Technology Category
- Infrastructure as a Service (IaaS) - Private Cloud
- Infrastructure as a Service (IaaS) - Virtual Private Cloud
Applicable Industries
- Aerospace
- Buildings
Applicable Functions
- Product Research & Development
- Quality Assurance
Use Cases
- Onsite Human Safety Management
- Time Sensitive Networking
Services
- Testing & Certification
About The Customer
B/E Aerospace is a leading manufacturer of cabin interior products for commercial and private passenger aircraft. With design and manufacturing facilities across the globe, one of their leading products is their line of commercial and business airline seats. These seats are engineered and tested at its Commercial Airplane Products Group in Winston-Salem, North Carolina. B/E Aerospace designs commercial airline seats, along with many other furnishings for aircraft interiors, at its NC facility. Their design and finite-element analysis (FEA) teams share a motto: A Cheaper Ticket and A Safer Ride.
The Challenge
B/E Aerospace, a leading manufacturer of cabin interior products for commercial and private passenger aircraft, was faced with the challenge of designing lighter and safer seats for airline passengers. The rising fuel prices were forcing airlines to find inventive ways to reduce weight within an aircraft, which in turn would lower fuel costs and ultimately ticket prices. B/E Aerospace was tasked with not only reducing the weight of the seats but also ensuring that the components provide better passenger protection in emergencies. The design of these seats was completely market-driven, with airlines demanding comfort and features for their passengers, while also asking for lighter seats to combat the relentless increase in fuel costs. The challenge was to accommodate these demands within the constraints of safety certification.
The Solution
B/E Aerospace incorporated the use of HyperWorks and computer-aided engineering (CAE) into their product cycle. This was after witnessing the success of HyperWorks at their Miami facility, where engineers designed first-class seats for private jets. Altair Engineering, the company behind HyperWorks, placed one of its highly qualified engineers on site for three months to support the design of their latest commercial seat products. During this period, the on-site engineer demonstrated the benefits of CAE using HyperWorks tools. Lead structure and certification engineer, Yanbin Liu, was tasked with improving B/E’s design process by developing a process for virtual certification by incorporating advanced CAE methods. Using Altair HyperMesh and the topology optimization capabilities of Altair OptiStruct early in the design process, Dr. Liu was able to reduce the weight of a typical leg-and-spreader unit for analysis by 32 percent.
Operational Impact
Quantitative Benefit
Case Study missing?
Start adding your own!
Register with your work email and create a new case study profile for your business.
Related Case Studies.
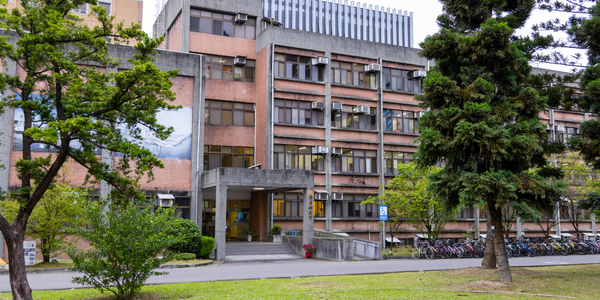
Case Study
Energy Saving & Power Monitoring System
Recently a university in Taiwan was experiencing dramatic power usage increases due to its growing number of campus buildings and students. Aiming to analyze their power consumption and increase their power efficiency across 52 buildings, the university wanted to build a power management system utilizing web-based hardware and software. With these goals in mind, they contacted Advantech to help them develop their system and provide them with the means to save energy in the years to come.
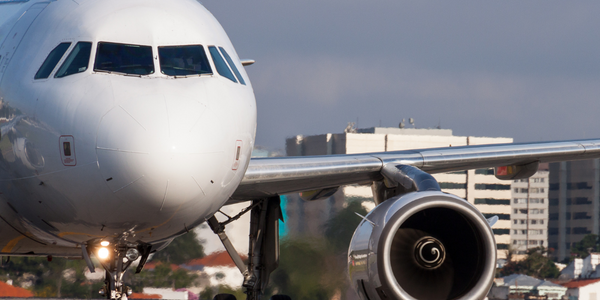
Case Study
Airbus Soars with Wearable Technology
Building an Airbus aircraft involves complex manufacturing processes consisting of thousands of moving parts. Speed and accuracy are critical to business and competitive advantage. Improvements in both would have high impact on Airbus’ bottom line. Airbus wanted to help operators reduce the complexity of assembling cabin seats and decrease the time required to complete this task.
