Technology Category
- Functional Applications - Enterprise Resource Planning Systems (ERP)
- Functional Applications - Warehouse Management Systems (WMS)
Applicable Industries
- Automotive
- Transportation
Applicable Functions
- Procurement
- Warehouse & Inventory Management
Use Cases
- Last Mile Delivery
- Service Parts Management
Services
- System Integration
- Testing & Certification
About The Customer
The customer in this case study is a major German automotive manufacturer with a critical load requirement for order fulfillment. The manufacturer is one of the world's largest automotive customers with complex Service Parts Management requirements. The customer operates in a competitive environment that demands greater efficiencies and integration of manufacturing, inventory, and logistics systems. The customer also requires a solution that can adapt to a dynamic, constantly changing environment, provide worldwide accessibility and visibility of information, and support operations ranging from small to very large service parts.
The Challenge
The case study revolves around the challenge of managing high-volume Service Parts Management (SPM) requirements in a competitive environment that demands greater efficiencies. Companies with complex SPM requirements are under pressure to integrate their manufacturing, inventory, and logistics systems more effectively to achieve significant cost savings. The challenge is further compounded by the need for a solution that can adapt to a dynamic, constantly changing environment, provide worldwide accessibility and visibility of information, and support operations ranging from small to very large service parts. The case study also highlights a specific request from a major German automotive manufacturer with a critical load requirement for order fulfillment.
The Solution
IBM and SAP collaborated to create a solution that could handle the high-volume SPM requirements of the world's largest automotive customers. The solution was built on IBM DB2, IBM System p servers, and IBM System Storage infrastructure, and used the SAP solution for Service Parts Management. The solution was tested for performance and scalability using production data from existing automotive customers. The tests were designed to ensure the quality, performance, and stability of the solution under high load conditions, and demonstrate sufficient scalability for a high-volume business. The solution includes several SAP applications, including SAP SCM – Service Parts Planning, SAP CRM – Service Parts Fulfillment, SAP SCM – Service Parts Warehousing with SAP Extended Warehouse Management, SAP ERP – Service Parts Management Execution, and SAP SPT – Service Parts Transportation.
Operational Impact
Quantitative Benefit
Case Study missing?
Start adding your own!
Register with your work email and create a new case study profile for your business.
Related Case Studies.
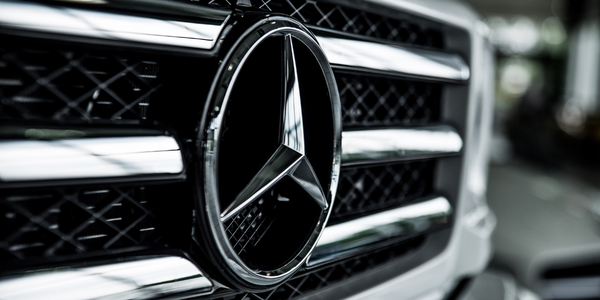
Case Study
Integral Plant Maintenance
Mercedes-Benz and his partner GAZ chose Siemens to be its maintenance partner at a new engine plant in Yaroslavl, Russia. The new plant offers a capacity to manufacture diesel engines for the Russian market, for locally produced Sprinter Classic. In addition to engines for the local market, the Yaroslavl plant will also produce spare parts. Mercedes-Benz Russia and his partner needed a service partner in order to ensure the operation of these lines in a maintenance partnership arrangement. The challenges included coordinating the entire maintenance management operation, in particular inspections, corrective and predictive maintenance activities, and the optimizing spare parts management. Siemens developed a customized maintenance solution that includes all electronic and mechanical maintenance activities (Integral Plant Maintenance).
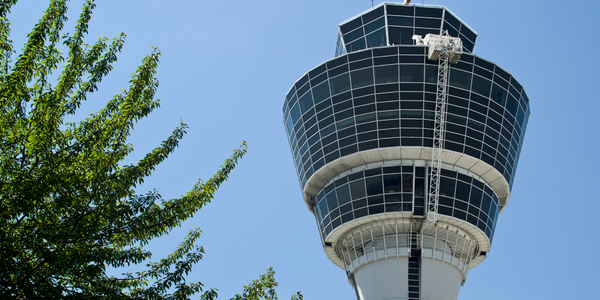
Case Study
Airport SCADA Systems Improve Service Levels
Modern airports are one of the busiest environments on Earth and rely on process automation equipment to ensure service operators achieve their KPIs. Increasingly airport SCADA systems are being used to control all aspects of the operation and associated facilities. This is because unplanned system downtime can cost dearly, both in terms of reduced revenues and the associated loss of customer satisfaction due to inevitable travel inconvenience and disruption.
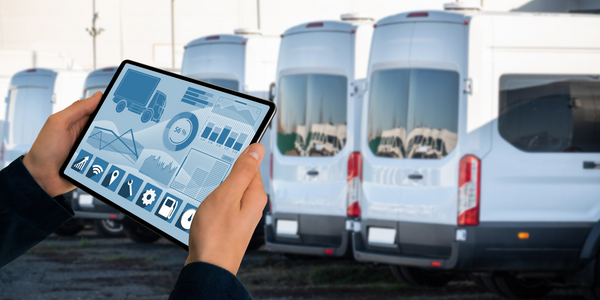
Case Study
IoT-based Fleet Intelligence Innovation
Speed to market is precious for DRVR, a rapidly growing start-up company. With a business model dependent on reliable mobile data, managers were spending their lives trying to negotiate data roaming deals with mobile network operators in different countries. And, even then, service quality was a constant concern.
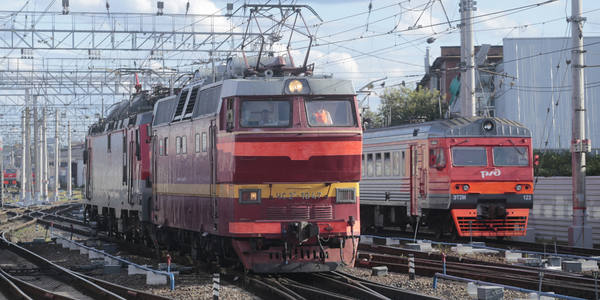
Case Study
Digitize Railway with Deutsche Bahn
To reduce maintenance costs and delay-causing failures for Deutsche Bahn. They need manual measurements by a position measurement system based on custom-made MEMS sensor clusters, which allow autonomous and continuous monitoring with wireless data transmission and long battery. They were looking for data pre-processing solution in the sensor and machine learning algorithms in the cloud so as to detect critical wear.