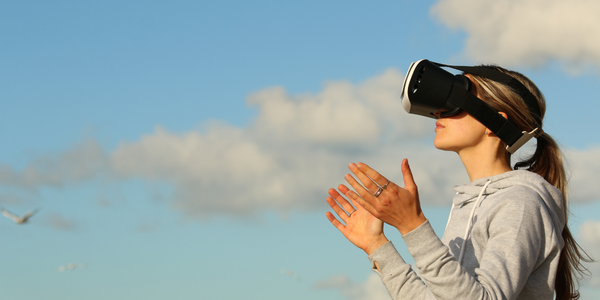
- Analytics & Modeling - Virtual & Augmented Reality Software
- Wearables - Augmented Reality Glasses, Headsets & Controllers
- Equipment & Machinery
- Discrete Manufacturing
- Augmented Reality
Scope AR collaborated with one of their large industrial clients to perform a side-byside comparison of Scope AR’s WorkLink software, an Augmented Reality software, versus using traditional paperbased methods to create manufacturing instructions. The client chose a complex assembly process for a proprietary spring-loaded hatch.
The assembly process contained over thirty steps that involved things such as fitting components at specific angles to ensure proper assembly, screwing down different screw types in correct locations, and grabbing parts that had similar exteriors.
The client chose this assembly process because it contained common steps that are frequently used in other processes as well as unique steps that are confusing and if done wrong would cause severe quality issues.
The client chose a competent computer user without any prior coding or 3D modeling knowledge to use WorkLink. After going through Scope AR’s standard tutorial and building a couple of sample projects, the user was timed to see how quickly he could create the assembly instructions using both WorkLink and traditional methods.
Once the instructions were built and deployed to the operators, the benefits for AR Smart instructions were evident. When operators used the Smart instructions, they were 30% faster than their counterparts who used paper-based instructions.
With the Smart instructions overlaid on top of the real-world object that needed to be assembled, operators were able to find the parts faster, they were able to understand the instructions clearer, and they ended up with three times fewer quality errors!
Case Study missing?
Start adding your own!
Register with your work email and create a new case study profile for your business.
Related Case Studies.
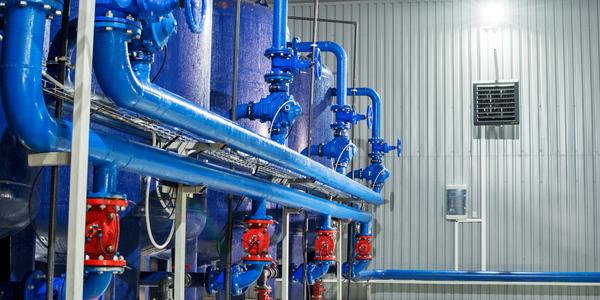
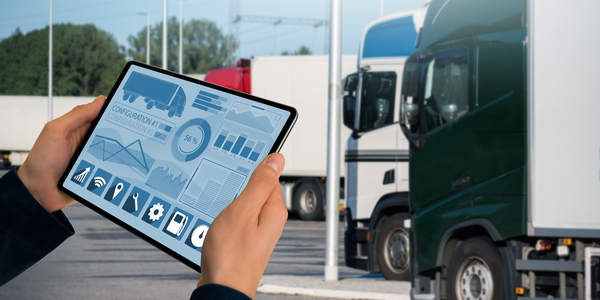
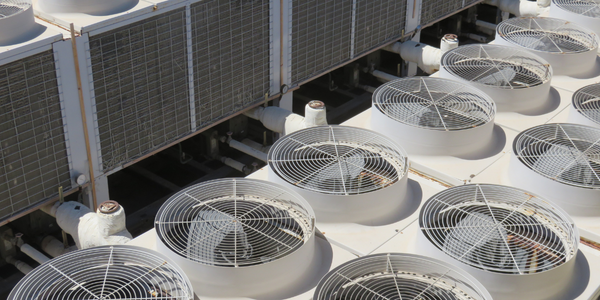
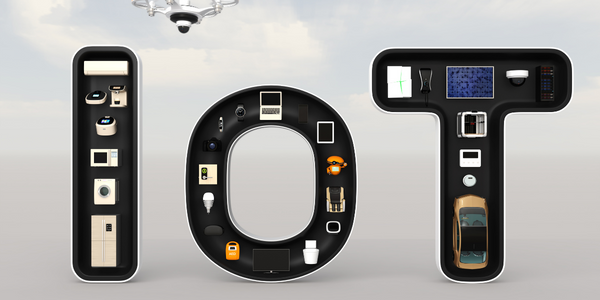
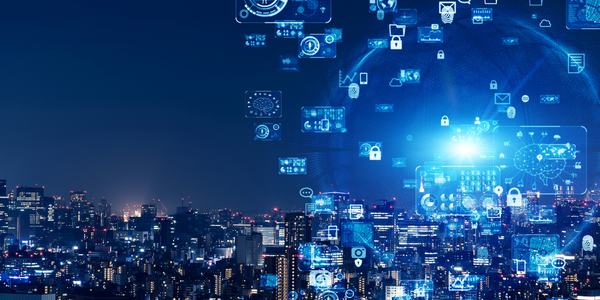
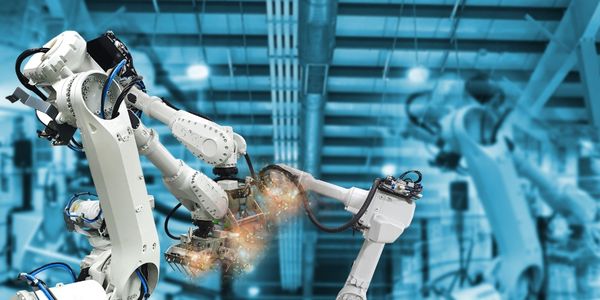