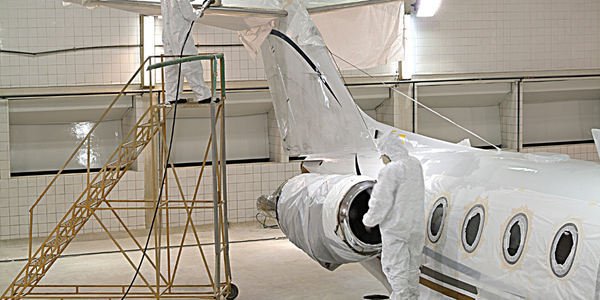
Case Study
Aircraft Predictive Maintenance and Workflow Optimization
First, aircraft manufacturer have trouble monitoring the health of aircraft systems with health prognostics and deliver predictive maintenance insights. Second, aircraft manufacturer wants a solution that can provide an in-context advisory and align job assignments to match technician experience and expertise.
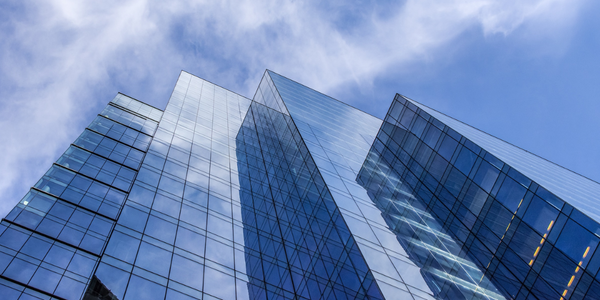
Case Study
Intelligent Building Automation System and Energy Saving Solution
One of the most difficult problems facing the world is conserving energy in buildings. However, it is not easy to have a cost-effective solution to reduce energy usage in a building. One solution for saving energy is to implement an intelligent building automation system (BAS) which can be controlled according to its schedule. In Indonesia a large university with a five floor building and 22 classrooms wanted to save the amount of energy being used.
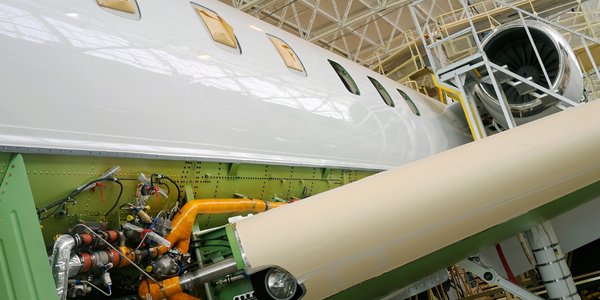
Case Study
Aerospace & Defense Case Study Airbus
For the development of its new wide-body aircraft, Airbus needed to ensure quality and consistency across all internal and external stakeholders. Airbus had many challenges including a very aggressive development schedule and the need to ramp up production quickly to satisfy their delivery commitments. The lack of communication extended design time and introduced errors that drove up costs.
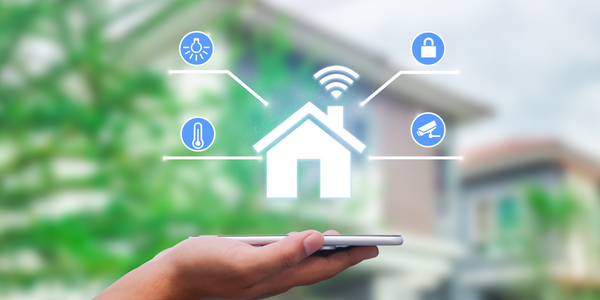
Case Study
Powering Smart Home Automation solutions with IoT for Energy conservation
Many industry leaders that offer Smart Energy Management products & solutions face challenges including:How to build a scalable platform that can automatically scale-up to on-board ‘n’ number of Smart home devicesData security, solution availability, and reliability are the other critical factors to deal withHow to create a robust common IoT platform that handles any kind of smart devicesHow to enable data management capabilities that would help in intelligent decision-making