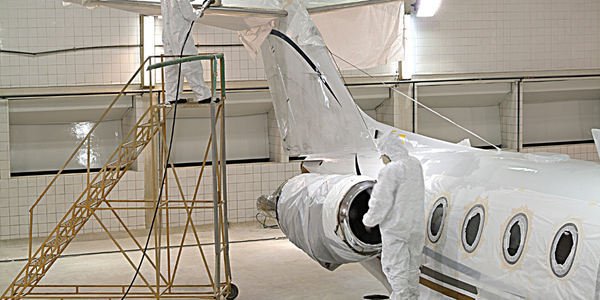
Case Study
Aircraft Predictive Maintenance and Workflow Optimization
First, aircraft manufacturer have trouble monitoring the health of aircraft systems with health prognostics and deliver predictive maintenance insights. Second, aircraft manufacturer wants a solution that can provide an in-context advisory and align job assignments to match technician experience and expertise.
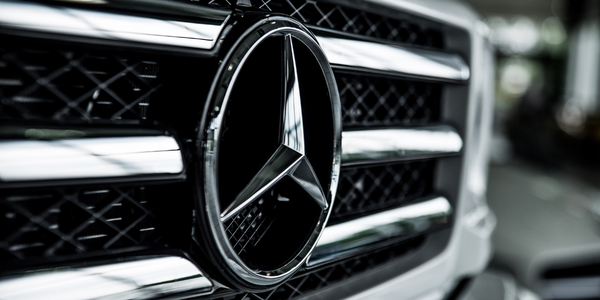
Case Study
Integral Plant Maintenance
Mercedes-Benz and his partner GAZ chose Siemens to be its maintenance partner at a new engine plant in Yaroslavl, Russia. The new plant offers a capacity to manufacture diesel engines for the Russian market, for locally produced Sprinter Classic. In addition to engines for the local market, the Yaroslavl plant will also produce spare parts. Mercedes-Benz Russia and his partner needed a service partner in order to ensure the operation of these lines in a maintenance partnership arrangement. The challenges included coordinating the entire maintenance management operation, in particular inspections, corrective and predictive maintenance activities, and the optimizing spare parts management. Siemens developed a customized maintenance solution that includes all electronic and mechanical maintenance activities (Integral Plant Maintenance).
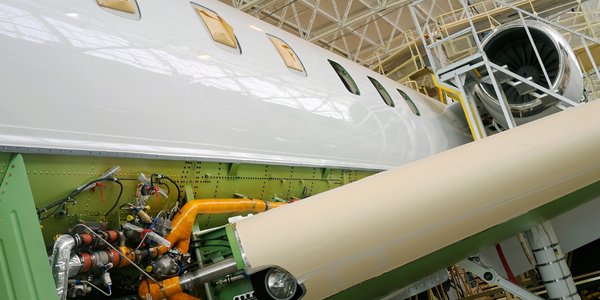
Case Study
Aerospace & Defense Case Study Airbus
For the development of its new wide-body aircraft, Airbus needed to ensure quality and consistency across all internal and external stakeholders. Airbus had many challenges including a very aggressive development schedule and the need to ramp up production quickly to satisfy their delivery commitments. The lack of communication extended design time and introduced errors that drove up costs.