Technology Category
- Analytics & Modeling - Digital Twin / Simulation
- Sensors - Haptic Sensors
Applicable Industries
- Aerospace
- Transportation
Applicable Functions
- Product Research & Development
- Quality Assurance
Use Cases
- Transportation Simulation
- Virtual Prototyping & Product Testing
Services
- Testing & Certification
About The Customer
Assystem is an international engineering and innovation consultancy group with a presence in 14 countries and 8500 employees. With main offices in Bristol, Derby, Preston, and Sunderland, UK, they are supported by 1400 staff delivering key capabilities in a wide array of industries, from Aerospace and Energy (including nuclear power) to Defence and Transport. As a leading European independent nuclear engineering specialist, Assystem is involved throughout the cycle, from fuel production to reprocessing to the design, commissioning, and decommissioning of nuclear installations.
The Challenge
Assystem UK Ltd, an international engineering and innovation consultancy group, was tasked with the design, simulation, prototyping, and verification testing of an encapsulation vessel for a customer in the nuclear industry. The challenge was to create an overpack, a protective barrier for product cans, that could withstand dynamic loading, such as being dropped during transit or falling to the ground in storage. The design had to endure drop heights of 3.5m (during transportation within the plant) and 1.5m (within the storage facility), with impact onto either a flat surface or an angled target. Additionally, due to the potential for internal pressurisation from gases inside the product can, the assembly had to be designed as a pressure vessel according to the rules of PD5500 and demonstrate a design life of 10 years.
The Solution
Assystem utilized the HyperWorks tools - HyperMesh, HyperView, RADIOSS, and HyperStudy - to design and develop the overpack. HyperMesh was used to mesh the design of the overpack components, which were then analyzed using RADIOSS. The RADIOSS solver was also crucial in simulating the pressurisation of the overpack at the moment of impact. Various drop scenarios of pressurised and non-pressurised overpacks were simulated to establish the worst-case impact orientations. A Design of Experiments approach was used with HyperStudy to rapidly generate, run, and post-process the impact scenarios. The results from each drop simulation were reviewed, and a small number of design iterations took place to refine the design, ensuring that it complied with PD5500.
Operational Impact
Quantitative Benefit
Case Study missing?
Start adding your own!
Register with your work email and create a new case study profile for your business.
Related Case Studies.
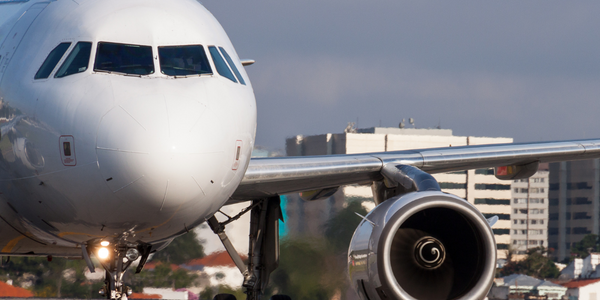
Case Study
Airbus Soars with Wearable Technology
Building an Airbus aircraft involves complex manufacturing processes consisting of thousands of moving parts. Speed and accuracy are critical to business and competitive advantage. Improvements in both would have high impact on Airbus’ bottom line. Airbus wanted to help operators reduce the complexity of assembling cabin seats and decrease the time required to complete this task.
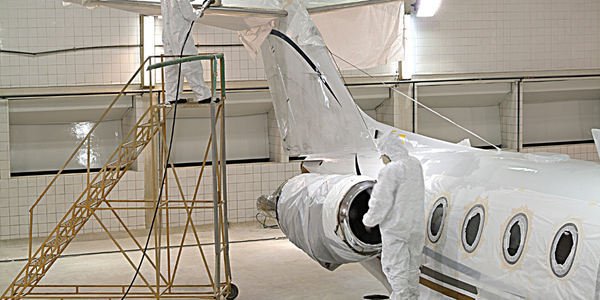
Case Study
Aircraft Predictive Maintenance and Workflow Optimization
First, aircraft manufacturer have trouble monitoring the health of aircraft systems with health prognostics and deliver predictive maintenance insights. Second, aircraft manufacturer wants a solution that can provide an in-context advisory and align job assignments to match technician experience and expertise.
