Customer Company Size
Large Corporate
Region
- Europe
Country
- Germany
Product
- Autodesk Inventor
- COMSOL Multiphysics
Tech Stack
- Numerical Simulation
- 3D Modeling
- Heat Transfer Modeling
Implementation Scale
- Pilot projects
Impact Metrics
- Innovation Output
- Productivity Improvements
- Customer Satisfaction
Technology Category
- Analytics & Modeling - Digital Twin / Simulation
- Analytics & Modeling - Predictive Analytics
Applicable Industries
- Battery
- Automotive
Applicable Functions
- Product Research & Development
- Quality Assurance
Use Cases
- Digital Twin
- Manufacturing Process Simulation
- Predictive Maintenance
Services
- Software Design & Engineering Services
- System Integration
About The Customer
NEXT ENERGY EWE Research Centre for Energy Technology at the University of Oldenburg, Germany, is a leading research institution focused on energy technology. The center collaborates closely with various academic and industrial partners to advance the understanding and development of energy systems, including lithium-ion batteries. The research team, led by Gerd Liebig and Pamina Bohn, is dedicated to investigating the thermal behavior of batteries during the manufacturing process. Their goal is to ensure the stability and capacity of batteries by understanding how elevated temperatures during manufacturing can affect the cells. The team employs advanced numerical simulation techniques to model different operating scenarios and validate their findings, providing valuable insights for the battery manufacturing industry.
The Challenge
The performance and durability of lithium-ion (Li-ion) batteries are heavily influenced by their operating temperature. Their performance decreases at low temperatures while the battery degrades quickly at high temperatures. This means that overall reliability is compromised, creating a potential safety issue. Industry research has led to standards regulating the ability of a battery to withstand fluctuations in temperature when it is in operation. In contrast, there has been much less focus on the temperatures that batteries are exposed to during the manufacturing process, which includes plasma pretreatment, UV curing, laser welding, ultrasonic joining, hot stacking, and hot gluing. A Li-ion battery may contain thousands of individual cells, which have to be stacked together. This is typically done through an assembling procedure that may involve various heat treatments, some of which can be extremely intense and expose the casing or other parts to high temperatures for short times. Gerd Liebig of NEXT ENERGY EWE Research Centre for Energy Technology at the University of Oldenburg, Germany, explained, “It is already well known that certain processes such as welding greatly increase the temperature within a battery. What is not known is the extent to which such elevated temperatures could propagate within and compromise a cell.”
The Solution
The research team from NEXT ENERGY EWE Research Centre for Energy Technology at the University of Oldenburg set out to investigate whether the manufacturing process could cause irreversible damage to lithium-ion cells due to elevated temperatures. They used numerical simulation to model different operating scenarios and placed probes to inspect results at any point in the model. The first step was to set up a physical experiment to measure temperatures reached inside a prismatic lithium dummy cell when subjected to short-term thermal stress. The goal was to collect data to validate the mathematical model and investigate the effect of various processes during cell manufacturing. The team created a 3D replica of a commercial prismatic lithium cell in Autodesk Inventor software and imported it into the COMSOL Multiphysics software. They modeled heat transfer by conduction due to an external heat source at different positions on the cell corresponding to different manufacturing processes, and the natural convective cooling on other areas of the cell surface. The physical and thermal properties of the individual materials were experimentally defined and mathematically homogenized into one jelly roll domain within a prismatic steel housing. Adaptive mesh refinement was used to adopt a finer discretization in regions where temperature gradients were higher, ensuring high-accuracy results.
Operational Impact
Quantitative Benefit
Case Study missing?
Start adding your own!
Register with your work email and create a new case study profile for your business.
Related Case Studies.
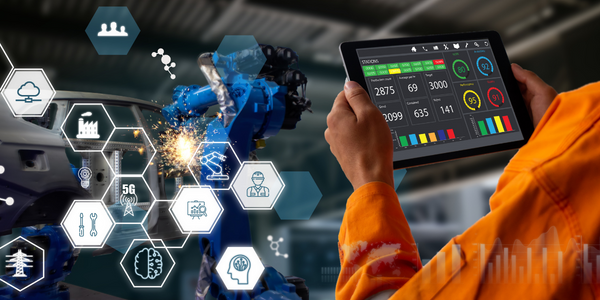
Case Study
Battery manufacturer Industrial Digital Twin
For optimum control of product quality, Banner relies on a high production depth. Its 560 production employees produce nearly all the components in¬-house that they need to make finished batteries on Banner’s six assembly lines. This includes the plastic parts for the battery cases as well as the paste-filled lead oxide grids. Their production involves two to five¬ days rest in maturing chambers to create optimum current absorption and storage capacity. Banner’s ongoing success was accompanied by a continuous, organic growth of the production facilities, adding or extending hall after hall until the complex filled the site that had seemed ever so spacious when the company moved here from a smaller place in 1959. These developments led to a heterogeneous production environment. “This confronts us with significant challenges, particularly concerning intra¬logistics issues, such as scheduling for the maturing chambers,” says Franz Dorninger, technical director at Banner. “We contemplated various ways to overcome this problem, including relocating to new premises.”
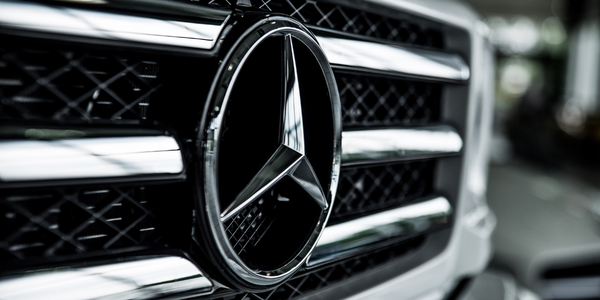
Case Study
Integral Plant Maintenance
Mercedes-Benz and his partner GAZ chose Siemens to be its maintenance partner at a new engine plant in Yaroslavl, Russia. The new plant offers a capacity to manufacture diesel engines for the Russian market, for locally produced Sprinter Classic. In addition to engines for the local market, the Yaroslavl plant will also produce spare parts. Mercedes-Benz Russia and his partner needed a service partner in order to ensure the operation of these lines in a maintenance partnership arrangement. The challenges included coordinating the entire maintenance management operation, in particular inspections, corrective and predictive maintenance activities, and the optimizing spare parts management. Siemens developed a customized maintenance solution that includes all electronic and mechanical maintenance activities (Integral Plant Maintenance).

Case Study
Monitoring of Pressure Pumps in Automotive Industry
A large German/American producer of auto parts uses high-pressure pumps to deburr machined parts as a part of its production and quality check process. They decided to monitor these pumps to make sure they work properly and that they can see any indications leading to a potential failure before it affects their process.