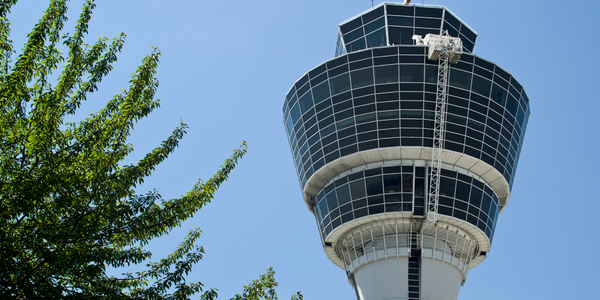
Case Study
Airport SCADA Systems Improve Service Levels
Modern airports are one of the busiest environments on Earth and rely on process automation equipment to ensure service operators achieve their KPIs. Increasingly airport SCADA systems are being used to control all aspects of the operation and associated facilities. This is because unplanned system downtime can cost dearly, both in terms of reduced revenues and the associated loss of customer satisfaction due to inevitable travel inconvenience and disruption.
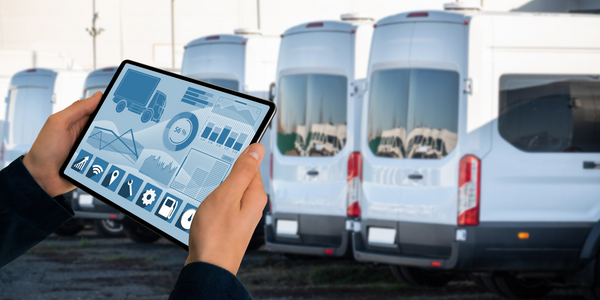
Case Study
IoT-based Fleet Intelligence Innovation
Speed to market is precious for DRVR, a rapidly growing start-up company. With a business model dependent on reliable mobile data, managers were spending their lives trying to negotiate data roaming deals with mobile network operators in different countries. And, even then, service quality was a constant concern.
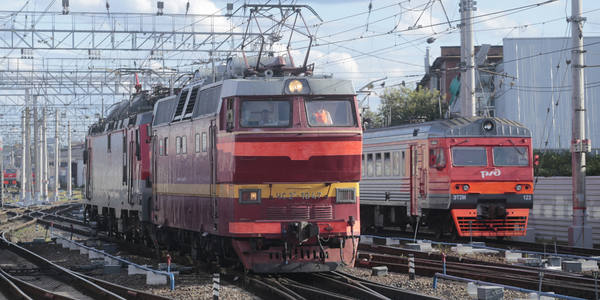
Case Study
Digitize Railway with Deutsche Bahn
To reduce maintenance costs and delay-causing failures for Deutsche Bahn. They need manual measurements by a position measurement system based on custom-made MEMS sensor clusters, which allow autonomous and continuous monitoring with wireless data transmission and long battery. They were looking for data pre-processing solution in the sensor and machine learning algorithms in the cloud so as to detect critical wear.
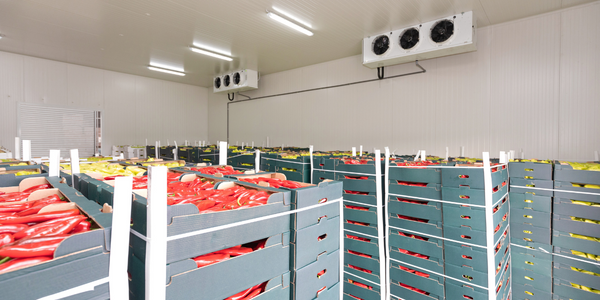
Case Study
Cold Chain Transportation and Refrigerated Fleet Management System
1) Create a digital connected transportation solution to retrofit cold chain trailers with real-time tracking and controls. 2) Prevent multi-million dollar losses due to theft or spoilage. 3) Deliver a digital chain-of-custody solution for door to door load monitoring and security. 4) Provide a trusted multi-fleet solution in a single application with granular data and access controls.